Safe, reliable resistors extend surge protection, offer green performance in medical contact devices. Stephen Oxley, senior engineer, Applications & Marketing at TT Electronics plc. describes some consideration for its design and applications.
Medical designers face a complex realm of diverse applications and performance environments for the devices they develop. An aging population, a greater number of healthcare settings, and increasing demand for smarter, more convenient devices are factors keeping designers on their toes as they face continual competitive pressure for equipment that is faster and smarter, with unmatched performance and precision.
These complex devices also must work closely with the human body, blending sophisticated digital components with the realities of the analog patient. For this reason, resistors – passive components that oppose the flow of electrical current – play a critical role in medical designs. Each active integrated circuit (IC) requires as many as 20 resistors in a medical device design. Off-the-shelf resistors are often insufficient, driving designers to specialized components purpose-built to handle diverse medical challenges such as high voltage and magnetic interference.
Understanding options is crucial, as various medical applications have different priorities for resistor performance. For example, in imaging, X-ray systems require ultra-high voltage resistors; magnetic resonance imaging (MRI) scanners demand non-magnetic resistors; and ultrasound devices need integrated resistor arrays. In instrumentation and analysis, accuracy and stability are key. And, some of the most challenging resistor applications are found in contact devices, those connecting directly with the body that are often tasked with safely delivering high-energy pulses or detecting and monitoring biological signals.
Human contact
Automatic external defibrillators (AEDs) are life-saving tools widely available today, but their success is based on the ability to guarantee patient safety as they provide electrical pulses. The same safety is needed for connected medical devices such as electrocardiogram (ECG) monitors. Protection resistors with high energy ratings support this application. This may be delivered using pulse-withstanding thick film elements and with double-sided chip designs that provide 2x the energy capacity of a traditional component in the same footprint. Most importantly, defibrillation energy must reach the patient, something generally achieved by designing pulse-withstanding resistance directly into the lead set of monitor input circuits. The proportion of defibrillation surge energy dissipated by a protection resistor decreases with rising ohmic value, meaning designers must opt for the highest value consistent with the requirements of the monitor function.
A simplified schematic of a defibrillator charge circuit is shown in Figure 1. The stable and repeatable measurement of the charging voltage is a critical function of this circuit, as this determines the amount of electrical energy delivered to the patient. As the energy delivered is proportional to the square of the voltage, a 1% tolerance requirement for the energy will demand a 0.5% tolerance on the voltage control.
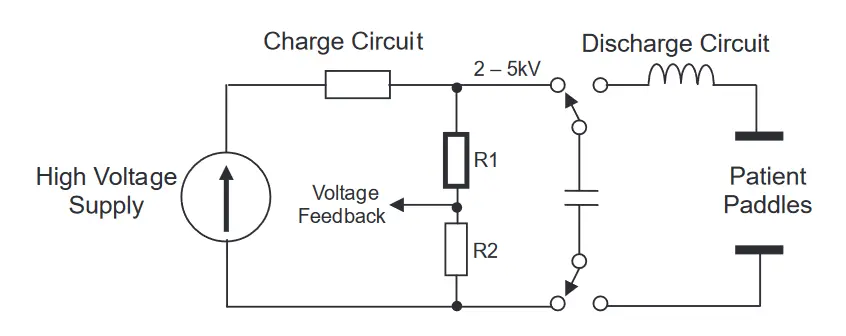
In this circuit R1 is a high value resistor, normally in the range 5M to 50M, which, together with a commodity chip resistor R2, forms a potential divider for voltage feedback. The critical features of this high voltage resistor are linearity, expressed by voltage coefficient (VCR) and temperature coefficient (TCR), and long term stability under voltage stress. In addition to this, the rapid growth in the non-professional AED segment adds the requirement for compact footprint and suitability for a wider range of environmental conditions, including high humidity.
Designers must also consider the parameters of the test circuit itself, factoring in the number of leads in the lead set based on electromagnetic compatibility (EMC) standards such as IEC601. In this case, a protection resistor – directing the appropriate surge to the patient and protecting attached monitors from electrical damage – must deliver energy ratings from 25.00J at 1kO to 0.25J at 100kO. While this has traditionally relied on composition technologies, thick film solutions are gaining momentum. Also available are specialist resistors pre-qualified to IEC 60601/61000 standards, minimizing risk and accelerating product development.
Consider that the total energy in a defibrillation pulse may be as much as 350J. Protection resistors, designed within a monitor cable set or on a printed circuit board (PCB) within the monitor itself, absorb some of this energy to block defibrillation energy from entering the monitor. Even 1% of that energy is significant for a small electronic component to handle.
Other options, proven in industrial applications, are also adding new value to medical designs. Pulse-withstanding chips (PWC) and high pulse-withstanding chips (HPWC) offer greater levels of energy capacity; for instance, as an untrimmed resistor with 5% tolerance, HPWC offer up to about 1J capacity in the defibrillation surge duration.
The defibrillator pulse chip resistor (DPCR) is an advancement in high-density signal carrier (HDSC) options. It’s an untrimmed, two-sided version, doubling surge capacity via its thick film material on both sides of the chip. Optimized for monitor inputs, this compact footprint option provides a guaranteed defibrillator pulse-withstand performance. Surge protection is maximized two ways – for deliberate surges such as from a defibrillator, and for random ones, such as those resulting from electrostatic discharge (ESD). Pre-qualified for maximum energy and voltage performance, the DPCR is pre-qualified to IEC 60601-2-27 for defibrillation surges and IEC 61000-4-2 level 4 for ESD. It offers a robust design option that reduces risk and quickly moves designs to market.
Design value
Green options are also on the rise, helping designers meet environmental mandates for medical devices. Employing a resistor that contains no lead meets standards for lead-free design without exemption – designs have inherently greater longevity and reduced need for component replacement as lead-free design requirements continue to expand.
Specialized resistors are making a difference in medical design. Extending value well beyond mass-produced commodity components, these pre-qualified options access features such as high electrical ratings, high surge performance in a small footprint, and environmental value – enabling medical designers to deliver safe, stable devices that help save lives.