The article explains safe built-in fuse function technology of segmented metallized PP dielectric films utilized in Panasonic Industry’s box type film capacitors.
When speaking about a device’s overall reliability, we know that is first and foremost a question of the components it is consisting of. Next to the ability of withstanding rough operational conditions such as vibrations and shocks, it is high voltage stress that can pose a severe risk of damage to components such as capacitors in high power designs – as found in automotive applications, industrial power supplies, DC/DC, AC/DC converters, solar inverters and many more.
In those contexts, high voltage stress cannot be abolished – but there are to avoid overall and fatal product failure: The fuse function is an integral part of the Panasonic Industry Film Capacitor technology which is worth a closer look for everyone designing next-gen high voltage applications.
Film Caps – a brief clarification on the basic principle
Film capacitors, commonly also known as plastic film capacitors, or polymer film capacitors, are electrical capacitors utilizing an insulating plastic film as the dielectric. The dielectric film materials vary depending on required dielectric strength, primarily Polypropylene (PP), Polyester (PET), Polyphenylene sulfide (PPS) etc. The electrodes could be metallized aluminum, zinc or Al-Zn alloy applied directly to the surface of the plastic.
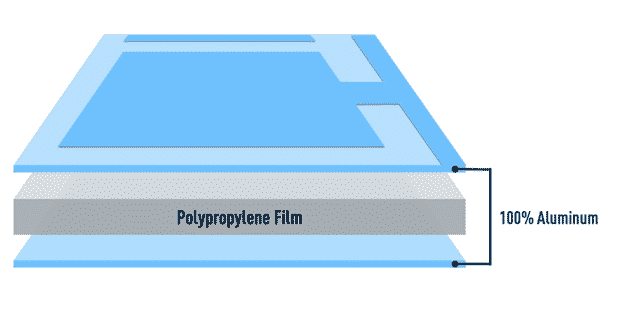
Film Caps – and the benefits of self-healing
To a certain but remarkable extent, metallized film capacitors have the ability to “repair” themselves. This so called “self-healing” ability applies when a capacitor with metallized films has the foils exposed to each other due to dielectric breakdown under voltage stress. The combination of the foils’ thinness and the high energy density at the damaged area causes the foils to vaporize – and the capacitor stays in operation. However, when too many of such damaged areas fail in a very short period of time, metallized film capacitors short circuit upon failure. In pursuit of higher safety and higher reliability for most of the industries’ innovations, the market correspondingly shows an increased demand for film capacitors to also open upon failure.
Better safe – built-in fuse function with patterned metallization
Specific patterned metallization technology – better known as “fuse function” emerges from a segmented thin layer of vapor deposited aluminum.
Those segments isolate the failure caused by overvoltage, therefore the damage is only encapsulated in a few areas of the capacitor. In case too many of those areas fail in a very short period of time, the capacitor will then open in a safe manner.
A comparison
The difference is apparent: When “treating” dielectric material with high- or overvoltage, the un-patterned version reveals a far more severe damage than the patterned fuse function film cap concept.
This patterned built-in fuse function should be a core criterion for everyone involved in high voltage application design and looking for the ideal type of capacitor. Or – shortly said: Better patterned than sorry!
To have a closer look, you can watch Panasonic Industry’s comparison in motion: