Vladimir Azbel published an article on his LinkedIn profile on reliability assessment of a tantalum capacitor.
The task set is to show the ability to predict the behavior of the electrical characteristics of the capacitance (C- CV / g ) and leakage current (DCL ) of the capacitor at the sinter pellet stage.
It is assumed that the capacitance of the capacitor depends on the porosity, and the leakage current behavior (DCL) depends on the neck properties of the frame material.
How the problem is solved:
The existing sinter pellet control method, by shrinkage, does not provide information about the neck and does not unambiguously reflect the change in porosity.
The proposed method, based on the mechanical characteristics of the sinter pellet, allows you to control changes in the porosity, size and defects of the neck depending on the powder and the manufacturing process.
Tantalum capacitors are widely used in the manufacture of electronic equipment for special applications, such as military, aerospace and medical, due to their high stability and reliability.
The tantalum capacitor is characterized by four electrical parameters. Of these four parameters, the capacitance and leakage currents are directly dependent on the design of the sinter pellet. For example: capacitor capacitance depends directly on the specific surface of the sinter pellet
Sinter pellet is a PM product representing pressed and sintered tantalum powder.
The manufacture of a tantalum capacitor is a lot – a step-by-step process and determining the possible causes of DCL failures associated with the production of a sinter pellet having a porous structure is not possible using existing methods of control for shrinkage or porosity. For this, an approach based on modeling a porous structure is used to predict its effect on the finished capacitor.
Production a predetermined capacitor design is primarily associated with obtaining the necessary sinter pellet porous structure, which is achieved by optimizing, on the one hand, the powder parameters: the size of its primary particle, their distribution curve, temperature agglomeration, and sintering activity; on the other hand, with technological parameters: pressing density (dg), temperature (Ts) and sintering time (t).
A structure has already been formed in the sinter pellet which defines the main characteristics of the capacitor, such as capacitance (C) and behavior, leakage current (DCL).
An increase in sinter density pellet, due to an increase in dg, leads to a decrease in C and DCL
If the capacitance of the capacitor, clearly, will be controlled by the sinter pellet porosity, and the leakage current (DCL) is associated with the defect of the dielectric. It is logical to assume that DCLs depend on the properties of the base material, i.e. from the metal frame, of a porous material, the most defective place located of which is the neck, which is the reason for the problems that occurred during electrolysis.
The sinter pellet control, when varying dg and Ts, by the standard method, allows to determine shrinkage and its changes, through its linear dimensions, but does not provide information about porosity, neck size and defect and their changes ..
The change in porosity and defects in PM products, depending on dg and Ts, is controlled by mechanical methods, in particular, by stress-strain curve.
The goal of this work is to show the relationship between the mechanical characteristics (σym, E, n) of the sinter pellets received from the stress-strain curve: with shrinkage and capacitor parameters: CV / g and DCL behavior, depending on the pressing density (dg), sintering temperature (Ts) and type of powder. This will allow the mechanical characteristics of sinter pellets to be used to predict, behavior CV /g and DCL of capacitor.
Using the proposed method will allow at the sinter pellet stage, based on a comparison of the mechanical characteristics of the tested sinter pellet, with similar characteristics of the sinter pellet selected as a benchmark:
- control sintering process acceptability
- control of acceptability of a new batch of powder
- control acceptable of the powder of the same type as an alternative supplier
- choice of the optimal sinter pellet design, when building the matrix
Comparison of the tested sinter pellet with its control analog (benchmark ), which is determined by the person responsible for its quality, increases the reliability of forecasting.
The reliability of predicting the behavior of the CV / g and DCL capacitor by the proposed method increases significantly if the mechanical characteristics of the tested sinter pellet used for the production of the capacitor are compared with similar characteristics of the sinter pellet, the design of which made it possible to receive a reliable capacitor.
Thus, at the sinter pellet stage, one can predict the behavior of the electrical characteristics of the CV/g and DCL capacitor
Mechanical inline test predicts tantalum capacitor reliability and reduces the production cost
Tantalum capacitors are widely used because of their unique high capacitance, high breakdown voltage, and relatively small sizes. Due to high-reliability tantalum capacitors are also used in military, aerospace and medical devices.
Tantalum capacitor production comprises fine Ta powder shaping and sintering into the pellets (anodes), the electrochemical formation of the Ta-oxide dielectric layer. Some inline measurements allow managing output parameters of the capacitor, but the reliability test is capable only at the end of the process. Based on the long-time investigations we found out that the reliability of the tantalum capacitor depends on the mechanical properties of the sintered pellet. Therefore the results of our special mechanical test of the sintered pellet can definitely predict the reliability behavior of the packaged capacitor. The prediction of the reliability properties of the tantalum capacitors at the early steps of the technological process saves the production cost. Below is the chart showing a correlation between the mechanical properties of the tantalum sintered pellet and the reliability behavior of the tantalum capacitor:
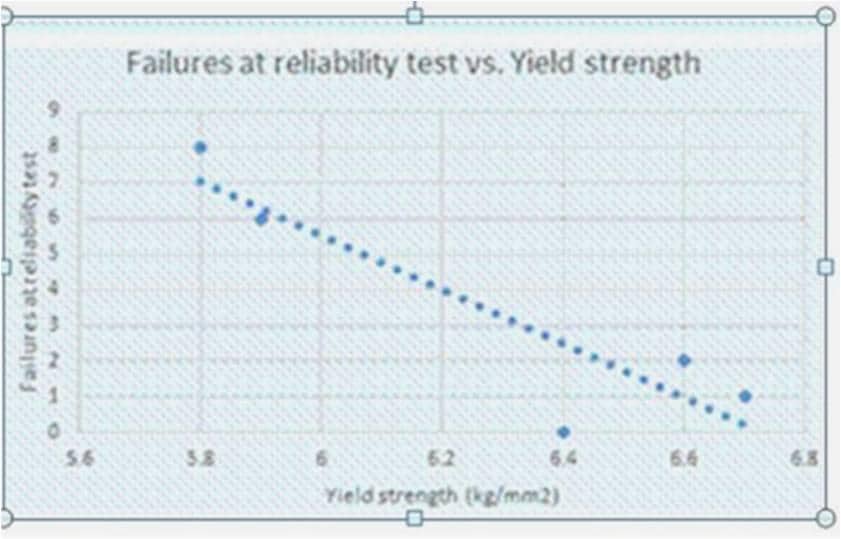
Mechanical stress of anodized pellet predicts the Ta-capacitor reliability
We have already discussed (see above) how the yield strength of a sintered Ta pellet (Ϭs) made from powders of the one grade, but from different vendors, allows predicting the reliability of a Ta-capacitor made from one recipe.
The value Ϭs may be sufficient when choosing an acceptable powder for the existing anodization recipe, but not representative enough for reliability indicators of Ta-capacitors, when it is necessary to choose an anodization recipe acceptable for specific sintered pellet. Anodization cause the formation of an amorphous film Ta2O5, which lead to created of defects in the anode (sintered pellet after anodization) and can affect the yield strength anode (Ϭa).
We offer an additional test to predict the reliability of tantalum capacitors by the ratio of the difference in the yield strength anode before (Ϭa) and after aging at 450°C (Ϭagn) to the Ϭa. In the case of an increase in this indicator, an increase in the number of failures is expected during the reliability test. Therefore, if the ratio trends to zero, it is assumed that reliability failures will be low. The graph below shows a very clear correlation between this ratio expressed as a percentage and the number of failures: