The majority of connector housings are manufactured from thermoplastic polymers due to their combination of electrical and mechanical properties and the manufacturing efficiencies of injection molding. This section will provide an overview of polymer materials and properties and a brief introduction to injection molding.
The word “polymer” describes the structure of polymers in that its meaning is “many mers” and the structure of a polymer is the repetition of a characteristic unit, the mer, many times, thousands of times. The properties of the polymer depend on the type of mer and the number of repetitions. The mers commonly used in engineering polymers are generally compounds among carbon and hydrogen, nitrogen, sulfur, chlorine and fluor.
The simplest carbon based compound is methane, CH4, a gas. The structure of methane is tetrahedral as shown in Figure 1.32 In contrast to metals where the outer electrons are free, as noted in Chapter I/1.4.2.1 Copper Alloy Metallurgy, the four outer electrons of carbon form shared directional bonds with four hydrogen atoms, each of which have one electron, to form methane gas. The electrons are shared between the carbon and hydrogen and are called covalent bonds. Covalent bonds are quite stable and methane is a stable molecule.
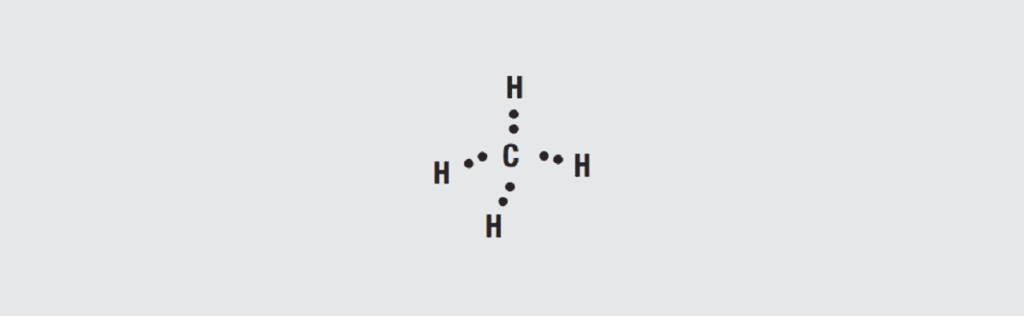
There are two variants of a carbon-hydrogen compound containing two carbons, ethane and ethylene. Ethane bonds use two electrons, the same as methane, as shown in Figure 1.33a. Ethylene used two electrons between carbon and hydrogen, but four electrons between the carbons, a so called double bond, as shown in Figure 1.33b. Ethylene is the simplest mer that can be polymerized and is the source of a family of polymers, polyethylenes. The polymerization reaction uses heat, pressure and catalysis to break the double bonds so that each carbon atom has a “dangling bond”, Figure 1.33c, which can, in turn combine with a “dangling bond” of an adjacent ethylene mer producing a chain of two ethylene molecules, Figure 1.33d. This process is called addition polymerization, mers are simply added on at each end of a polymer chain. A second polymerization process, condensation polymerization, will be discussed in a following section.
As noted the properties of the polymer vary with the number of mers. The number of mers is generally characterized in terms of the molecular weight of the polymer. For example, the molecular weight of the ethylene mer is:
As will be discussed later, polyethylene goes from a gas to a liquid to a grease to a wax, to a microcrystalline wax to a plastic as the molecular weight, the number of mers in the polyethylene chain increases. High Density High Molecular Weight (HDHMW) polyethylene has a molecular weight in the millions of ethylene mers. The structure and properties of a polymer chain depend on factors in addition to molecular weight.
Polymer Microstructure and Types
Consider now some other aspects of polymer bonding and how it affects the structure and properties of polymer chains. Two of the major aspects are bond angles and side groups. Figure 1.34 shows a schematic polyethylene chain. The carbon atoms are shown as black circles and are the backbone of the polymer chain. The hydrogen atoms, in grey, are the side group in polyethylene. There is a characteristic covalent bond angle, 110 degrees, between the carbon atoms in the backbone of a polyethylene chain. That angle depends on the bond energy between carbon and the side group and the size of the side group. For example other side groups in an ethylene type structure are methane, chlorine and fluorine which result in the polymers polypropylene, polyvinylchloride (PVC) and polytetrafluoroethylene (PTFE) respectively. Figure 1.35 shows the mers of these variants. Naturally the bond strengths, therefore the bond lengths, and bond angles of these polymers would be different from one another. Thus the interactions of the chains in the bulk polymer would be different resulting in the different properties.
As the length of the polymer chains increases, the directionality of the bonds tends to cause the chain to twist. The degree and form of twisting depends on the side groups on the chain and how they attach to the chain, randomly or at preferred sites, whichwould, in turn affect how the chains pack together. The reactivity of the side groups can also cause branching, an offshoot chain, or cross linking between chains resulting in three chain configurations, linear, branched and crosslinked as schematically illustrated in Figure 1.36.
These differences in chain interactions result in two fundamentally different microstructures, amorphous and crystalline polymers and two fundamentally different thermal characteristics, thermosetting and thermoplastic polymers. The former significantly affects the mechanical properties of a polymer and the latter the processing characteristics. Most of the engineering polymers used in connectors are crystalline or semi-crystalline thermoplastic materials: crystalline for the properties and thermoplastic for processing efficiency.
Polymer Structure and Mechanical Properties
The following discussion will be rather qualitative than quantitative to highlight the mechanisms of polymer deformation and how they vary with the polymer molecular weight and crystallinity. As noted previously, as the molecular weight of a polymer increases the length of the individual polymer chains increases which leads to two significant mechanisms of polymer strength, one physical and one chemical. First, as the length of the chains increases they are more likely to become entangled with one another. A common analogy being based on spaghetti; cut spaghetti reacts as individual strands while full length spaghetti reacts as a mass. Second, the increased chain length causes an increase in electrostatic bonding between the chains. Suffice it to say that there are several variations of dipolar bonding that can be active between polymer chains. Though the individual bond energies are small, the number of bonds between chains can be very large. In addition the electrostatic bonding tends to align the chains enhancing the opportunity for further bonding. This tendancy for alignment is the source of crystallinity in polymers. Figure 1.37a illustrates the random entanglements of an amorphous polymer, Figure 1.37b an intermediate stage of crystallinity and Figure 1.37c a highly crystalline polymer. The crystallinity of a polymer can be controlled by composition and processing. Note in Figure 1.37b that there are chains that are included in more than one crystallite cluster. These so called “tie molecules” in combination with the crystallites are an additional “entanglement” mechanism that is more stable than the physical entanglement previously described.
At low molecular weights, very short chains, the chains are free to slide over each other under an applied load. In the liquid and grease stages the chains flow freely and disentangle from each other. Eventually the increase in chain length promotes interchain bonding so that not all entanglements are disrupted, and the polymer becomes a wax. Increasing dipole bonding promotes increasing crystallinity leading to microcrystalline waxes and, eventually to rigid polymers, plastics. It should be noted that the dipole bond strength and frequency on the chain depend on the side groups in the chain so the tendency towards crystallinity is dependent on the side groups, the mers of the polymer. Crystalline polymers used in connectors include, polyamides (nylon), polyesters, and polyphenylenesulfide. Comments on these polymers will be provided later.
There is another class of polymers important to connector technology, Liquid Crystal Polymers (LCP). As the name indicates, LCP are crystalline in the liquid state consisting of rod like structures that readily self align into crystallites. At the temperatures where the LCP is liquid, thermal agitation limits the degree of crystallinity that is realized, but as the temperature decreases during the molding process a high degree of crystallinity is achieved.
The mechanical properties of many engineering polymers are further improved by the addition of glass fibers. The strengthening effect of glass fibers arises from chain bonding to the fibers. For example addition of glass fibers to the polyester PBT (polybutylene terephthalate) can double the tensile strength and increase the flexural modulus (analog to Elastic modulus in bending) by 250 percent.
A comparison of the mechanical properties of metals and polymers may be useful at this point. Metal strength data is generally provided via tensile stress. Polymer strength data may be obtained from either tensile or bending stress tests. The table in Figure 1.38 contains tensile data for copper30zinc brass in a temper commonly used in connectors and bending data for a commonly used PBT polyester polymer. The polymer data includes neat (unfilled) and 15 and 30 percent glass reinforced grades. Elastic modulus corresponds to flexural modulus and yield strength corresponds to flexural strength in the table.
There are several significant differences between the mechanical properties of metal and polymers in Figure 1.38: First, metals are much stiffer and stronger than polymers. For reference, the elastic moduli of copper alloys used in connectors fall in the range of 110 to 140 GPa (16 to 20 Mpsi) while for typical connector engineering polymers the corresponding range is 1 to 19 GPa ( 0.3 to 2.8 Mpsi); the corresponding comparison for tensile (flexural) strength are 230 to 760 MPa ( 35 to 110 Kpsi) for metals and 40 to 185 MPa (6 to 27 Kpsi) for polymers. Second, the effect of reinforcing glass fibers on polymer mechanical strength is significant. In the example polymer the flexural modulus and flexural strength are doubled with 15 percent glass, and nearly tripled with 30 percent glass. Similar improvements occur with other polymers. Third, it merits noting that the higher values of flexural modulus and strength are for Liquid Crystal Polymers and that LCP do not benefit from reinforcing fibers. A final, and significant difference between metals and polymers is their temperature and strain rate sensitivity. The mechanical properties of metals are essentially constant with respect to temperature and strain rate. Polymers, in contrast are sensitive to both. The mechanical properties of polymers are reduced as a function of increasing temperature and decreasing strain rate. A simplistic, but basically correct, explanation of these sensitivities revolves around the movement of polymer chains as a function of temperature and load. Increasing temperature increases the amount of thermal motion of the chains and facilitates their untangling and sliding over each other, thus reducing the strength of the material. Slow strain rates have a similar effect, the chains have more time to untangle and slide as the load slowly increases, viscoelasticity. Glass reinforced polymers are less sensitive to these temperature and strain rate effects due to the polymer bonding to the glass fibers restricting the chain motion. Metals are not immune to thermal effects as noted earlier with respect to stress relaxation and its effect on contact force. Polymers, however, show much larger effects, material flow, creep, rather than stress relaxation which is a localized atomic level rearrangement.
Polymer Processing
There are two processes used to convert polymer resin pellets to a connector housing, compression/transfer molding and injection molding. Before discussing those processes, however, another method of polymerizing the starting resin must be mentioned for completeness, condensation polymerization.
Recall that addition polymerization occurs by the addition of individual mers to existing polymer chains under the influence of temperature, pressure and catalysis. Some typi cal addition polymers include polyethylene, polypropylene, polyvinyl chloride (PVC) and polytetrafluoroethylene (PTFE).
Condensation polymers are so called because the bond breaking process that leads to polymerization occurs through a chemical reaction between different mers, an organic acid and an alcohol, esterification, with the production of by-products, condensates. The most common condensates are water and methyl alcohol, CH4O. Polymers produced by the esterification reaction are called polyesters. Nylons, polyamides, are also produced by condensation polymerization.
Compression/Transfer Molding
Compression and transfer molding processes are used primarily for molding of cross linking, thermosetting, polymers. The processes are similar, differing in how the polymer resin is presented to the mold. In compression molding a fixed amount of material is placed into the mold which is then pressurized and heated to the molding temperature. In transfer molding the material is transferred from a transfer pot into the mold at controlled temperature and pressure. Molding temperatures are high and time in the mold is long in order to optimize the cross linking of the polymers with a significant cost impact. Any molding scrap, from sprues and runners in the mold to underfilled parts is scrap.
Injection Molding
Injection molding is similar to transfer molding in that the resin pellets are held in a hopper and transferred, after heating/mixing/plasticating, by injection under pressure into a mold. While some thermosets are injection molded, the vast majority of connector housings are thermoplastic polymers.
There are two major components of an injection molding system, the injection system and the clamping system, shown in Figure 1.39. The injection system includes:
Hopper: The hopper holds the polymer resin pellets prior to transfer into the plasticating section. The hopper can be refilled as needed because the pellets are not held under controlled temperature.
Plastication: Plastication includes two steps, heating of the resin and mixing of the heated pellets into a homogenous polymer melt at a controlled temperature. Heat is supplied by heater bands around the injection barrel. A reciprocating screw within the injection barrel mixes the heated polymer until it is ready for injection into the mold. The reciprocating screw then moves forward injecting the polymer under controlled pressure through a nozzle into the gating system of the mold. The pressure is maintained during the cooling cycle of the process. The nozzle then retracts and the hopper fills the plastication section with polymer for the next molding shot.
The molding system includes
Clamping System: The clamping system contains and supports the mold. It consists of a fixed front plate which engages the nozzle during injection of the polymer and a movable back platen which holds the mold closed under a clamping pressure dependent on the size of the mold and polymer being molded and moves backward on completion of the cooling time to open the mold and eject the molded parts.
Mold: The mold may be a single or multi-cavity mold depending on the economics of the part being molded. A multi-cavity mold will contain sprues and runners to interconnect the individual cavities. Mold design of multi-cavity molds can be complex in order to balance the polymer flow to the individual cavities. For thermoplastic polymers, the sprue and runner parts may be salvaged and reused depending on the requirements on the part. An example of a multi-cavity mold is provided in Figure 1.41.
As noted with the processing of metals from casting to strip, the principles of injection molding are straight forward, but many design challenges must be met to ensure consistent high volume manufactured parts.
Polymer Families
The number of individual engineering polymer products has exploded in the past years due to specialized requirements on the polymer being addressed by a variety of additives. Additives and the function they provide include:
Flame Retardants: Most connector housings are required to meet flammability requirements, burning rates and combustion products, defined by various product safety organizations. Some polymers are intrinsically flame retardant, but the majority require additives to provide that function (most of them are halogen).
Reinforcing Agents: Reinforcing agents are intended to enhance the mechanical properties of polymers. As noted previously, glass fibers are the most common reinforcing agents. The enhancement is dependent on the percentage of fiber, the length of the fiber, the bonding between the polymer and the fiber and the processing.
Stabilizing Agents: Stabilizing agents are intended to reduce the sensitivity of a polymer to moisture, oxidation, Ultra-violet radiation etc.
Colorants/Plasticizers: Colorants, of course, are used to add color to the polymer. Plasticizers are additives intended to improve polymer processibility.
Given the variety of products available in these families the discussion will be qualitative. Refer to the supplier literature for details on specific products in each family.
Polyamides: Polyamides are generally known as “nylon”. There are several varieties of nylon use in connectors depending on the component mers used for polymerization. The generic designations are 66 and 46 with 66 being the oldest and most commonly used. Nylons are semicrystalline polymers and have a number of desirable characteristics and one unfortunate negative.
66 nylon once dominated the connector market as a housing material due to its combination of strength, toughness, abrasion resistance and chemical stability. The negative characteristic of nylons is high moisture absorption, with 66 nylon being the most susceptible. High moisture absorption results in growth in dimensions of the part, and subsequent shrinkage if the part later dries out. This compromises the dimensional stability and limits the size of housings that can be made with 66 nylon.
Moisture absorption also compromises the mechanical and electrical properties of nylons. For 66 nylon the flexural modulus and flexural strength both decrease by more than 50 percent from the Dry as Molded to samples conditioned at 100 percent Relative Humidity. The volume resistance also degrades from 1015 to 109 W/cm, a significant decline, but still a very high resistance. Other nylons are less susceptible to this problem. Nylons are still widely used in automotive, commercial, white goods and industrial markets.
Polyesters: Polyesters, too, are semicrystalline polymers with a good balance of electrical and chemical properties and good mechanical properties with glass reinforcement. There are three polyesters used in connectors, PET (PolyEthylene Terephthalate), PBT (PolyButylene Terephthalate) and PCT (PolyCyclohexylenedimethylene Terephthalate). The different mers used for each polyester affect the polymer chain stiffness which affect the mechanical properties directly, but also affect the crystallization of the polymers which influences processing parameters.
Apart from Surface Mount Technology (SMT) soldering applications where the temperature capability of PBT is not adequate, it is the most widely used of the polyesters.
PBT has excellent chemical resistance, very good electrical properties and moderate mechanical properties. It is also sensitive to moisture during processing.
PET is similar in properties to PBT but has better mechanical properties and temperature capabilities and could be used in some SMT applications (before lead free issue). It is also sensitive to moisture during processing.
PCT has better short term temperature capabilities than PBT and PET and was suitable for SMT applications before lead free but not so much used any more.
PolyPhenyleneSulfide (PPS): PPS is a crystalline polymer and has high temperature capabilities for SMT and continuous use applications. The crystallinity of PPS, and, therefore, the properties, are process sensitive. Most PPS polymers are glass reinforced for both mechanical properties and to reduce brittleness and flash for enhanced molding performance. PPS is inherently flame retardant and has outstanding chemical resistance. The properties of PPS are stable over a large temperature range.
Liquid Crystal Polymers (LCP): LCP, as noted previously, is crystalline even in the molten state due to its rod like structure. This impacts several processing and performance characteristics of LCP. The high crystallinity of LCP results in a good balance of flexural modulus and strength over a range of temperatures. The high temperature stability of LCP makes it suitable for SMT and high continuous use applications. However the intrinsic crystallinity of LCP during mold flow can produce highly anisotropic properties due to the rod alignment in the flow direction. The anisotropy in crystallinity creates a tendency towards part warpage and results in weak “weld lines”, the interface where two fronts of injected polymer meet in the mold. This tendency is countered by the use of glass reinforcement and other fillers to reduce the anisotropy. LCP is inherently flame retardant and has outstanding chemical resistance. LCP has outstanding mold flow allowing the molding of thin sections and excellent dimensional stability an important characteristic for molding of miniaturized connector housings.