TU Graz and partners successfully 3D print super magnet using laser-based AM.
An additive manufacturing breakthrough coming out of TU Graz in Austria could make it easier to manufacture permanent magnets for small electronic components. A TU Graz team—working in collaboration with the University of Vienna, the Friedrich-Alexander Universität Erlangen-Nürnberg (FAU) and Joanneum Research—has successfully manufactured super magnets using a laser-based 3D printing process.
Permanent magnets are present in many electrical products—from electric motors and sensors, to wind turbines and magnetic switching systems. Despite their ubiquity, however, they present certain manufacturing challenges. That is, permanent magnets are typically produced using sintering or injection molding, which limits them in terms of size and geometry.
With electronics being increasingly miniaturized, there needs to be a way to produce super magnets in more complex geometries and at smaller scales. Additive manufacturing has thus presented an interesting avenue forward for the production of super magnets.
The Austria-based research team recently reported it had successfully 3D printed a super magnet structure, using a magnetic powder material and a laser-based AM process. The overall process has been refined to the point where the printed magnets display a high relative density with controllable microstructures.
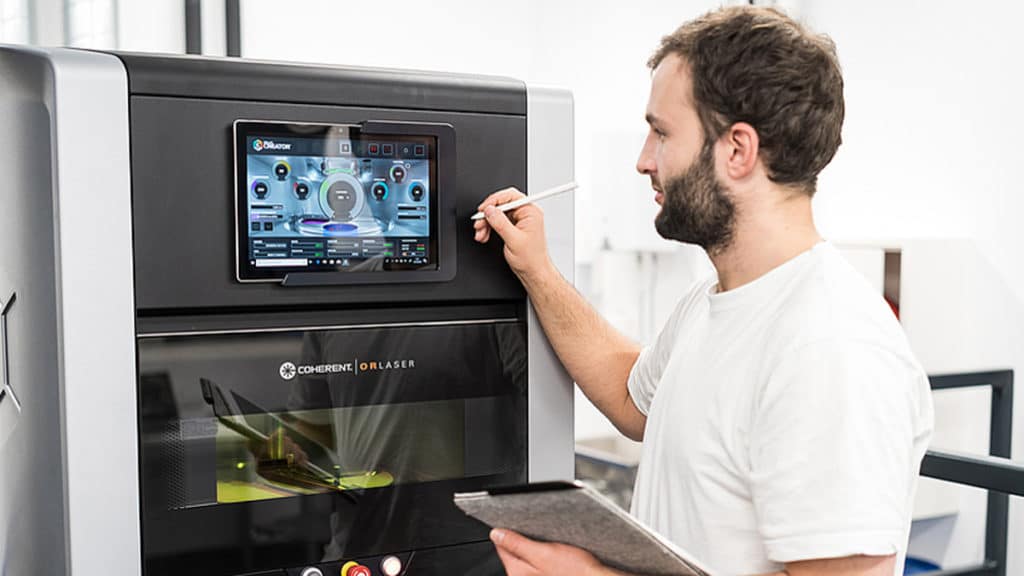
As Siegfried Arneitz and Mateusz Skalon, researchers at the Institute of Materials Science, Joining and Forming at TU Graz, explained: “The combination of both these features enables efficient material use because it means we can precisely tailor the magnetic properties according to the application.”
In the beginning, the researchers focused their efforts on 3D printing neodymium (NdFeB), a rare earth metal that is used in many strong permanent magnets, such as those used in computers, smartphones and more.
Now, team member Arneitz—a PhD student at TU Graz—is exploring the possibility of 3D printing other types of magnets, like iron and cobalt magnets (Fe-Co). Down the line, these magnets could present a more ecological alternative to NdFeB, which, as a rare earth metal, is resource intensive and challenging to recycle.
The researchers also point out that, in terms of performance, rare earth metals tend to lose their magnetic properties at high temperatures, while Fe-Co alloys can maintain their magnetism up to 400° Celsius.
“Theoretical calculations have shown that the magnetic properties of these materials can be improved by a factor of two or three,” Arneitz added. “Given the flexibility of shape that 3D printing offers, we’re confident we can get closer to this goal. We’re going to continue working on this topic in collaboration with various other institutes so we can develop alternative magnetic materials for areas in which neodymium magnets are not necessary.”
featured image source: TU Graz