Knowles Precision Devices released white paper on why bidirectional EV charging requires special attention to design.
As interest and adoption increase in the electric vehicle (EV) arena, associated technologies are advancing quickly.
Batteries are becoming more powerful and charging infrastructure is increasingly robust and efficient. With all these advancements, EV batteries are good for more than powering cars on the road.
Bidirectional charging capabilities are the next big perk for EV owners. Perfecting this technology means EV batteries can fuel vehicles and private homes or local grids. Right now, OEMs are part of a huge push to make bidirectional chargers resilient and reliable.
How Does Bidirectional Charging Work?
When an EV is charging, alternating current (AC) from the grid is converted into direct current (DC) electricity, which can be used by the vehicle. This conversion can be performed by the vehicle’s converter, or a converter located inside the charging apparatus.
During this process, semiconductors located inside the converter switch at high speeds to create a waveform that mimics DC electricity. In a unidirectional charging scenario, diodes continue sending current forward in one direction—towards the vehicle.
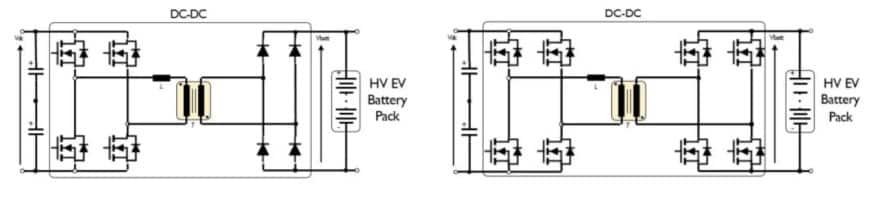
Replacing diodes with semiconductors, see Figure 1, allows waveforms to be made on the primary and secondary sides of the converter, so current can flow in either direction—towards the vehicle or towards the grid. Since semiconductor switching creates so much electrical noise, and there are so many more of them in bidirectional chargers, smoothing and filtering ceramic capacitors, like snubber capacitors, are implemented to smooth and reduce all of that noise.
Why Use Bidirectional Charging in the First Place?
Even with all the excitement, battery economics is a central concern with more devices and systems on the grid. What happens when the grid gets overloaded? Experts believe that vehicle-to-grid charging is one way to manage demand-response capabilities.
Bidirectional chargers regulate the flow of electricity in both directions, which allows EV batteries to charge from the grid and discharge electricity back into the grid to power a home, office, or appliance during an outage. In other words, vehicles can pick up the slack when grids inevitably fail due to factors like weather or overload.
What are the Greatest Design Challenges Associated with Bidirectional EV Charging?
To serve their critical function, bidirectional chargers need to comply with local grid requirements, which vary across localities. Designers are tasked with ensuring communication devices and circuits can accommodate different voltages (e.g., 230V vs. 110V) and frequencies (e.g., 50Hz vs. 60Hz) depending on where the driver lives and travels to ensure safe, reliable charging and discharging.
Since bidirectional chargers send current in two different directions using one circuit, their components will experience more wear. Wear leads to overheating, voltage spikes, and current surges that could pose safety concerns. Each component in the system must be designed for longer device life and a higher number of charge/discharge cycles. Along the same lines, efficiency becomes a more critical constraint because these chargers experience a higher number of power conversion cycles than unidirectional chargers.
Adding active switches to the secondary side of the converter for bidirectional charging adds complexity to the overall design. Components must be carefully selected to handle high power without compromising safety or reliability.
For more information on bidirectional EV charging, see Knowles white paper, Making Electric Vehicle Wireless Charging a Reality.