This blog article written by Jeff Lee, KYOCERA-AVX Corporation explains the benefits of using tantalum capacitors in electric vehicle applications.
Introduction
An electric vehicle is a car powered by electricity unlike internal combustion locomotives that obtain driving energy by burning fossil fuels, they rotate the motor with electricity accumulated in the battery to obtain driving energy.
Electric vehicles are largely composed of on-board chargers (OBC), electric power control units (EPCUs), motors, speed reducers, and high voltage battery. The motor of an electric vehicle is a high-efficiency and high-power driving motor and has high output and rotational power. Unlike internal combustion vehicle engines, the electric motor can be made to minimize noise and vibration generation while driving.
The main control unit is the electric power control units and it is largely composed of inverters (Inverters, LDCs, VCUs).
- Inverter: Conversion of power between high voltage battery and motor (AC<—>DC)
- Low voltage DC-DC converter (LDC): Converted into low voltage (12 V) and supplied to electronic components in high voltage battery.
- Vehicle control unit (VCU): A control tower that control the in-vehicle power controller.
- On Board Charger (OBC): converts external AC power into DC power to charge a high voltage battery.
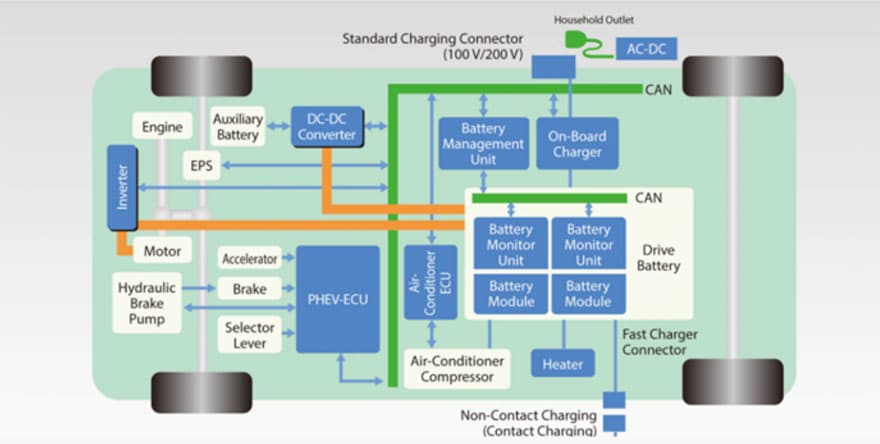
Capacitor Comparison
Generally, capacitors are used for the following purposes, and differences in applicable applications occur due to differences in characteristics for each capacitor type. The purpose of the capacitor is below.
- Coupling
- Decoupling
- Filtering
- Energy storage/supply
- Impedance matching
- Snubbers and many more applications
As shown in the table below, the tantalum capacitor has a narrow voltage range rather than others, but has advantages of wide range capacitance value, ESR, and temperature character.
Tantalum Capacitors
Tantalum capacitor capacitance range extends up to some thousands µF. The capacitors are characterized by a high CV product per volume unit, especially when high CV powders above 200k CV/g are introduced for low voltages and above 80k CV/g for higher voltages.
The conventional solid electrolyte is MnO2, however conductive polymer types are more and more favorable due to its lower ESR and reduced ignition features. On the other hand, the MnO2 types are more robust against thermo-mechanical stress, stable electrical parameters under high temp & high humidity environments, thus high reliability and longer operation lifetime applications still uses mostly established reliability MnO2 types as the main tantalum solid capacitor technology.
The defects in tantalum capacitors are mostly due to initial faults (infant failure region). After that, the device is exceptionally stabile in the field. (Polymer tantalum failure rate may increase due to a wear out phenomenon that can be averted with derating). These devices exhibit a very stable defect rate compared to other capacitors and due to its reliability characteristics, it is possible to ensure long term stability and reliability when using tantalum capacitors.
Electrical Vehicle Main Systems
Electrical Vehicle Traction Inverters
The purpose of DC capacitors in an electric vehicle traction inverter is to decouple the load from the DC supply. In this role, the capacitor absorbs large ripple currents generated by the switching sequence of the inverter. In general, a DC capacitor applied to a three-phase inverter can see up to 60% of an RMS load current and thus the capacitor needs to store a certain amount of energy to prevent ripple voltage.
Thus, a capacitor with large capacity occupies a substantial space in an inverter, and because of that it is important to minimize a volume of capacitor bank and maximize power and energy density to optimize a volume of traction inverter. The most commonly used capacitors applicable to the relevant inverter are electrolytic capacitors, ceramic capacitors (MLCC), and film capacitors.
Among them, an electrolytic capacitor is the most widely used in existing motor driving applications with the lowest cost and highest energy density, but since it has a short life, limited current conductivity, and limited low frequency characteristics, it is limited to use as a DC filter capacitor. In contrast, a film capacitor is widely used as an application capacitor of an EV motor unit due to high reliability, high current conduction capability, high frequency operation, and low ESR compared to an electrolytic capacitor. However, it may not be a suitable solution for inverters seeking miniaturization due to its disadvantage of being larger than the electrolytic capacitor of the dielectric.
Another, highly preferred capacitor for the inverter is the MLCC. MLCCs can be smaller than other capacitors and can be used at high voltages. However, there is a limitation to the practical capacitance. Beyond that high capacity cannot be easily implemented due to CV limitations relative to (high) voltage ratings.
A solution that can overcome these shortcomings in some applications may be tantalum capacitors. The tantalum capacitor cannot achieve a high voltage, but it can produce a larger capacity because it is higher than MLCC in terms of capacity.
However, the voltage range of tantalum technology is limited by relatively low (but increasing) voltage rating. Generally these devices can be used as a smoothing capacitor on the front end of lower voltage IGBTs in the inverter circuit. Another use is for general purpose low to moderate voltage rated filters with large capacity and small ESR (in the case of low ESR Polymer tantalum products.
LDC (Low Voltage DC-DC Converter)
Selecting a larger capacitance value typically reduces the output ripple. However, unnecessarily large capacitance values increase the cost by increasing the dimensions of the capacitor. There is an optimization consideration of an allowed ripple value and then selecting a capacitor technology and capacitance value. Examples are shown in Table 2. below.
If for example a DC/DC converter is not compatible with low ESR capacitors, using a particularly low ESR capacitor technology may result in abnormal switching. So, if low ESR capacitors are used in the continuous mode, check the load-transient response to confirm that the output voltage is rapidly stabilized (commonly target two switching cycles).
The ripple increases in proportion to the ESR value and in inverse proportion to the CL value. In the case of an aluminum electrolytic capacitor, the ESR value is so large that a ceramic capacitor is typically connected in parallel for stabilizing and optimizing output current.
Conclusion
Electric vehicles are a new platform with increased quality and reliability demands beyond existing internal combustion engine car. Optimized performance & reliability can be achieved by using suitable capacitors chosen specifically for each application.
In some use cases tantalum capacitors can be suitable for electric vehicle applications and next generation low ESR polymer tantalum help expand the number of applications allowing use of this technology.