This article based on Knowles Precision Devices blog elaborates on importance of safety capacitors and its benefits especially in power electronic applications.
Safety capacitors are designed to mitigate the effects of transient voltages and interference in electrical and electronic circuits, especially high-voltage applications, ensuring their safe operation.
Even everyday devices need safety capacitors: modems and other telecoms equipment, AC-DC power supplies, power distribution switchgear, and electric vehicles (EVs) and other automotive applications.
The Role of the Safety Capacitor
In a circuit, safety capacitors used on AC lines filter high-frequency electromagnetic interference (EMI), or undesirable electromagnetic emissions or disturbances generated either by electronic devices or natural sources in the environment that can interfere with the proper functioning of other nearby devices or systems. This is known as EMI filtering, with the filter providing a safe path for noise while maintaining electrical isolation and safety.
When placed in combination with a series of inductors or resistors, safety capacitors form low-pass filters that attenuate the high-frequency signals (EMI) and allow the lower-frequency power signals to pass. This is the classic EMI filter setup—attenuating unwanted noise above a cutoff frequency. As more electronic devices enter the market, EMI filtering becomes even more crucial as there is an increased likelihood that EMI could cause a device to malfunction, crash, or fail.
In power electronics specifically, EMI filters take the form of power line filters that protect the line from upstream noise. While this list may differ depending on system requirements, the core components of a power line filter include:
- A common-mode filter circuit with two or more line-to-chassis capacitors and a common-mode inductor
- A differential mode (DM) filter circuit with at least one pair of series inductors and one line-to-line capacitor
- Compensation networks to adjust the filter’s quality (Q) factor and adapt the output impedance as needed
- Transient voltage suppression device(s) to defend against surges
Figure 1. shows an EMI filter structure that could be useful for single-phase AC applications or for DC power inputs.
Where Safety Capacitors are Used
To ensure safe operations and compliance with electrical safety standards, you’ll find safety capacitors in nearly every electronic device developed today – from industrial motor drives and HVAC systems to consumer appliances to medical devices, telecommunications equipment, and automotive electronics. For many of these applications, safety capacitors are crucial components that ensure user safety and reliable performance.
Classes of Safety Capacitors
In general, there are two classes of capacitors, Class-X and Class-Y, that are both used to minimize EMI in different applications.
- X Capacitors: Class-X capacitors, also known as “across-the-line capacitors,” are used between the wires carrying the incoming AC current. These offer line-to-line protection, which means that if there is a failure, a short may occur, but there is no risk of shock. An X capacitor failure usually causes a fuse or circuit breaker to open.
- Y Capacitors: Class-Y capacitors, also known as “line-to-ground capacitors” or “line bypass capacitors,” offer line-to-ground protection, which generally means that if a failure with the ground occurs, there is a risk for shock. However, Class-Y safety capacitors must meet rigorous specifications, minimizing the chance of electric shock.
- X/Y Capacitors: Some safety capacitors handily combine classes, for example, X1/Y2. This simply means that the capacitor can be used as an X1 capacitor in an across-the-line application or as a Y2 capacitor in the line-to-ground portion of the circuit.
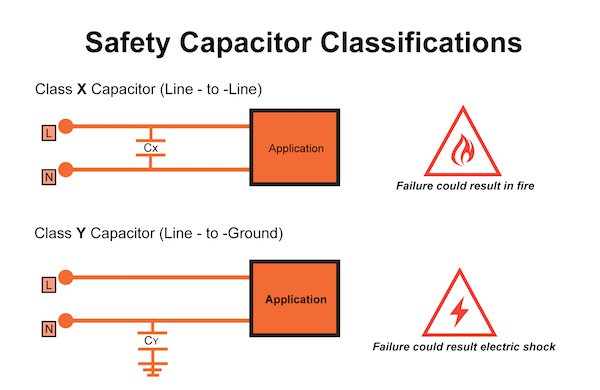
Safety Capacitor Subclasses
As mentioned, both X and Y capacitors are further broken into the following subclasses according to their pulse voltage withstand capability and rated voltage (more details in Table 1):
- X Capacitor Subclasses:
- X1: For higher surge levels (≥2.5 kV and ≤4 kV)
- X2: Most common in consumer electronics (≤2.5 kV)
- X3: For ≤1.2 kV, less common
- X Capacitor Subclasses:
- Y1: For higher insulation and impulse voltage (>500 VAC, up to 8 kV)
- Y2: Common for 250 VAC operation
- Y3/Y4: Lower ratings, used in less critical applications
*2x Y2 or Y4 rated may bridge double or reinforced insulation when used in series
By understanding the differences between the different capacitor classes and subclasses, you can optimize product development while ensuring user safety, product compliance, and reliable circuit performance.
General Considerations for Selecting a Safety Capacitor Technology
When comparing whether to use a multilayer ceramic capacitor (MLCC) or film capacitor for your safety capacitor, you need to consider the capacitor’s construction, performance characteristics, and suitability for specific safety roles as well as the capacitor’s:
- Temperature range
- Size constraints
- Voltage rating
- Capacitance value
- Cost
Let’s further explore the characteristics of both MLCCs and film capacitors.
Ceramic Capacitors
In general, for line-to-ground configurations, or Class Y capacitors, safety requirements dictate that failure must not result in a conductive path that could pose a shock hazard. MLCCs, when properly rated, can meet these requirements. Some benefits of using MLCCs include the following:
- Compact size, allowing for high capacitance in a small footprint, which is ideal for space-constrained designs
- Cost-effective manufacturing makes ceramics attractive for high-volume, cost-sensitive projects
- Low equivalent series resistance (ESR) and equivalent series inductance (ESL) support effective high-frequency EMI suppression
Some challenges with using ceramic include that ceramic generally has a lower voltage rating than film, which can limit its use in high-power designs. Additionally, while some MLCCs can withstand high temperatures and humidity, others may be susceptible to performance drift under environmental stress, which can impact long-term reliability.
As a result, ceramic is well suited for Y1 and Y2 safety capacitors, especially those used in appliances, chargers, or compact consumer electronics where space and cost are driving factors.
Film Capacitors
Film capacitors are most commonly used in Class X applications where they are installed across the AC line. Therefore, these capacitors must be able to withstand large voltage surges and recover from a dielectric breakdown with only a small reduction in capacitance. Advantages of using a film capacitor include the following:
- High voltage tolerance that enables reliable performance
- Self-healing properties that allow the capacitor to recover from small dielectric failures without catastrophic failure
- Excellent stability over time and varying environmental conditions to ensure long service life and consistent safety compliance
Since film capacitors are typically larger in size, it may be challenging to use these capacitors in densely packed assemblies. Film capacitors also typically cost more than ceramic options, which may be a consideration for cost-sensitive markets.
As a result, film is typically a good fit for X1 and X2 safety capacitors used in industrial equipment, power supplies, or any design that must withstand line surges and operate over extended periods.
Selecting the Right Safety Capacitor for Your Design
The choice between using ceramic or film for your safety capacitors requires a clear understanding of the capacitor’s role, requirements, and environmental operating conditions. Ceramic capacitors offer compactness and cost advantages, making them well suited for many Class Y roles. Film capacitors, with their robust voltage handling and reliability, are typically the preferred choice for demanding Class X applications.