Induction heating occurs when an electrically conducting material is placed within a varying magnetic field. The heating is due to eddy-current losses within the material (in magnetic materials such as iron, some heat is also generated by hysteresis losses). Let’s have a look at needs for capacitors in this application field.
An important aspect of the process is that the heat is generated by the material itself without the need for an external radiant heat source. This means that induction heating is clean and fast. It also highly repetitive; once the equipment has been set up, part after part can be heated with identical results.
Induction heating finds applications in many industries for heat treating activities such as annealing, forging, welding, brazing, curing and sealing.
INDUCTION HEATING INDUSTRIES AND APPLICATIONS
Induction heating is a natural fit for automated production lines and, because magnetic fields can permeate glass and similar materials, it works in controlled environments.
Some of the industries that use induction heating in a big way are:
- The automotive industry for treating bearings, brakes, drive trains, gears joints and shafts. Frames, seats, bumpers and steering wheels are also heat treated.
- The bus and truck industry for similar, albeit physically larger, applications and the ship-building industry for larger still; It is also used for repairing and reshaping damaged hulls. The commercial and recreational marine engine industry uses induction heating processes in production.
- The sports and fitness industry for golf clubs, goal posts and exercise equipment.
- The wind-turbine industry for gear-handling systems.
- The aeronautics and aerospace industries for heat treating components and producing special alloys.
- The oil and mining industries for pipe and tool manufacture.
- The railroad industry for an array of locomotive parts.
- The commercial, residential and industrial construction industries for the production of structural sections.
Induction Heating Equipment
The design and manufacture of induction heating equipment is a major industry in itself, and machine types are many and varied.
Some types are:
- large industrial heat treatment and processing systems
- mobile heat generators
- solid state welders
- modular forging systems
- custom configurations
Induction Heating Capacitors
The three main constituents of an induction heating machine are the working coil, the power supply and the tank circuit. The working coil generates the electromagnetic field that produces the heat, the power supply converts the line signal to an alternating current and delivers it to the workhead, and the tank circuit generates the operating frequency.
Capacitor designs suitable for use in induction heating equipment include:
- water-cooled plastic film
- ceramic capacitors
The suitable capacitors are developed in order to have minimized internal losses thus it can work in electric circuits with high frequencies, by very high current and high working voltage. Fluid cooling capacitors can achieve quite high working rated power, in range from hundreds of kVA to few MVA.
The internal losses are the reason of the rise of the heat which have to be removed. This heat could cause the destruction of the capacitor if the heat removal is not sufficient. Permissible temperature rise of the capacitor effected by the power dissipation also depend on the ambient temperature that needs to be considered during design-in. See below Fig.
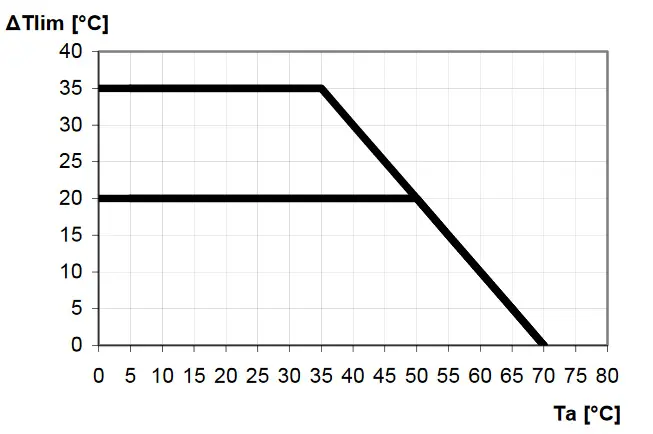
By the application of the capacitor is useful to make energetic balance and choose appropriate cooling of the capacitor. Capacitors for induction heating machine tank circuits are an important market for some capacitor manufacturers.
Manufacturers such as Alcon Electronics, Dacpol, Celem, Illinois Capacitor, Iskra, ZEZ-SILKO, produce conduction or water cooled plastic film capacitors primarily for the induction heating market, while many high RF power water-cooled ceramic capacitors from manufacturers such High Energy Corp. and Vishay are well suited to the task.
featured image: induction heating capacitor range example up to 5 000kVA; image credit: ZEZ-SILKO.