This article provides an overview of impact of shielding materials on shielding effectiveness. The post is based on Würth Elektronik‘s “Reference Guide ABC of Shielding” that can be ordered from WE website here. Published under permission by Würth Elektronik.
The fundamental principle of shielding enclosures against electromagnetic fields is to construct a Faraday cage around an electrical device.
If PCBs and internal cabling are meticulously designed, the amount of enclosure shielding required can be significantly reduced. However, if it becomes evident that enclosure shielding is necessary, the design of the enclosure to meet EMC requirements will become a crucial cost factor for the product.
A shielded enclosure must be constructed using materials that possess the requisite electrical properties and adhere to the application-specific requirements. Discontinuities, such as housing openings, seams, and sheet metal overlaps, should be minimized and designed in a manner that maintains the effectiveness of the housing shielding.
This can be achieved through the appropriate use of EMI shielding gaskets, ventilation, window shields, and shielded and filtered peripheral cables. The materials employed in the manufacture of enclosures include metal sheet and foil, non-metallic materials like plastic materials with conductive coatings, conductive plastics, and various composites.
Metal Sheets
Metal sheets are effective in shielding electrical (high-impedance) fields due to their high conductivity, as illustrated in Figure 1.
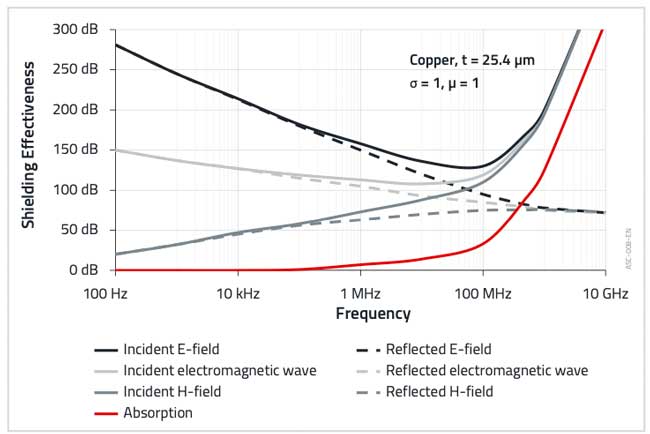
The shielding effect for electric fields is infinite for direct current and decreases with increasing frequency. However, magnetic fields are more challenging to shield. As frequency decreases, non-magnetic materials like aluminum exhibit reduced reflection and absorption losses, making it difficult to shield magnetic fields using them.
At high frequencies, the shielding effectiveness is high due to reflection and absorption losses, so the choice of materials becomes less critical. Regarding plane waves, magnetic materials offer better absorption attenuation, while well-conducting materials provide better reflection attenuation. Table 1. provides a qualitative overview of these parameters.
Some of the values in Table 1. are quite high because they were measured in the laboratory under ideal conditions for comparison purposes and are rarely achieved in practice. It is often assumed that materials with sufficient structural stiffness also have sufficient thickness to achieve a sufficient shielding effect. However, this is not always the case for devices operating in the low-frequency range (typically <100 kHz). At these low frequencies, it is necessary to use a highly permeable material to achieve sufficiently high shielding effectiveness against magnetic fields.
Plastics with Shielding Attenuation Properties
Plastics, synthetic materials derived from raw materials called monomers, exhibit diverse physical properties like melting point, strength, and formability. However, these properties can hinder their processing and usability. Composite materials have emerged as a solution to address these shortcomings. Composite materials are combinations of two or more materials designed to achieve a property that none of the individual materials can provide. This combination often results in enhanced strength, but it can also increase electrical conductivity and improve electromagnetic shielding properties.
To improve the electrical and electromagnetic properties of plastics, graphite mats or other materials can be used, such as the addition of conductive fillers. Typical conductive fillers are graphite flakes, metal-coated graphite fibres, and metal flakes or fibres. The resistivity of carbon fibre composites ranges from 4 mΩ/cm to some 100 mΩ/cm, depending on the number of layers and their weaving angle.
This is three to four orders of magnitude greater than copper or aluminum. Thus, most composites pose serious problems for electrical connections. The establishment of low-impedance and long-term reliable electrical contact between a housing ground and the electronics is essential for a functioning EMC concept. The conductivity of the housing surface can also be achieved by integrating a conductive screen or by coating the housing with conductive paint. The technologies used to apply conductive enclosure coatings include flame spraying, arc spraying, vacuum metallization, painting with conductive paints, and covering with conductive foil. This can further improve the surface conductivity of composite materials. Surface resistance can thus be reduced to 5 to 100 mΩ/cm.
All these plastics with shielding attenuation properties offer a certain degree of attenuation within a limited frequency range. Table 2. compares the conductivity and magnetic permeability of various materials. It’s evident that only materials containing ferromagnetic components exhibit effective attenuation of low-frequency magnetic field components, as only these have a magnetic permeability exceeding 1.
Plastic housings have a crucial aspect to consider: their interference resistance against electrostatic discharges. Materials with a specific surface resistance of less than 1 · 107 Ω/square can accumulate static charge if electrically connected to a conductive structure like a wire, allowing the charge to flow. Conversely, materials with a resistivity of more than 1 · 1013 Ω/square can build up static charge that remains undissipated even when the housing is grounded by a conductor.
Graphite-reinforced materials are generally conductive enough to prevent static charge buildup when graphite particles protrude through the plastic to the surface. In contrast, epoxy resin surface coatings lack conductivity, necessitating an additional conductive coating in certain cases.
Related articles: