Space on a PCB is in short supply, but the demands placed on the technical properties of inductive components continue to rise. Choosing the right technology can make the difference in successfully mastering the balancing act between space and performance. Rutronik noted some general guidelines in its blog on miniaturization and inductor downsizing.
In the automotive sector, it has long been standard practice to define the available development space for modules before the development using actual components even begins. In industrial applications, there are also increasingly size restrictions in the interest of saving space, weight and cost. At the same time, the modern designs of many applications require higher currents, higher switching frequencies, higher efficiency levels and better temperature management.
Power inductors
A conventional application for inductors is filtering electrical interference in a conductor. To filter push-pull interference in a current signal, coils with a single winding are used. It is conventional to use a ferrite core to boost the filter effect, although saturation effects can occur with high currents and temperatures. Coils with much higher buffer inductance values than are actually required for the application are often used as a workaround for this effect. The drawback with this over-specification is that components tend to become significantly larger and more expensive as a result.
An elegant approach to avoiding this is the use of coils with a different core material such as iron or metal powder. Figure 2 shows the inductance curve of ferrite and metal powder chokes as current rising and at different temperatures. The metal powder components exhibit a more stable inductance curve at both 25°C and 150°C compared to the ferrite models.
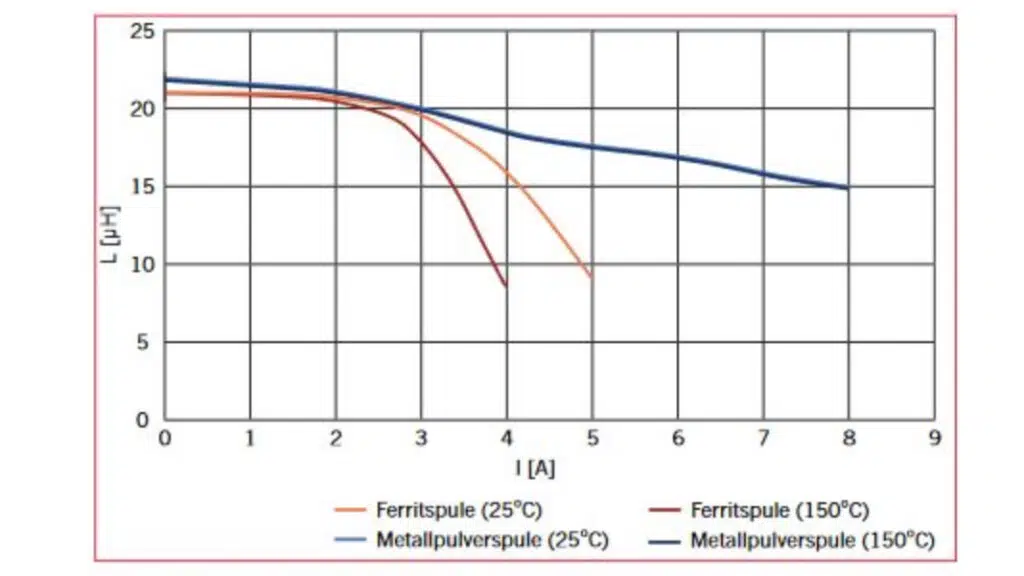
When selecting products for real applications, this enables the use of coils with a lower rated inductance. This generally results in a smaller footprint and consequently also a cheaper component.
The technology and production process of metal power inductors have since adjusted to the needs of the market, satisfying the technical requirements of modern applications and providing a competitive commercial offering.
But it’s still worth taking a closer look at the specifications of the application. Instead of comparing the rated inductance values in the data sheets when selecting components, a more pertinent question would be “which inductance is required with a real current at conventional operating temperatures?” The consistent behavior of metal powder coils also provides the confidence of passing EMC testing reliably.
Transducers and EMI filters
Transducers and EMI filters (electromagnetic interference) are created relatively rarely using standard products – the requirements placed upon these products are simply too diverse. Manufacturers have made great technological strides in the development of these products in recent years. Especially when it comes to power supply units in the field of power electronics, the specifications are often pushed to their limits with conventional ferrite core designs for high-frequency transducers. The transducer is often the tallest component on the PCB, making its miniaturization a matter of some importance. With its large volume, it also plays a significant role in the heating of the system as a whole.
To enable the creation of smaller form factors and more efficient circuits, “nanocrystalline” cores have been developed. These materials offer much greater magnetic permeability (see table), allowing for the generation of higher magnetic flux densities in the component. They also make transducers with a higher switching frequency possible, which means lower losses.
Another trend is open designs that are not encapsulated by a package, but are simply mounted on a base plate to comply with insulation resistance requirements. This saves space and helps better dissipate heat.
Conclusion
There are inductors available today that use different – sometimes novel – materials and designs to meet all of the key requirements of modern applications, namely small size, low weight, higher currents and switching frequencies, and optimized heat control. When selecting components, it is essential to take into account not only the rated values of the inductors, but also the values arising in real applications.