This article written by Dennis Zogbi, Paumanok Inc. and published by TTI Market Eye provides PTC Thermistor overview of its complex ecosystem in 2024.
Introduction to PTC Thermistors
PTC (positive temperature coefficient) thermistors are used primarily for overcurrent protection in a variety of electronic equipment applications but are also available in specialty switch applications for degaussing circuits in cathode ray tube TV sets and PC monitors, inrush current limiting in lighting ballasts, motor start circuits for compressor motors and as heating elements for electric heaters.
This article written in December 2023 addresses the global market for PTC thermistors in both ceramic and polymer constructions and in their various types of configurations, primarily—but not limited to—radial, surface mount, axial strap as well as their vertical integration into probe assemblies.
Ceramic PTC Construction
Ceramic PTC thermistors are primarily made from doped barium titanate. Barium titanate’s basic building blocks are barium carbonate and titanium dioxide. Interaction of semi-conductance and ferro-electricity cause the resistance of the ceramic PTC thermistor to change with temperature. Below a certain Curie point (or transition temperature), the device is in a low resistance state and has a small negative-temperature coefficient. Above the Curie point, the dielectric constant of the material drops, increasing the barrier potential between individual crystals in the structure. Because free electron flow is restricted, the material resistivity rises.
Further temperature increases cause total device resistance to increase exponentially by several orders of magnitude and produces a switch-like response. Ceramic type PTC thermistors are considered reliable and robust and are the technology upon which the global PTC thermistor market was founded. However, in many instances, over the years it has been displaced by disruptive technology in the form of polymer PTC thermistors.
Polymer PTC Construction
Polymeric PTC devices are a low-cost alternative to the ceramic PTC thermistor. Polymer PTCs are made of conductive particles, such as carbon, scattered in a polymer matrix. Resistivity of the material is about an order of magnitude lower than that of ceramic PTC thermistors, which allows operating currents much higher than possible with ceramic thermistors. Under normal operating conditions, little I2R heat is generated and the conductive particles remain in close contact.
When overcurrent occurs, the polymer heats above its transition temperature. The polymer matrix expands, causing the conductive particles to lose contact, which sharply increases device resistance—a remarkable and exotic solution. As with the ceramic PTC thermistor, I2R heating is normally enough to keep the polymer PTC latched in the high resistance state. The polymer PTC thermistor, which was invented by Raychem of Menlo Park, California (now part of TE Connectivity) is considered new technology. Since the Raychem patent expired due to its reaching the maximum allowable age of a patent, the number of vendors of this technology has blossomed, as is shown in this report.
Differences in the Technology (ceramic vs. polymer)
The primary differences in ceramic vs. polymer technology which is important for the reader to understand from a market perspective is as follows:
Unique Aspects of the Polymer PTC Thermistor
Polymer PTC thermistors are used for overcurrent and temperature sensing applications only. Ceramic PTC thermistors are used for overcurrent applications and temperature sensing but also have created application specific markets such as degaussing of CRT monitors, heater elements and inrush current limiting in motor starting and lighting ballast circuits. They are also used in advanced probe assemblies consumed in the industrial and home appliance markets worldwide.
Unique Aspects of the Ceramic PTC Thermistor
Ceramic PTC thermistors lend themselves to smaller case size production because of their multilayered designs. Polymer PTC thermistors are more reliant upon surface area of extruded polymer sheets and therefore require greater surface area and larger physical case sizes to accomplish their overcurrent protection functions. However, in this version of this essay, we note that the gap between polymer technology and ceramic technology in PTC is narrowing. Ceramic PTC devices are now available down to the 0201 case size (EIA in inches) and polymer chips are now available in the 0402 case size.
PTC Thermistor Manufacturing Process (ceramic vs. polymer)
Ceramic PTC Thermistor Production Process
Ceramic PTC thermistors have been in existence for some time and their development has coincided with the development of television sets, wherein ceramic PTC thermistors were (and are) used for degaussing circuits, although the number of CRT monitor being produced globally in 2023 has dropped dramatically in favor of flat panel displays. This, in turn, has resulted in many Asian vendors of CPTC products to exit the market completely. Ceramic PTC thermistors are produced from ceramic slurries based upon doped barium titanate ceramic materials. Dopants can include magnesium, strontium or other rare earth materials that are included to control resistance. The ceramic is developed captively by the PTC thermistor vendor or purchased from a merchant vendor such as Ferro Corporation.
The ceramic begins as a powder, which is milled, doped and then mixed into aqueous or non- aqueous slurry, which is pressed into a disc shape (in a radial leaded component). Lead wires are attached, the product is sprayed with silver for conductivity and the component is fired in a kiln (otherwise known as a pressed pill process). The end product may be dipped in epoxy or coated with electronic glass for humidity resistance. In a chip design, the process is multilayered stacking of “green sheet” extruded ceramic upon which a layer of precious metal electrode (palladium + silver) is deposited upon each stacked layer. These chips are very small and cannot be distinguished from a grain of salt in their smallest iteration (i.e. the 0402).
Polymer PTC Production Process
The polymer process is much different. The polymer is doped with carbon black materials and melted in a pot to a certain viscosity. It is then extruded into thin polymer sheets. The polymer sheets are then irradiated (mostly by an external vendor, or in the case of TE Connectivity, captively) in a process known as cross-linking. The polymer is then cut into desired lengths and the active material is cut into round or square shapes (radial discs or squares and chips). Lead wires or terminations are attached and the product is dipped in epoxy. Costs to produce polymer PTC thermistors are inherently much lower than that of ceramic, and this gives the PPTC a competitive advantage based upon the most important attribute to the design engineer—price.
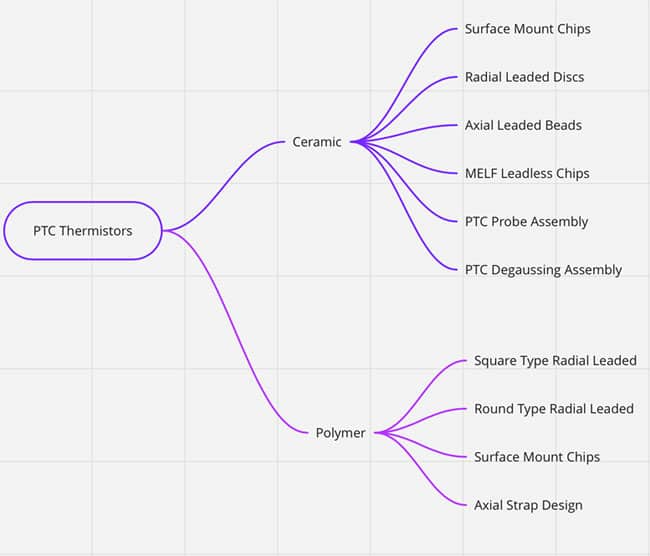
Ceramic and Polymer PTC Components Configurations
The following table illustrates the various ceramic and polymer PTC component configurations and vertical assemblies:
Ceramic PTC Chip Thermistors
The ceramic PTC thermistor can be considered the area of technical growth and development for the ceramic versions of varistors based upon barium titanate technology. Furthermore, the development of increasingly smaller case sizes down below 0402 into the 0201 and 01005 case size ranges are the area of research and development for advanced manufacturers of ceramic PTC thermistors. Applications for ceramic chip thermistors are PCB board mounted for temperature sensing and for overcurrent protection.
Currently case sizes are in the larger 3225 down to the ultra-small 0201 case size. The 0201 is brand new for 2023 and illustrates the technology direction to even smaller sizes. This is a growth market for vendors of ceramic PTC thermistors and many vendors offer a solution. The limitation of such technology is that its size is equal to its technical ability to sense excess current at specific voltages. However, as is the case with ceramic chip capacitors and thick film chip resistors, even the smallest case size products have applications in today’s ultra-small portable printed circuit boards.
Ceramic PTC MELF Designs
Some ceramic PTC thermistors are offered by the vendor in a MELF configuration, which is considered a surface mound design. Such configurations are manufactured through ceramic extrusion as opposed to stacking and are more cost effective. The designs are cylindrical and have metal terminations. They are preferred by the automotive industry. MELF resistors are also available and would be considered a like product.
Ceramic PTC Degaussers
Another vertically integrated product that employs ceramic PTC technology is the degausser which is used in the degaussing circuit in CRT monitor assemblies. However, this is a dying market as CRT monitors have largely been replaced by flat panel displays which require no degaussing. Small markets still exist for these designs in Turkey, Mexico and Brazil.
Ceramic PTC Thermistor Probe Assembly
The ceramic PTC thermistors are also consumed in the larger probe assemblies, where they are in turn installed in heating and ventilation equipment and in large home appliances (white goods) for thermal sensing. The probe assembly is a surefire way for ceramic PTC thermistor component manufacturers to vertically integrate their component production into the more profitable probe assembly markets. Probe assemblies have high pricing compared to the thermistors that make them work. Many manufacturers of ceramic PTC thermistors have realized this potential profit center and have acquired the equipment and skillsets to manufacture probes in-house.
Ceramic Radial Leaded PTC Thermistors
Radial leaded ceramic PTC thermistors continue to represent the largest market by configuration with respective to ceramic versions of PTC thermistors. Radial leaded designs are consumed in overcurrent protection, thermal sensing and for DC motor protection circuits worldwide.
Ceramic PTC Axial Leaded Designs
Some value added and application specific end-use markets in medical and defense require axial leaded ceramic PTC thermistors either for the purposes of adherence to an established but legacy military specification or because of unique volumetric efficiency requirements.
Ceramic PTC Rods and Disc Elements
PTC thermistors are also sold as bare elements for heating purposes in small home appliances (brown goods) and heating related equipment. The ceramic PTC thermistors in their naked form are manufactured in various shapes that adhere to the requirements of the end-use product and its respective volumetric efficiency requirements. Such shapes include square and round discs and ceramic rods.
Polymer PTC Square Type Radial Leaded
One of the more popular designs in polymer type PTC configurations is the square type PPTC design. These designs are used in industrial and professional electronics applications that require greater current handling than their round counterparts. The square design is clever way to increase the performance parameters of the finished thermistor without incurring much cost. The polymer nature of the thermistor allows for such a square design.
Polymer PTC Round Type Radial Leaded
The round type polymer PTC thermistor represents a large market for the polymer PTC vendors. The round type finds many applications as secondary line card protectors in telecommunications infrastructure equipment worldwide.
Polymer PTC Chip Type Thermistor
The chip type PPTC thermistor is the fastest growth portion of the PPTC segment of the overall thermistor market. The surface mount designs are finding many suitable applications in portable electronics and in applications in computers where the combination of volumetric efficiency requirements and the need for overcurrent protection are present.
Polymer PTC Axial Strap Type Thermistor
The axial strap type polymer PTC thermistor is somewhat unique in the components industry. It is design almost exclusively for battery protection and therefore is round and flat with a tab. In this instance, we see where the configuration of the component is adherent to an intended application (i.e. battery thermal overload protection). The polymer axial strap thermistor represents a significant and growing market worldwide.
Summary and Conclusions
Positive temperature coefficient thermistors are a complex market where ceramics compete with polymer infused with carbon. Ceramic is the legacy thermistor switch, and polymer is the newer invention.
Polymer PTC component designs comes in radial and chip formats as well as a variety of odd shapes due to battery protection requirements.
Automotive manufacturers involved in EVx propulsion prefer a solid state or polymer solution because of its tendency not to combust, but Paumanok also notes a clear trend to use ceramic PTC thermistors as heating elements in EVx sedans as well as preference for ceramics for inrush current limiting in the propulsion systems—a unique market opportunity.
Both ceramic and polymer technologies provide for desirable protection against overcurrent, but they radically differ with respect to their method of operation and the process in which they recover after exposure to overcurrent.
In effect, ceramic PTC thermistors are much more stable over time, but they are also more expensive than polymer PTC thermistors (when all types and available configurations are considered). As of this writing, the success of the polymer PTC thermistor, especially in telecom applications, is based on the combination of price and performance, which is directionally proportional to the available surface area of the active polymer material (thus, the square polymer PTC designs, which are somewhat unique but which increase the surface area over ceramic alternatives in pressed radial disc—a clever solution).
SMD and radial discs are tied to the telecom infrastructure and computer markets which saw turbulence due to the global pandemic. The markets in telecom, computer and consumer AV are feeling the effects of the post economic aberration in 2023.
Axial strap markets are consistently performing well over time because of their thermal sensing in battery applications—a key growth market. This also applies to the probe assembly markets for ICE automotive, medical and high reliability segments, which remain significantly profitable segments for ceramic and polymer PTC thermistors over time.