Vishay Intertechnology released white paper on use of MLCCs as electrostatic discharge protection in automotive environment. Authors Thomas Wächter, Brian Ward, Eli Bershadsky, and Oded Shiek of Vishay Vitramon.
Today’s automobiles use increasingly more electrical and electronic components. Computers now control many automotive functions to the point that traditional mechanical and pneumatic systems are almost obsolete. Proper functioning of all car electronics depends on eliminating or minimizing the effects of the electrostatic discharge (ESD) phenomenon, which can be harmful to the circuit components.
Prevention of damage to the electronic circuit can be accomplished using multiple suppression devices. Multilayer ceramic capacitors (MLCCs) are one of the solutions used to protect components from ESD damage. Since integrated circuits (ICs) are most prone to damage by ESD, MLCCs are placed close to the board connection contacts or directly next to the IC connections in order to absorb and then level the unwanted voltage spikes.
MLCCs of different capacitance values are used at different places in the circuit according to its design: high capacitance MLCCs shunt out high voltage bursts and low capacitance MLCCs are used in circuits where fast responses are required. The origin of the voltage burst could be human touch during manufacturing of the circuit board or operation of the car’s electrical systems. The surge could also come from other equipment that contacts the susceptible circuits.
Different standards based on models of discharge originated by the human body or by machines have been developed to define the level of the ESD protection provided by the MLCCs.
Today there are two major standards addressing the ESD test methods used for validation of MLCCs:
- AEC-Q200 Automotive Electronic Council human body model (HBM) electrostatic discharge (ESD) test rev. B
- IEC 61000-4-2 International Commission; electrostatic discharge immunity test
Vishay recently released a new series of MLCCs designed for ESD protection in the automotive industry. These capacitors are manufactured with X7R ceramic in 0603, 0805, and 1206 case sizes using precious metal electrodes (PME) and a wet build up process.
Capacitors manufactured from the wet buildup are characterized by high reliability. All capacitors meet Vishay Green and RoHS / ELV requirements and can be supplied with different types of terminations.For a capacitor to be effective in ESD suppression, it must not be damaged by the ESD strike. So, to test a capacitor, it is exposed to one of the surges defined in the specification, using a circuit as depicted in Figure 1.

The choice of parameter values in that circuit (charge voltage, charge capacitor, discharge resistor) are chosen to meet the definition of the specific waveform under evaluation. The parameters of the device under test (capacitance, dissipation factor(DF), and insulation resistance (IR)) are measured before and after the application of the surge.
A decrease of capacitance below the defined capacitance or decrease of IR by one degree of order of magnitude are indications of ESD failure in the capacitor.
The typical causes of ESD failure are poor capacitor design, existence of the defects, loss of connection of electrodes with termination pads, etc. Changes in these parameters determine whether the capacitor can pass the surge test.
To establish the AEC-Q200-002 ESD level, parts are tested at increasing severity levels until a failure occurs. A flowchart of this process is shown in Figure 2.
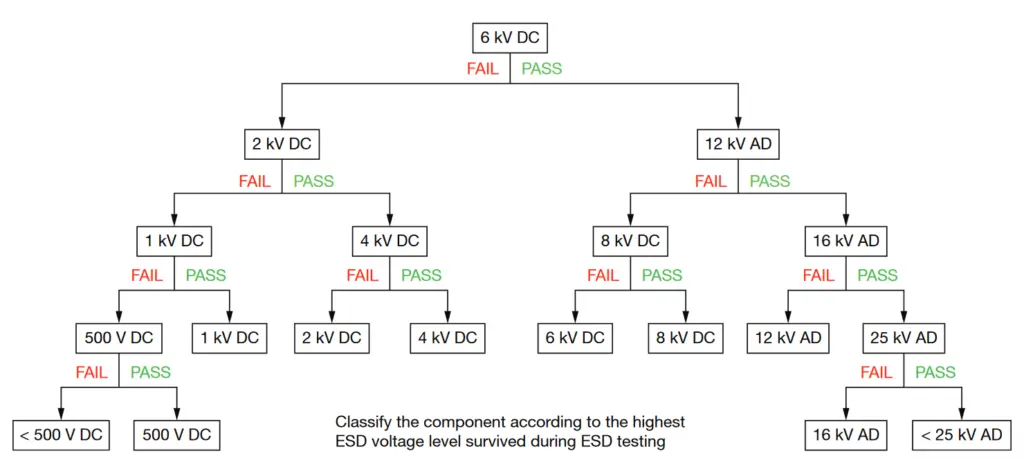
Following this process, the part receives the rating at the last level it passes. For IEC-61000-4-2, parts are tested at the different severity levels (Table 1). Successful performance of the test is achieved using the criteria described in the paragraph above to determine the rating level.
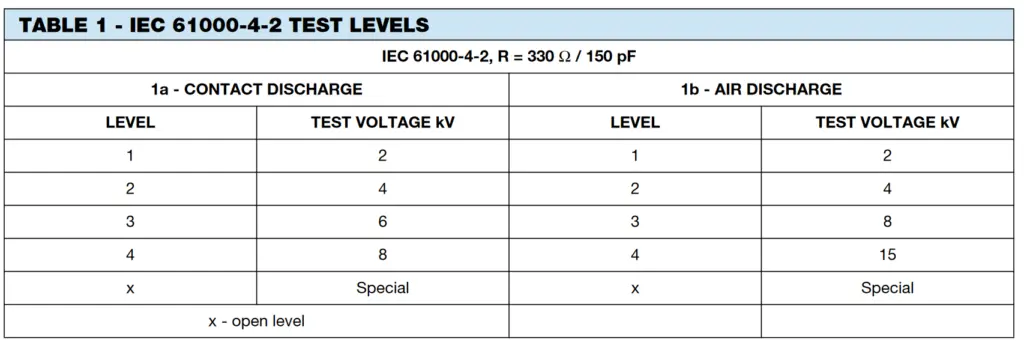
The MLCC protects components by absorbing the energy of the ESD pulse, thus diverting it from the sensitive electronic components. A key factor in how much energy the MLCC can absorb is its capacitance: the energy absorbed is proportional to the capacitance value.
Complicating this scenario is that the capacitance is not constant for the Class II materials used for these MLCCs. In fact, as the voltage applied increases, the effective capacitance decreases. This is known as the Voltage Coefficient of Capacitance, or VCC.
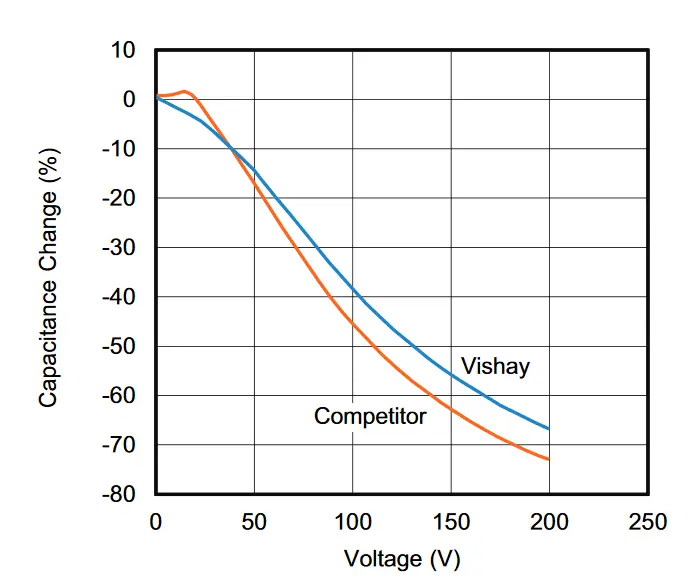
The material used to build the Vishay MLCCs results in a product with better VCC than products built on the material commonly used in the market, as shown in Figure 3.
That means that the Vishay part retains more capacitance at voltage than typical MLCCs – which means more energy absorbed in the MLCC and less transmitted to the sensitive electronic components. Testing of the Vishay MLCCs has produced a series of ESD suppression MLCCs across three body sizes and many capacitance values. A summary of the offering is presented below:
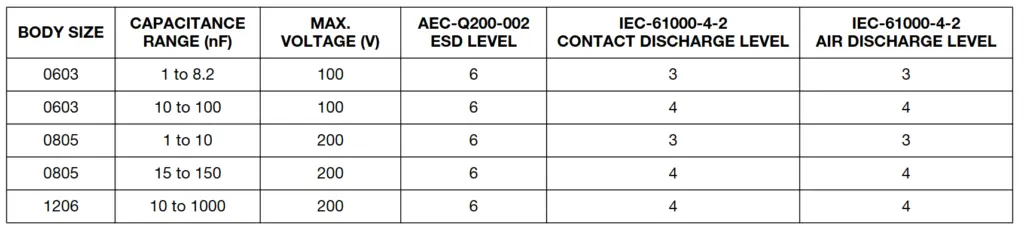