In this article, Vladimir Azbel Ph.D., semiconductor process reliability engineer consultant, Israel propose two-stage tantalum powder sintering techniques in order to improve tantalum capacitor quality and reliability.
Abstract
Sintering porous tantalum pellets is a critical step in producing tantalum capacitors (TC), integral to electronics for their high capacitance, reliability, and stability. However, achieving high-quality sintered pellets, especially with thicknesses below 1 mm, often leads to warping during sintering, impacting subsequent production stages and electrical properties of capacitors.
This study investigates the efficacy of two-stage sintering in controlling pellet properties. Experimental results demonstrate that two-stage sintering effectively reduces warpage while maintaining electrical characteristics, enhancing the reliability of tantalum capacitors. A model is proposed to estimate optimal sintering parameters, offering insights into controlling pellet structure. The study underscores the potential of two-stage sintering for optimizing tantalum capacitor production.
Introduction
Sintering porous tantalum pellets is the initial and critical stage in the production of tantalum capacitors (TC). These capacitors find wide application in electronics due to their high capacitance, reliability, and stability. The quality of sintered pellets plays a significant role in determining the reliability of tantalum capacitors, much like how the foundation of a house affects its overall stability.
However, producing high-quality sintered pellets with minimal defects, especially those with a thickness of less than 1 mm, often leads to shape distortion during sintering, a phenomenon known as warping. Warping indicates the presence of internal stresses, which negatively impact the quality of subsequent production stages.
Warpage of sintered tantalum pellets can significantly affect the electrical properties of multi-anode tantalum capacitors, potentially leading to changes in capacitance, ESR, and leakage current. The causes of warpage depend on various factors, including technological parameters such as powder composition, compaction density, and sintering temperature, as well as equipment capabilities for compaction and sintering.
The manufacturer of the TC determines the above-listed technological parameters of the sintered pellet and equipment settings.
Factors Affecting Warpage and Pellet Quality
One of the reasons for the warpage of sintered pellets, apart from their heating and cooling rate, is the uneven compression of the powder material caused by the non-uniform distribution of primary powder particles in size and asymmetry of pressure distribution inside the pressed pellet depending on the compaction scheme. These factors are an integral part of the production of pressed pellets.
One way to reduce the risk of warpage is to find the optimum balance between compaction density and sintering parameters – temperature, heating and cooling time, and rate. In the search for optimal parameter values, it is necessary to consider that reducing the risk of pellet warpage is usually achieved by decreasing the compaction density and sintering temperature, while ensuring the reliability of the electrical characteristics of TC requires, on the contrary, their increase.
Although the sintered pellet plays a key role, the possibilities of controlling its structure to achieve optimal values between conflicting parameters, in the production of tantalum capacitors (TC), have not been fully utilized.
Two-Stage Sintering Process
This may be due to limited knowledge of sintering technologies for materials with controlled porosity (e.g., filters) used in powder metallurgy, which could be useful in producing TC.
Usually, for sintering pellets, tantalum capacitor production uses a single-stage profile Applying a two-stage temperature profile (see Fig. 1 ) expands our capabilities in controlling the making of the material’s porous structure, likely due to the ability to use two key sintering mechanisms – surface and volume diffusion – in a single heat treatment cycle.
These processes can controlled at different time intervals depending on the temperature and material. By independently regulating the temperature and time at each stage, we can shape the material’s structure by controlling its sintering process. Shrinkage of the material can be used as an indicator of the sintering mechanism: in surface diffusion mechanisms, material shrinkage is absent, unlike in volume diffusion mechanisms. (See Fig. 2)
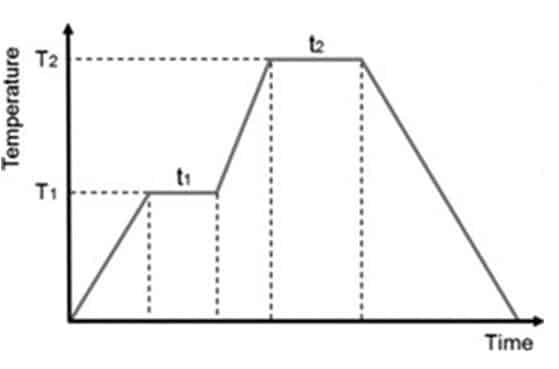
Both mechanisms are significant, for achieving optimal properties of tantalum capacitor pellets, such as porosity, mechanical strength, and electrical characteristics. The ability to independently control these mechanisms allows for managing the sintering process.
Based on the above, the possibility of utilizing the advantages of two-stage sintering for tantalum pellets used in tantalum capacitor manufacturing is considered. Two-stage sintering is a process in which the material undergoes two consecutive heating and cooling with the ability to independently control the temperature and time at each stage within a single technological cycle (see diagram).
To regulate porosity during the sintering process, it is necessary to select the temperature of the first stage in such a way as to avoid intensive sintering and reduction of porosity. The shrinkage of the pellet is used as an indicator of the sintering process. In this case, a low temperature at the first stage will help preserve a significant portion of the porous structure of the pressed pellet. This approach allows for more flexible control of the porous structure in the second stage of sintering, which is not available with single-stage sintering.
At the optimal temperature during the first stage of the sintering process, the development of relaxation of compressive stresses occurs, which may transform them into tensile stresses. This process may increase in the pellet volume and enhance diffusion speed along the particle boundaries. The creation of necks between primary powder particles, accompanied by the change of the boundaries, between them due to adhesive contact, reduces defects and increases thermal conductivity.
Properly selected temperature and time during the first stage of sintering ensure the formation of contact area between particles without changing the pore sizes, simultaneously reducing internal stresses without altering the pellet volume.
In the second stage of sintering, the dominant mechanism is volume diffusion, unlike the first stage, leading to changes in the pellet volume. Process management of the temperature and time of sintering during the second stage shapes the dynamics of necking and porosity within the pellet, significantly affecting its electrical characteristics such as capacitance and leakage currents. As a result, the final structure of the pellet is formed.
Thus, two-stage sintering can be more effective than single-stage sintering in the technological process of tantalum capacitor production.
Experimental Results
To evaluate the effectiveness of two-stage sintering technology, a sintered pellet with a thickness of 0.9 mm was selected to produce multi-anode tantalum capacitors. In these capacitors, warpage absence is a critical parameter. To reduce the risk of warpage, a decision was made to decrease the pellet’s compaction density and sintering temperature to 5.0 g/cc and 1310°C, respectively. However, this leads to an increase in leakage current losses, which may negatively impact the reliability of the tantalum capacitor.
To address this contradiction, an experiment was conducted using two-stage sintering with increased pellet compaction density and sintering temperature. (see figure) This should reduce the likelihood of warpage and decrease leakage current losses, positively affecting the tantalum capacitor’s reliability.
The experimental options are presented below in the table 1:
Variant | Press Density [g/cc] | First Sintering Step [T°C/min] | Second Sintering Step [T°C/min.] |
---|---|---|---|
Standard | 5 | 1310/30 | – |
Experimental A | 5 | 1000/40 | – |
Experimental 1 | 5 | 1000/40 | 1310/30 |
Experimental 2 | 5,5 | 1000/40 | 1310/30 |
Experimental 3 | 5,25 | 1000/40 | 1350/30 |
Several pellet variants, Experimental 1, 2, 3, from the table, underwent two-stage sintering. After conducting experiments with two-stage sintering, all variants, except Experimental A, were divided into two groups.
The first group of pellets, selected from each variant, underwent compression tests to record the stress-strain curve (SS) (see Appendix). The SS curve parameters determined the yield strength and shear modulus and calculated the strain hardening coefficient for each variant. These parameters reflect the characteristics of the porous material structure.
The developed models establish a numerical relationship between these parameters and various aspects of the material’s porous structure, such as the size of necks between particles, porosity, and granule defects. The SS curve parameters were used as indicators to assess the impact of two-stage sintering on changes in the pellets’ porous structure through their mechanical properties for different variants.
To monitor two-stage sintering through shrinkage, it was necessary to determine the pellet dimensions after the first stage of sintering. For this purpose, the pressed pellet underwent single-stage sintering at a temperature and time corresponding to the first stage of the two-stage process. According to the above, the sintering process in the first stage should not cause a reduction in pellet size compared to the pressed state. To estimate the temperature of the first stage, a model was proposed, which will be discussed below.
The second group of pellets from all variants underwent the standard technological process of tantalum capacitor production. After sintering, all variants of pellets were combined on one tray. Since these pellets were used for multi-anode capacitors, data for analyzing their electrical characteristics, was used
after the Silver Test. This allows for comparing the effects of sintering experiments on their electrical properties (see Table 2). These data include capacitance and leakage currents.
Since capacitance correlates with porosity and leakage currents depend on internal stresses caused by defects, one of which is sintering, data characterizing leakage current losses were used instead of leakage current parameters for the convenience of analyzing the influence of internal stresses created during sintering.
The sintering process’s influence on the sintered pellet’s properties can be evaluated by comparing the pellets’ electrical and mechanical parameters from the first, second, and third groups with the standard variant. The effect of the difference between two-stage sintering and single-stage sintering on the
structure of the sintered pellet can be illustrated, below in the sintering diagrams (Fig. 3,4).
Modeling and Optimization
To determine the maximum allowable temperature for the first stage of the tantalum powder pellet sintering process with various values of CV/g to avoid shrinkage, we propose using the relative change in pore volume as an indicator of shrinkage.
For a clear description of the sintering process, we can apply, the below model (see Fig. 5), where D represents the diameter of the primary powder particles, L is the distance between the centers of contacting particles, R is the diameter of the pore formed by these particles, and r is the diameter of the pore after particle sintering, where the distance between their centers is halved, from L to L-x. In this case, r=R-x.
Then the relative change in pore volume can be expressed as follows:
ΔV = (R3−(R−х)3)/ R3
To calculate ΔV, knowing the values of R and x is necessary. The value of x can be calculated
using the following equation:
x=√D*t,m
x is displacement particles, diameter Z, for a time t at temperature T
D=D0*EXP(-Q/kT)
- D0 is temperature-independent preexponential (m2/s)
- D is the diffusion coefficient
- T is the absolute temperature (in Kelvin)
- k is Boltzmann’s constant
- Q – the activation energy for diffusion
The convergence of the centers of sintered tantalum particles occurs through the mechanism, of self-diffusion and is dependent on the sintering temperature. To determine ΔV =0 for any grade of tantalum powder, it’s crucial to know the diameter of the pore (R) formed in the powder before pressing.
To estimate the pore diameter, in different grades of powder, data obtained from various vendors of tantalum powders using the mercury pycnometer method were used. This method provides information, not just about the pore size distribution, but also about the cumulative pore area or the specific surface area of the powder (Fig. 7,8). Figure 9 shows that each pore diameter (D50) in their distribution corresponds to its maximum cumulative pore
area of the powder.
The specific surface area values obtained by gas adsorption (BET method) slightly exceed those measured using mercury (cumulative pore area), since porosimetry cannot account for fine surface roughness and applies more simplified model calculations for their analysis. In the investigated tantalum powders, the influence of roughness can be considered insignificant within the measurement accuracy, allowing the BET values to be equated to the
cumulative pore area.
Through the relationship between the BET method and CV/g (Fig. 10), we can correlate the average pore size values (D50) obtained through the cumulative pore area method with the corresponding CV/g values (Fig. 11).
The porosity and cumulative pore area of the powder depend on its type and weakly on the pellet pressing density (Fig. 6), allowing the use of porosimetry data for pressed pellets with a pressing density below 5.5g/cc.
To assess the adequacy of the proposed model for calculating shrinkage due to the sintering temperature of tantalum powders, a calculated shrinkage dependence was plotted for the sintering temperature range from 1000°C to 1450°C, for powders with 80 kCV/g (see Fig. 12).
Red circles indicate experimental results on this graph. As seen from the graph, the calculated values closely match the experimental ones, allowing, by calculation, an estimation of the temperature of the initial sintering stage that does not lead to material shrinkage.
Conclusion
- Effectiveness of Two-Stage Sintering: The research demonstrates the effectiveness of two-stage sintering in controlling pellet properties, particularly in reducing warpage while maintaining optimal electrical characteristics. By utilizing two consecutive heating and cooling stages with independent temperature and time control, two stage sintering offers a promising approach to enhance the reliability of tantalum capacitors.
- Optimization Potential: The study highlights the potential for optimizing sintering parameters to achieve desired pellet structures and properties. By developing a model to estimate optimal sintering parameters based on pore volume change and sintering temperature, manufacturers can make informed decisions to prevent shrinkage and preserve pellet integrity.
- Mechanical and Electrical Evaluation: Experimental results indicate changes in mechanical properties, such as yield strength and shear modulus, as well as electrical characteristics, including capacitance and leakage currents, in response to different sintering conditions. This comprehensive evaluation provides valuable insights into the relationship between sintering parameters and pellet performance.
- Practical Implications: The findings of this study have practical implications for tantalum capacitor production, offering manufacturers strategies to improve pellet quality, reliability, and performance. By adopting two-stage sintering techniques and optimizing sintering parameters, manufacturers can enhance the overall quality and reliability of tantalum capacitors, contributing to advancements in electronic device manufacturing.
Appendix
Describe characteristic Strain-Stress curve, porous material
Yield strength (Ay) depends on the neck’s size, which affects the maximum permissible formation voltage. For porous materials, the yield stress can be calculated using the following equation:
Ay = b*A0*(X/D)2
where b is an empirical constant, Ay is the yield point of the sintered porous material, and A0 is the yield point of the deformed material. The neck size (X) is divided by the size of the primary powder particle (D), but this ratio cannot exceed 0.5.
Young’s modulus (E) is related to porosity, which affects capacitance. The behavior of Young’s modulus of a porous material can be described using the following equation: E = E0*(1-p/pc), where E is the elastic modulus of a porous material with a porosity of the corresponding density p, and E0 is the modulus of solid material at a density pc ~ 1.
The CC curve can be used to calculate the strain hardening coefficient (n), which is related to the defectiveness of the material. This coefficient can influence leakage currents.