This article written by Bourns explains why sulphur-resistant film resistors are needed to improve reliability of industrial and other harsh environment applications.
In recent years, the long term reliability of film chip resistors in a high sulphur environment plays an increasingly important role in a wide range of market segments such as industrial electronics, IT systems and telecommunications. Sulphurous environments have a negative impact on film resistors by reacting with elements, in particular silver.
Sulphur pollution can adversely affect productivity in industrial environments, and is known to be influenced by several critical factors that include areas where oils, lubricants or fossil fuels are utilized. Sulfur is also an issue when affected materials are in the presence of rubber seals, gaskets, grommets or molded coatings, which are frequently part of the factory setting.
Sulfide growth can cause resistors to go open circuit.
The critical environmental factors of sulphur pollution are:
- Where oils, lubricants or fossil fuels are used
- Rubber seals, gaskets, grommets or molded coatings of affected material
- Air polluted industrial area or areas containing biological or volcanic gasses
The key application areas most affected by sulfur pollution are: - IT industry, server farms, data/storage centers, notebooks and desktop computers
- Communication base stations
- Industrial motor controls, pump controls and welding equipment
- Rubber, paper and oil manufacturing
- Outdoor and on-road applications, lighting and traffic control
- Marine, mining, agricultural and winery equipment
BACKGROUND
The Film Surface Mount Chip Resistor is practically a standard in the electronics industry and is in wide use today due to economics and manufacturability. The basic structure (Featured image) is composed of a ceramic substrate with layered terminations on each end of the ceramic chip. The layers consist of internal terminations that are typically comprised of a printed silver (Ag) or siver palladium (AgPd) material.
The resistive element or ink is then screened onto the ceramic chip and connects both sides of the Ag/AgPd terminals, creating the resistive circuit. An epoxy passivation layer is then applied over the resistive element which partially covers the Ag/AgPd terminals, leaving a portion of the terminal exposed for final construction of the terminal outer layer application process. A protective nickel (Ni) covering is then sputtered onto the Ag/AgPd terminals to prevent any type of contamination. Finally, a matte tin (Sn) solder layer is applied to the terminals to complete the construction.
STANDARD FILM RESISTORS vs. SULFUR-RESISTANT FILM RESISTORS
In standard film resistors, the area where the internal Ag/AgPd terminal is only protected by the epoxy passivation layer is susceptible to the ingress of sulfur based gasses. These gasses can diffuse and attack the silver in the Ag/AgPd internal terminal, which, depending on factors such as temperature, humidity and even air flow in the environment, begin the corrosion process and the formation of silver sulfide. Over time, the silver sulfide can crack the ceramic of the resistor package, causing the resistor to open circuit. Another possible consequence is that once the non-conductive silver sulfide has formed along the length of the terminal, it gradually increases with resistance as the conductive path is reduced, eventually resulting in another open circuit condition and failure of the resistor.
Application of the sulfur-resistant resistor is no different than a standard film resistor when it is designed into and used in IT systems, industrial and telecommunication electronics. The benefits, however, for data/storage centers, server farms, and the IT industry in general are enormous in these mission critical applications, e.g., when used in banking, mass data storage, military and especially harsh industrial environments or geographic locations like China and India, where conditions sometimes may not be optimum for server operation.
ADVANTAGES OF SULFUR-RESISTANT FILM RESISTORS
Plating termination layers of sulphur-resistant thin film resistors have a special structure in the area between the protective layers and the terminations in order to cover the silver (Ag) terminals (Figure 1.) and protect it against sulphurous gases. Bourns sulphur-resistant thick film resistors consist of a specialized Palladium (Pd) protection layer that covers the Silver (Ag) terminals (Figure 1.). The (Pd) protection layer eliminates the ingress of the sulphur gasses and thus removes the chance for corrosion and formation of Silver Sulphide.
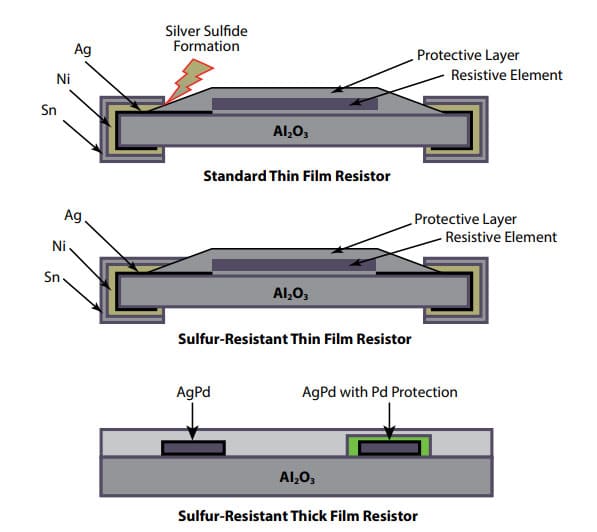
ADVANTAGES OF SULFUR-RESISTANT FILM RESISTORS IN DATA CRITICAL APPLICATIONS
As the transfer of data becomes ever more critical in the digital age, the need for uncorrupted data transmission and reception at the binary level in all manner of applications, from the modest smartphone to the supercomputer, is paramount.
Although soft errors or repairable bits of data can be recovered through redundancy systems and complex algorithms or error correction systems, the hard failure of any input or output interface port can still cause a catastrophic system failure. These hard failures can be caused by corrosion in a system such as a server farm exposed to harsh environments on a factory floor or data systems located geographically in regions of the world that have higher percentages of potentially corrosive gasses or biological and volcanic gasses, especially where sulfur bearing gasses or environments with higher sulfur contamination exists.
In addition to gaseous born states, sulfur can also be found in connectors, oils, lubricants, gaskets, rubber sealings, molded coatings, etc., which can lead to the formation of silver sulfide that corrodes the silver terminals in sensitive electronic components like a film resistor. There are now even recommendations on corrosivity levels for IT centers, so as to try to control the environment.
With the use of sulphur-resistant film resistors, this corrosion related type of hard failure can be substantially reduced or eliminated, resulting in improved system reliability, performance, robustness and reduction of downtime. This is one of the most important operating factors in the IT industry where subsystems such as memory modules are used heavily in the server farms and the data/storage center marketplace.
RESULTS AND BENEFITS
In order to test the performance of standard film resistor compared to a sulphur resistant film resistor, Bourns tested the parts in a 2400 cm3 glass desiccator vessel with 40 ~ 60 grams of powdered sulphur. The vessel was heated to an elevated temperature of 105 ˚C to accelerate the effects of the sulfurization. The resistors were then measured at regular intervals to verify resistance.
Under these test conditions, the test results of the standard film resistor versus the sulphur-resistant film resistor showed the sulphur-resistant device had about 20 times greater operating lifetime than the standard device. In the world of industrial and telecommunication electronics, this test result indicates a more reliable system that will help reduce field failures related to standard film resistor failure in sulphur contaminated environments.
SUMMARY
Due to the increase of IT, industrial and telecommunication electronic equipment in every form of industry and environment, the need for sulphur-resistant film resistors is becoming more prevalent and necessary. Reliability in all market segments is critical and failures can be extremely costly to the manufacturers, users and service providers. Thus, sulphur resistant film resistors can protect against system downtime and field failures safeguarding the return on investment for all sectors of the industry.