This study by Dr. V. Azbel, independent consultant on tantalum capacitors, investigates the electrical characteristics of anodes made from tantalum capacitors, focusing on the impact of oxygen in the sintered pellet and the effects of deoxidation and temperature and overall tantalum capacitor quality.
Optimal parameters for the deoxidation process are identified to improve anode reliability and performance.
The results provide recommendations for enhancing the quality and reliability of tantalum anodes.
Introduction
Tantalum capacitors are crucial in electronics due to their high performance and reliability. The oxygen content in the sintered pellet before electrolysis significantly affects their reliability.
The natural oxide layer of tantalum is about 3 nm thick, meaning that the oxygen content in the powder or sintered pellet should directly depend on the surface area (see Fig. 1). According to the study, the oxygen/BET ratio is approximately 3000 ppm/(m²/g).
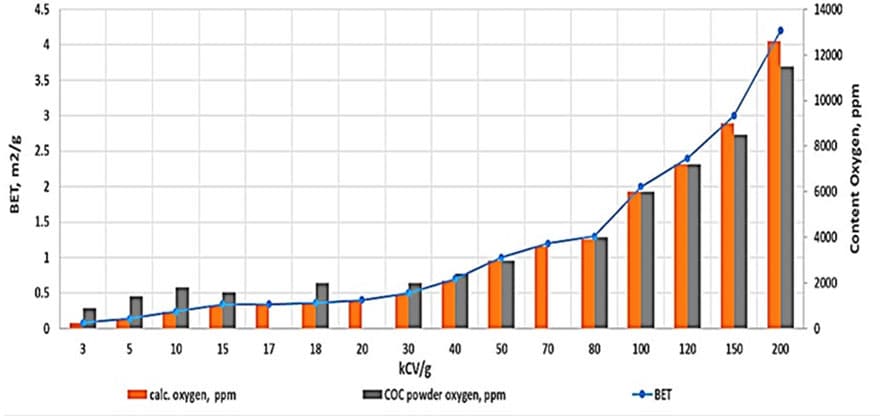
The relationship between BET surface area and CV/g and oxygen content in tantalum powders:
- BET surface area (m²/g) compared to (CV/g) / 1 /— blue line.
- Calculated oxygen content in the powder according to its BET (ppm)/2/ — orange bars.
- Average oxygen content in powders of the same CV/g from different manufacturers /3.4/— black bars (OTIC, Ulba, GAM, H.C.Starck). This graph illustrates the correlation between BET surface area, CV/g, calculated, and actual oxygen content in tantalum powders. As seen from Fig. 1, for powders with CV/g ≥ 30, the calculated and actual oxygen values are close.
Oxygen in Sintered Porous Tantalum Pellet
Pure tantalum contains negligible free oxygen due to its high reactivity, forming oxides. Therefore, free oxygen in the tantalum matrix is practically absent. Experiments with tantalum foil show how deoxidation affects oxygen content.
To assess the oxygen content in the tantalum matrix, experiments were conducted on tantalum foil with 99.99% purity before and after deoxidation (DEOX) at 1000°C for 3 hours. At room temperature, the oxygen content changed from 550 ppm to 150 ppm (see Fig.2).
This suggests that upon cooling, excess oxygen that cannot remain dissolved in tantalum at room temperature will precipitate and form tantalum oxide on the surface. The solubility of oxygen in tantalum is illustrated in the graph in Fig. 3.
The formation of tantalum oxide can cause internal stresses depending on several factors, such as the difference in the coefficients of volumetric expansion between tantalum and tantalum oxide, the increase in oxide film thickness, and the cooling rate. If the oxide film forms evenly and slowly, internal stresses may be minimal. The thickness of the oxide film will also depend on the temperature of oxygen solubility.
To better understand the behavior of oxygen in tantalum during sintering, the following schematic explains the oxygen behavior at various stages of the sintering process (Fig. 4).
For example, powders with a specific surface area of 150 m²/g contain about 9000 ppm of oxygen, and the maximum usable sintering temperature does not exceed 1300°C (see Fig. 3). The solubility of oxygen at this temperature is up to 4000 ppm, which means that about 5000 ppm remains in the form of an oxide film on the surface, to which, after sintering, is added a movie of oxygen precipitated from the matrix at room temperature.
During air passivation, if the oxide film is already formed and stable, without internal stresses, the additional oxygen content may not increase significantly and DEOX is not required. However, it is important to consider the passivation recipe so that internal stresses do not form in the sintered pellet after cooling, before passivation, which will affect the characteristics of the resulting oxide film. The thickness and characteristics of the oxide film on the surface significantly depend on the oxygen content in the used powder (see Fig. 1) and its sintering temperature (see Fig. 5).
Impact of the Deoxidation Process on the Electrical Characteristics of Anodes
Deoxidation reduces oxygen content, improving anode electrical properties. This section examines the impact of deoxidation temperature and time on these properties, using different sintered pellet designs. Two sintered pellet designs with the same sintering temperatures were used for the analysis, but one of them additionally underwent deoxidation. Fig.6 demonstrates the mechanical and electrical characteristics of anodes made from these pellets.
Changes in oxygen content (O, ppm), yield strength (Ay, kg/mm²), work hardening coefficient (n), capacitance (Cap, µF), and leakage currents (DCL, µA). With the same porosity, higher Ay values are due to the high concentration of oxides, which prevent the onset of plastic deformation. This is confirmed by increasing n values, indicating material defectiveness.
Influence of Deoxidation Temperature and Time
The deoxidation process in a magnesium atmosphere, ranging from 800°C to 1000°C, is analyzed. The optimal balance between oxide reduction, DCL/CV decrease, and capacitance loss is determined (see Fig. 7).
The selected temperature range for deoxidation, in an atmosphere magnesium is between its melting point of 650°C and its boiling point of 1090°C. The reaction at 800°C can take several to several tens of minutes depending on conditions (pressure, particle size, etc.), while at 1000°C it proceeds much faster and can be completed within a few minutes.
To determine the evaporation time of magnesium at 800°C and 1000°C under atmospheric pressure, we use the Knudsen equation for the evaporation rate (see Appendix 1).
Consequently, the deoxidation temperature range is below the sintering temperatures. At deoxidation temperatures, there is no decrease in bulk shrinkage. It may remain unchanged or, for some designs, even lead to a slight increase. This study analyzed various temperatures and durations of deoxidation in a magnesium atmosphere to determine their impact on the electrical characteristics of tantalum anodes. The deoxidation temperature varied between 800°C and 1000°C.
Patent [5] provides a table (see Table 1) showing the impact of different deoxidation temperatures on specific capacitance (CV/g) and oxygen content in the powder. According to this table, increasing the deoxidation temperature leads to a reduction in oxygen content and an improvement in specific capacitance (CV/g). This data underscores the importance of temperature control in deoxidation to achieve optimal electrical characteristics of tantalum anodes (see Fig.7).
Reduction in oxygen content with increasing deoxidation temperature and time. Decrease in DCL/CV. (see Fig.7)
Reduction in capacitance with increasing temperature and processing time. For the sintered pellet design studied, the optimal balance between oxide content reduction, DCL/CV decrease, and capacitance loss was achieved at a temperature of 1000°C and a processing time of 2 hours.
Surface Changes in Sintered Porous Pellets and Electrical Properties
The effects of deoxidation on the porous structure, surface diffusion, and electrical properties are examined. The increase in surface diffusion rate and its impact on specific capacitance are highlighted.
Consider the processes occurring in the porous structure during DEOX. Tantalum oxide, after sintering a porous pellet, is located on the surface of the particles. As a result of the dissociation of tantalum oxides upon contact with magnesium, small particles of tantalum and magnesium oxide are formed. This leads to an increase in the rate of surface diffusion, which in turn promotes surface smoothing, relaxation of surface stresses, and adhesion of fine tantalum particles formed on the surface after DEOX. Consequently, the surface area decreases.
When the temperature increases from 850°C to 950°C, and in the absence of tantalum oxide on the particle surface, the rate of surface diffusion of tantalum increases approximately threefold, which, according to calculations (see Appendix 2), leads to a 26% reduction in surface area. This correlates with the change in specific capacitance (CV/g) and confirms the influence of the rate of tantalum diffusion on the structure and properties of sintered pellets. Therefore, it can be assumed that, in this temperature range, the controlling process of structural changes is the surface diffusion of tantalum.
Appendix
Table 1
Tantalum Powder for the Production of Solid Electrolyte Capacitors, US 2008.0094779A1
1. The Knudsen equation can be written as follows:
where:
- R — evaporation rate (g/cm²·s),
- α — evaporation coefficient (for magnesium ≈ 1),
- P — vapor pressure (Pa),
- M — molecular mass of magnesium (0.024305 kg/mol),
- R — universal gas constant (8.314 J/mol·K),
- T — temperature (K).
For magnesium, the vapor pressure at 850°C and 1000°C, taken from tables, is approximately:
- At 850°C: P ≈ 0.1 atm
- At 1000°C: P ≈ 0.5 atm
2. Calculation of the Reduction in Pore Surface Area
Surface Diffusion and Pore Sintering: An increase in the surface diffusion rate by an order of magnitude (Ds′ = 10Ds) accelerates the processes that reduce the pore surface area.
The pore radius R changes with time t according to the surface diffusion equation:
With an increase in Ds by an order of magnitude:
Pore Surface Area: The surface area of the pores is proportional to the square of their radius:
S∞R²
Ratio of Pore Surface Areas Before and After Increase in Ds:
An order of magnitude increase in surface diffusion can reduce pore surface area by 20-30%, significantly impacting porous material properties.
Findings include:
1. Oxygen content and electrical properties. Excessive oxygen content relative to the surface of the sintered pellet leads to the formation of crystalline oxides on the surface of the sintered particle, negatively affecting the electrical properties of tantalum anodes. The study confirms that reducing the oxygen content through an effective deoxidation process improves these properties.
2. Effect of temperature and time. Deoxidation at temperatures between 800°C and 1000°C is critical. Increasing the temperature and increasing the deoxidation time effectively reduce the oxygen content, although excessive temperature or prolonged processing may result in loss of capacity. For a given anode design, the optimal temperature and deoxidation time of the sintered pellet, have been established.
3. Structure stability after deoxidation. The structure of the sintered pellet, formed after the deoxidation process, when re-sintered under the same conditions, as before deoxidation, does not lead to increased internal stresses. This is indicated by the oxygen content, which is close to the content in the powder, and the characteristics of Ay and n (see Fig. 6).
Conclusions and Recommendations
Precise control of deoxidation temperature and time is necessary to enhance the electrical performance and reliability of tantalum anodes. The study confirms that reducing the oxygen content improves electrical properties and stabilizes the structure, which reduces the risk of internal stress in the pellets during subsequent sintering.
Reference
- Magnesium Vapor Reduced Tantalum Powders with Very High Capacitances Helmut Haas CARTS Europe 2004
- Tantalum Capacitor Anodes Providing Highest Capacitances: Where Are the Limits? Helmut Haas CARTS Europe 2011
- A New Era for High CV/g Tantalum Powders J. Koenitzer, T. Izumi, and L. Mann Cabot Supermetals
- TA1048 Capacitor Grade Tantalum Powder (above 60V) Standford Advanced Materials www.samaterials.com/tantalum/1048-capacitor-grade-tantalum-ta-powder-above-60v.html
- Patent “Tantalum Powder for the Production of Solid Electrolyte Capacitors, US 2008.0094779A1”