Nan Zhang in this blog article explains Knowles’ MLCC capacitors StackiCap capabilities, benefits and applications.
From industrial to automotive to aerospace applications, power electronics are demanding higher capacitance in smaller packages.
Therefore, to meet both capacitance demands and size requirements, electronic designers simply cannot continue to add more capacitors.
While capacitor stacking is an option, many stacked assemblies are still quite large and stacking often introduces new failure modes, such as piezo electric cracking (Figure 1).
To overcome this issue, many capacitor manufacturers’ solutions use special, stronger dielectric formulations, but these usually come with trade-offs regarding dielectric constant, and therefore the ultimate capacitance value available.
Knowles Precision Devices offers a solution designed to provide high capacitance value (CV) in a compact package while reducing the risk of piezo electric cracking.
Known as StackiCap™, this surface-mount multi-layer ceramic capacitor (MLCC) offers the greatest volumetric efficiency and CV per unit mass of any high-voltage X7R ceramic capacitor available.
Figure 2 shows how single StackiCap components can replace various stacked assemblies. The electrical details of StackiCap are shown in Table 1.
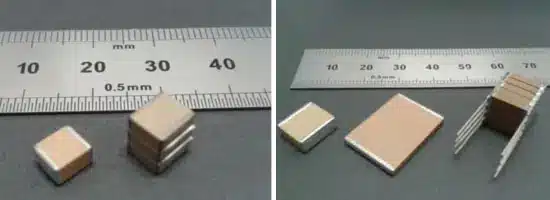
Electrical Details | |
Voltage Range | 200V – 2,000V |
Maximum Capacitance | 5.6µF |
Temperature Coefficient of Capacitance (TCC) | ±15% from -55°C to ± 125°C |
Dissipation Factor | ≤ 0.025 |
Insulation Resistance (IR) | 100GΩ or 500secs (whichever is the less) |
Dielectric Withstand Voltage (DWV) | Voltage applied for ± 1 seconds, 50mA charging current maximum |
Ageing Rate | < 2% per decade |
The Technology Behind StackiCap
With a novel and patented* inbuilt stress relieving layer, StackiCap capacitors exhibit the electrical and physical behavior of multiple, thinner, components while exploiting the manufacture and process benefits of being a single unit.
The stress-relieving layer included in StackiCap is made of a combination of already utilized material systems and is formed during the standard manufacturing process. The layer is positioned in the place(s) where mechanical stress is the greatest, which allows for mechanical decoupling of the multiple component layers.
To further reduce the risk of mechanical stress damage, StackiCap terminations use our proprietary FlexiCap™ flexible termination material. Coupled with the fact that there is no need to attach components together to form a stack, StackiCap does not require lead frames, which means we can use standard tape and reel packaging with pick and place capability for StackiCap.
Key Applications that Can Benefit from Using StackiCap
Between Knowles unique patented construction and FlexiCap™ termination material, StackiCap™ range of MLCCs are suitable for a variety of applications including power supply filtering, lighting, aerospace electronics, DC-DC converters for industrial and automotive markets, and other high voltage applications where a large amount of capacitance is required. The majority of StackiCap MLCCs are also AEC-Q200 qualified.
Overall, StackiCap range of MLCCs offers a significant reduction in required PCB real estate for an equivalent capacitance value when board space is at a premium.