The purpose of the work is to propose a method for predicting the reliability of a capacitor by leakage currents (DCL), which allows predicting the behavior of DCL, already at the initial stages of anode manufacturing, based on the mechanical tests, which significantly reduces the time and cost at its manufacture.
The paper was presented by Vladimir Azbel, independent consultant, Israel at the 3rd PCNS 7-10th September 2021, Milano, Italy as paper No.1.6.
METHODS TO CONTROL RELIABILITY OF TANTALUM CAPACITORS
Usually, deficiency of control methods in the early stages of manufacture of the product, with a multi-step process, leads to the search results of trial and error, which leads to a waste of time and money with a low probability of solving the problem. The reliability of the tantalum capacitor, its capacitance (CAP), and above all, the leakage currents, and their stability, are determined by the anode.
METHODS TO CONTROL RELIABILITY OF TANTALUM CAPACITORS FROM EARLY ANODE PRODUCTION STAGE
One of the ways to increase the reliability of the anode is the development of new effective control methods on the stage of its production. The anode is the heart of the tantalum capacitor.
Anode production – imagine how, as the two-stage process:
- the first stage is getting a sintered pellet.
- the second stage is getting anode, by the formation process of a sintered pellet. The CAP and DCL values of the anode, produced at the same powder, depend on choosing the parameters first and the second stage:
- for sintered pellet, this choice of the pressing density, and temperature sintering
- The only controlled parameter of the process is shrinkage. It should be noted that shrinkage depends on the temperature/time of sintering and does not depend on the change in the pressing density at the same sintering temperature
- the second stage is the formation of the process of the sintered pellets and define of CAP and DCL.
Most of the tantalum capacitors manufacturers nowadays use for determining anode quality “wet-cell” tests (WC). The WC test is a good indicator of overall anode capacitance (CAP) and dissipation factor (DF) but insufficient to precise prognoses direct current leakage (DCL) on the final product and does not provide a direct connection to the structure of the sintered pellet.
The problem is that at present the quality assessment can be carried out only on the anode, and any deviation, in consisting of its components from the recipe process associated with the repetition of all stages of its manufacture.
Unfortunately, WC the test does not provide:
- current control of the sintered pellet, which is currently controlled by shrinkage, which has its own limitations / 1/.
- control defects, at each technological stage
- predicting risk degradation of the DCL in the final product.
Mechanical Test
Consider the possibility of estimate CAP and DCL of anode not by WC, but by mechanical tests, applied to porous materials.
The proposed method is based on recording the stress-strain curve of the material, which makes it possible to independently control, not only, changes in the porous structure, but and residual stress of the sintered pellet (at variations in the pressing density and sintering temperature), and the ability of the structure of the sintered pellet to resist the change, during the formation of an amorphous Ta2O5 film during the formation process.
The typical form of the CC curve and the parameters characterizing it are shown in Fig.1
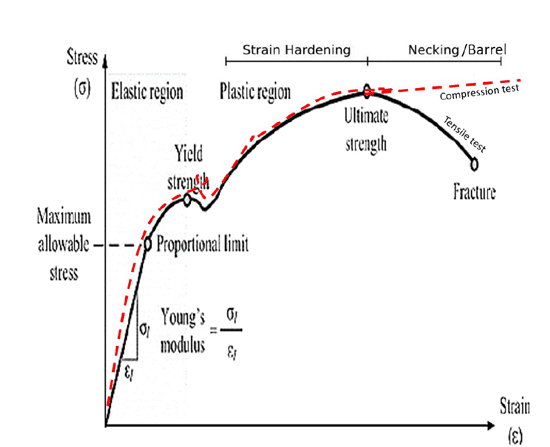
The stress-strain curve provides information about the structure, which affects its parameters of yield strength (Ay), Young’s modulus (E), ultimate tensile stress (AUTS), exponential hardening factor (n), which is also true for porous materials.
The characteristics of the SS curve are widely used to assess the quality and reliability of the material, in particular powder porous materials, after various technological processes subjected to mechanical, thermal, and chemical treatment.
In the case of a composite material, which is an anode, the stability of its properties:
- first of all, will depend on the ability of its plastic matrix (sintered pellet) to withstand degradation caused by the formation process
- keep stability during exploitation.
An indicator, of the stability of anode properties, is the stability of its structure, after a reliability test, can be estimated by:
- standard method determined CAP and DCL on the capacitor
- suggested method / 5 /- Ay, E, and n determined from the SS curve of the anodes before and after heating in air, in the temperature/time range 400-450°C/20 – 60 min., should not exceed 10%.
HOW TO CONTROL FEATURES OF THE SINTERED PELLET
1.Press Density
Shrinkage value of pellets, pressed with different densities and sintered at the same temperature does not change and is not an indicator of changes in the porous structure. Currently, control of the sintered pellet, by volume shrinkage. A higher in the press density pellet leads to an increase: E~ k1- decrease porosity sinter pellet and a decrease in the CV/g of anodes produced from these sintered pellets.
2.Sintering Temperature
The influence temperature sintering on Ay and k1 of sintered pellets and CV/g anode can be investigated. An increase in the sintering temperature, similar to an increase in the pressing density, leads to an increase in Ау, к1 and a decrease in CAP (CV/g) change.
3.Sintering Time
The influence time sintering on Ay and k1 of sintered pellets and CV/g, DCL/CV anode is another variable to consider. An increase in the sintering time leads to similar changes CV/g and DCL/CV as an increase in the pressing density and sintering temperature.
From our experimental results, it can be seen, that there is a correlation between the parameters Ay, k1 of the sintered pellet and CV/g, DCL/CV of the anode, depending on the variation of the pressing density, temperature, and sintering time. At the same time, to predict DCL, the Ay parameter is used, which is responsible for the size of the neck of the sintered pellet and the recipe for the formation of the anode.
4.Formation Process
The anode is a composite material, and unlike the test used to predict the stability of the DCL on the final anode, the mechanical test it possible to make such an estimate of the compatibility of the parameters Ау and the length of the plasticity region (Ls) of the sintered pellet and Av and Lv after formation (on the anode). The parameters Ay and the Ls of the sintered pellet, depend on powder, the press. density, temperature/time of sintering, and Av, Lv, from recipe formation (formation voltage and current, etc).
The scheme of the effect of formation voltage on the size neck, indicate an increase in the risk of overheating during formation.
5. Powder Vendors Benchmark
The different vendor powder, leads to significantly different DCL, it can be checked by standard powder parameters evaluation.
Comparison of the size of the neck obtained from the stress–strain curve, after sintering, allows predicting the acceptance of the powder in the early stages of production, significantly reduces the time and cost spent for powder conversion.
6. Powder Batch Acceptance Criteria
On sintered pellet from acceptable and problematic batches, SS- curves can be obtained and compared.
7. Using SS Curve to Monitor Anode Pellet Shape Influence on Ау and DCL
Pellets A and B were prepared at the same: grade powder, press density, temperature/time sintering, formation voltage have at the same shrinkage, and content oxygen. Anode, produce by sintered pellet B, has low values of Ау and burns out on formation.
SUMMARY & CONCLUSION
SUMMARY & CONCLUSION
The proposed method makes it possible to control the quality of the sinter and anode in comparison with their benchmark values E and Ay (curve SS), for which acceptable electrical characteristics of the anode were obtained.
Using of mechanical test could help to:
- Improve effectiveness of powder conversion. (since allow direct measurements and comparison of pellet with different powders at different manufacturing steps)
- Control pelleting “process” to reduce lot-by-lot variation (for special products).
- Reduce cost and increase effectiveness of new pellet developing. (achieving measurable data at early manufacturing steps)
- Evaluate effectiveness and necessaries of different manufacturing steps/treatments.
- Specific Ta pellets design optimization.
This article is shortened version of original paper available at the link below or pdf download.