This article explains operation principles, features and packaging options of thermistors.
NTC Thermistors
Simplified, the thermistor material consists of doped granule compounds containing various oxides that by means of binders have been pressed to a desired shape and then sintered.
The terminals either are inserted into the resistor body or soldered to metallized surfaces. There are a number of encapsulation types.
Designs
Thermistors exist as rods, discs, beads covered with lacquer, epoxy, glaze or melted glass and as SMDs.
SMD thermistors in low ohmic designs are made with a number of internal electrodes as shown in Figure 2. The reduced resistance is achieved by a construction that connect โresistor elementsโ in parallel inside the thermistor body.
Temperature Dependence and Tolerances
NTC stands for negative TCR (Negative Temperature Coefficient). The temperature dependence is strong and exponential and follows the formula
The material constant A determines the resistance and B its temperature dependence, i.e. the slope of the resistance โ temperature curve. T means the temperature in Kelvin (ยฐC + 273). If we apply the formula [1] on a reference temperature T0 and a general temperature T and combine the two expressions we obtain the formula
The constant B generally is determined by measurements at 25 and 50 ยฐC. It usually has values between 2500 and 5000. The value varies a little with temperature. Hence the โ symbol in the formulas. The thermistor material shrinks strongly during the sintering process which causes great difficulties keeping the tolerances on both the R25 and the B value within specified limits. The B value is stated with tolerances that usually are 5 %. The reference value R0 relates to 20 or 25 ยฐC and has tolerances of 5, 10 or 20 %. However, by sawing already sintered chips to close dimensions one increases the accuracy considerably. R25 tolerances of 0.2โ โ โ 1 % no longer are exclusive, nor are tolerance of 1 % on the B value. The result of these superimposed tolerances looks like the illustrations in Figures 3. to 5.
For more accurate applications two or more points on the Resistance/Temperature curve โ abbreviated R/T curve – are specified, a so called curve-tracking application. The B tolerances then are of less importance. The tolerances of such a two or three point sensor may be stated either as a resistance deviation โR in percent of R or as a temperature deviation โT in ยฐC, at the temperatures in question (Figure 6). In the latter case we have to calculate โR by means of the temperature coefficient ฮฑ in the Formula [3].
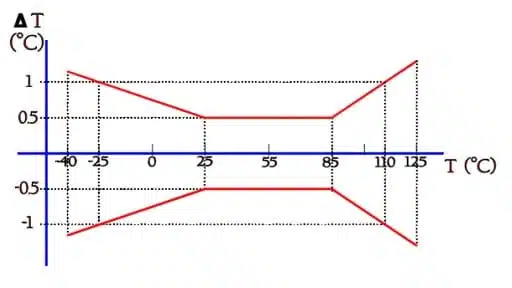
Slope and Temperature coefficient
The slope of the R/T curve for an NTC thermistor is determined by the B value. Sometimes the temperature coefficient a (or also called ฮฑ) is also specified. If we derive the expression in Equation [1] we obtain:
Compared to general resistor TCR formula, where TCR = 1/R x โR/โT, we find the same basic expression as for ฮฑ. As follows from Equation [3] ฮฑ varies strongly with temperature. Around 25 ยฐC ฮฑ usually has values between โ3 and โ5.5%/ยฐC. Yet another way of specifying the slope of the R/T curve is by using resistance ratios. For example the ratios of R0/R50 or R25/R125 are compared. The ratios are stated with tolerances.
Self-Heating Effects
The self-heating of the NTC thermistor influences the resistance. If we apply a voltage over the thermistor the current at the beginning rises linearly according to Ohmโs law. But as soon as the internal power generates palpable heat the resistance starts decreasing. Further voltage rises gradually force resistance reductions that occur faster than the current increases. The V/I curve starts declining (Figures 7. and 8.).
The example in Figure 8. helps us realize how the parameters V, I, P and R belong together.
Thermal Cooling Time Constant, Heat Capacity and Dissipation Factor
Another two parameters are associated with Figure 8., namely, time and temperature. Size, shape and surrounding medium influence the velocity with which the temperature is changed. A measure of the change velocity is the thermal time constant, t. It is specified for an in-still-air freely mounted thermistor body under zero power conditions and is defined as the time required for the temperature to change by 63.2% – exactly (1-1/e) – of the difference โT between the initial and final body temperature, T0 respectively Tโ (Figure 9).
With designations from Figure 9. the thermistor temperature can be written:
The heat capacity describes how many Joules (Ws) that have to be conveyed to the thermistor body in order to rise its mean temperature by 1 ยฐC. The dissipation factor D is expressed in mW/ยฐC (or mW/K) and is specified as the power that raises the mean temperature of a thermistor body by 1 ยฐC (or 1 K) when freely mounted in still air. The power dissipation capability, of course, can be increased by means of fans, heat sinks or another cooling medium, for example a suitable liquid. In that case one obtains a practical time constant. If the thermistor is placed in a suitable liquid the time constant is decreased drastically. Among other things this is utilized at production control. The thermistor is immersed into a precise temperature controlled bath and thus in a very short time is conveyed to the stable measurement temperature.
Thermistor Application / Choice of Type
We can distinguish three main groups of applications:
- The temperature dependence of resistance R = f(T) is utilized. The temperature then may be determined
- either by the surroundings
- or by the internal power of the thermistor.
- The time dependence R = f(t) is utilized, i.e. we make use of the inherent thermal inertia of the material.
- The typical NTC characteristics of the material is utilized. When we choose a thermistor we have to consider the following requirements
- Environment and encapsulation requirements. Glass, glaze cover, lacquer/epoxy, no encapsulation.
- Temperature range.
- Shape and design. Chip/SMD, rod, disc or bead thermistor.
- Soldering, spot welding or gluing.
- Reference temperature R25 and temperature coefficient ฮฑ (-B/T2).
- Tolerance requirements on R25 and B value. Is it a point-matching or a curve-tracking R/T application?
- Power dissipation a) without perceptible heating. b) with maximum change in resistance value.
- Thermal time constant ฯ.
Linearizing the R/T characteristic
If we want a temperature dependence with a particular slope of the R/T characteristic over a broader temperature range, it is usually difficult to find a suitable curve shape. However, by means of fixed resistors combined with the thermistor it is possible to adjust the R/T curve in a desired direction. Figure 10. shows some examples of simple circuits to do this.
With alternative c) one may obtain an interesting solution by dimensioning Rp according to Equation [6] below. The resulting parallel resistance gives a curve that intersects a straight line in three points, as shown in Figure 11.
Failure Modes
Thermistors often have very small sizes and high resistance values. They are sensitive to every โdisturbanceโ in the material. An exposed part of the body is the terminal area, especially for small sizes. If the body isnโt encapsulated in such a manner that any lead bendings are mechanically unloaded before entrance to the thermistor body, it is easy to create small cracks around the lead entrance. With those cracks, the resistance is changed; there also is left a way for moisture and liquids to penetrate the body.
Glaze covered beads and uncoated discs with terminals soldered direct on top of metallized pads are examples of vulnerable designs. Uncoated disc thermistors are not recommended for use in conductive liquids and aggressive gases. The sintered material sometimes undergoes settlings in the crystalline structure. Such events manifest themselves as sudden resistance changes in the magnitude of 3 to 10 % and may be released by heat, temperature changes and mechanical shocks. The failure rate for non-treated delivery lots varies between 30 to 60 %. The cure is a burn-in process that usually is performed as a heat treatment.
Bead thermistors encapsulated in a melted glass body often have small sizes and corresponding thin leads, consisting of alloys that often are difficult to solder. In such events leads intended for spot welding may be the only solution. Caution. Never try to connect NTC thermistors in parallel in order to increase the power dissipation capability. The thermistor that for the moment has the lowest resistance will get a higher current load, a stronger self-heating, a greater resistance decrease, an even higher current load etc., until the avalanche effect will destroy the component.
Reliability
The reliability of NTC thermistors today is regarded as good. It depends not least on serious manufacturers with Statistical Process Control (SPC) based programs for manufacture and verified type qualifications. If we determine that the components are burn-in treated and if we purchase them with hermetic seals, i.e. glass or glass/metal housings, the reliability of such thermistors should be classified in the same group as fixed metallized film resistors.
SMD thermistors eliminate some of the problems connected with sensitive lead terminals. In the beginning there were some solderability problems but today they may be regarded as overcome. We now have got a component that structurally resembles the ceramic chip capacitor, however, with fewer sources of error. The stratified low resistance variant has its electrodes embedded in the material and may from a reliability aspect be comparable to the homogeneous type.
Read more about thermistors measurement system configurations, NTC vs PTC thermistors vs RTD resistor temperature detectors in this article: Thermistor-Based Temperature Sensing System Explained (passive-components.eu)
Nuclear radiation
Tests with radioactive radiation in the form of neutron, ฮฒ and ฮณ radiation show that thermistors are capable of withstanding high intensities without any effects on the characteristics.
PTC Thermistors
PTC (positive temperature coefficient) thermistors are used primarily for overcurrent protection in a variety of electronic equipment applications but are also available in specialty switch applications for degaussing circuits in cathode ray tube TV sets and PC monitors, inrush current limiting in lighting ballasts, motor start circuits for compressor motors and as heating elements for electric heaters.
Ceramic PTC Construction
Ceramic PTC thermistors are primarily made from doped barium titanate. Barium titanateโs basic building blocks are barium carbonate and titanium dioxide. Interaction of semi-conductance and ferro-electricity cause the resistance of the ceramic PTC thermistor to change with temperature. Below a certain Curie point (or transition temperature), the device is in a low resistance state and has a small negative-temperature coefficient. Above the Curie point, the dielectric constant of the material drops, increasing the barrier potential between individual crystals in the structure. Because free electron flow is restricted, the material resistivity rises.
Further temperature increases cause total device resistance to increase exponentially by several orders of magnitude and produces a switch-like response. Ceramic type PTC thermistors are considered reliable and robust and are the technology upon which the global PTC thermistor market was founded. However, in many instances, over the years it has been displaced by disruptive technology in the form of polymer PTC thermistors.
Polymer PTC Construction
Polymeric PTC devices are a low-cost alternative to the ceramic PTC thermistor. Polymer PTCs are made of conductive particles, such as carbon, scattered in a polymer matrix. Resistivity of the material is about an order of magnitude lower than that of ceramic PTC thermistors, which allows operating currents much higher than possible with ceramic thermistors. Under normal operating conditions, little I2R heat is generated and the conductive particles remain in close contact.
When overcurrent occurs, the polymer heats above its transition temperature. The polymer matrix expands, causing the conductive particles to lose contact, which sharply increases device resistanceโa remarkable and exotic solution. As with the ceramic PTC thermistor, I2R heating is normally enough to keep the polymer PTC latched in the high resistance state. The polymer PTC thermistor, which was invented by Raychem of Menlo Park, California (now part of TE Connectivity) is considered new technology. Since the Raychem patent expired due to its reaching the maximum allowable age of a patent, the number of vendors of this technology has blossomed, as is shown in this report.
Differences in the Technology (ceramic vs. polymer)
The primary differences in ceramic vs. polymer technology which is important for the reader to understand from a market perspective is as follows:
Unique Aspects of the Polymer PTC Thermistor
Polymer PTC thermistors are used for overcurrent and temperature sensing applications only. Ceramic PTC thermistors are used for overcurrent applications and temperature sensing but also have created application specific markets such as degaussing of CRT monitors, heater elements and inrush current limiting in motor starting and lighting ballast circuits. They are also used in advanced probe assemblies consumed in the industrial and home appliance markets worldwide.
Unique Aspects of the Ceramic PTC Thermistor
Ceramic PTC thermistors lend themselves to smaller case size production because of their multilayered designs. Polymer PTC thermistors are more reliant upon surface area of extruded polymer sheets and therefore require greater surface area and larger physical case sizes to accomplish their overcurrent protection functions. However, in this version of this essay, we note that the gap between polymer technology and ceramic technology in PTC is narrowing. Ceramic PTC devices are now available down to the 0201 case size (EIA in inches) and polymer chips are now available in the 0402 case size.
PTC Thermistor Manufacturing Process (ceramic vs. polymer)
Ceramic PTC Thermistor Production Process
Ceramic PTC thermistors have been in existence for some time and their development has coincided with the development of television sets, wherein ceramic PTC thermistors were (and are) used for degaussing circuits, although the number of CRT monitor being produced globally in 2023 has dropped dramatically in favor of flat panel displays. This, in turn, has resulted in many Asian vendors of CPTC products to exit the market completely. Ceramic PTC thermistors are produced from ceramic slurries based upon doped barium titanate ceramic materials. Dopants can include magnesium, strontium or other rare earth materials that are included to control resistance. The ceramic is developed captively by the PTC thermistor vendor or purchased from a merchant vendor such as Ferro Corporation.
The ceramic begins as a powder, which is milled, doped and then mixed into aqueous or non- aqueous slurry, which is pressed into a disc shape (in a radial leaded component). Lead wires are attached, the product is sprayed with silver for conductivity and the component is fired in a kiln (otherwise known as a pressed pill process). The end product may be dipped in epoxy or coated with electronic glass for humidity resistance. In a chip design, the process is multilayered stacking of โgreen sheetโ extruded ceramic upon which a layer of precious metal electrode (palladium + silver) is deposited upon each stacked layer. These chips are very small and cannot be distinguished from a grain of salt in their smallest iteration (i.e. the 0402).
Polymer PTC Production Process
The polymer process is much different. The polymer is doped with carbon black materials and melted in a pot to a certain viscosity. It is then extruded into thin polymer sheets. The polymer sheets are then irradiated (mostly by an external vendor, or in the case of TE Connectivity, captively) in a process known as cross-linking. The polymer is then cut into desired lengths and the active material is cut into round or square shapes (radial discs or squares and chips). Lead wires or terminations are attached and the product is dipped in epoxy. Costs to produce polymer PTC thermistors are inherently much lower than that of ceramic, and this gives the PPTC a competitive advantage based upon the most important attribute to the design engineerโprice.
Ceramic and Polymer PTC Components Configurations
The following list illustrates the various ceramic and polymer PTC component configurations and assemblies:
Ceramic PTC Chip Thermistors
The ceramic PTC thermistor can be considered the area of technical growth and development for the ceramic versions of varistors based upon barium titanate technology. Furthermore, the development of increasingly smaller case sizes down below 0402 into the 0201 and 01005 case size ranges are the area of research and development for advanced manufacturers of ceramic PTC thermistors. Applications for ceramic chip thermistors are PCB board mounted for temperature sensing and for overcurrent protection.
Currently case sizes are in the larger 3225 down to the ultra-small 0201 case size. The 0201 is brand new for 2023 and illustrates the technology direction to even smaller sizes. This is a growth market for vendors of ceramic PTC thermistors and many vendors offer a solution. The limitation of such technology is that its size is equal to its technical ability to sense excess current at specific voltages. However, as is the case with ceramic chip capacitors and thick film chip resistors, even the smallest case size products have applications in todayโs ultra-small portable printed circuit boards.
Ceramic PTC MELF Designs
Some ceramic PTC thermistors are offered by the vendor in a MELF configuration, which is considered a surface mound design. Such configurations are manufactured through ceramic extrusion as opposed to stacking and are more cost effective. The designs are cylindrical and have metal terminations. They are preferred by the automotive industry. MELF resistors are also available and would be considered a like product.
Ceramic PTC Degaussers
Another vertically integrated product that employs ceramic PTC technology is the degausser which is used in the degaussing circuit in CRT monitor assemblies. However, this is a dying market as CRT monitors have largely been replaced by flat panel displays which require no degaussing. Small markets still exist for these designs in Turkey, Mexico and Brazil.
Ceramic PTC Thermistor Probe Assembly
The ceramic PTC thermistors are also consumed in the larger probe assemblies, where they are in turn installed in heating and ventilation equipment and in large home appliances (white goods) for thermal sensing. The probe assembly is a surefire way for ceramic PTC thermistor component manufacturers to vertically integrate their component production into the more profitable probe assembly markets. Probe assemblies have high pricing compared to the thermistors that make them work. Many manufacturers of ceramic PTC thermistors have realized this potential profit center and have acquired the equipment and skillsets to manufacture probes in-house.
Ceramic Radial Leaded PTC Thermistors
Radial leaded ceramic PTC thermistors continue to represent the largest market by configuration with respective to ceramic versions of PTC thermistors. Radial leaded designs are consumed in overcurrent protection, thermal sensing and for DC motor protection circuits worldwide.
Ceramic PTC Axial Leaded Designs
Some value added and application specific end-use markets in medical and defense require axial leaded ceramic PTC thermistors either for the purposes of adherence to an established but legacy military specification or because of unique volumetric efficiency requirements.
Ceramic PTC Rods and Disc Elements
PTC thermistors are also sold as bare elements for heating purposes in small home appliances (brown goods) and heating related equipment. The ceramic PTC thermistors in their naked form are manufactured in various shapes that adhere to the requirements of the end-use product and its respective volumetric efficiency requirements. Such shapes include square and round discs and ceramic rods.
Polymer PTC Square Type Radial Leaded
One of the more popular designs in polymer type PTC configurations is the square type PPTC design. These designs are used in industrial and professional electronics applications that require greater current handling than their round counterparts. The square design is clever way to increase the performance parameters of the finished thermistor without incurring much cost. The polymer nature of the thermistor allows for such a square design.
Polymer PTC Round Type Radial Leaded
The round type polymer PTC thermistor represents a large market for the polymer PTC vendors. The round type finds many applications as secondary line card protectors in telecommunications infrastructure equipment worldwide.
Polymer PTC Chip Type Thermistor
The chip type PPTC thermistor is the fastest growth portion of the PPTC segment of the overall thermistor market. The surface mount designs are finding many suitable applications in portable electronics and in applications in computers where the combination of volumetric efficiency requirements and the need for overcurrent protection are present.
Polymer PTC Axial Strap Type Thermistor
The axial strap type polymer PTC thermistor is somewhat unique in the components industry. It is design almost exclusively for battery protection and therefore is round and flat with a tab. In this instance, we see where the configuration of the component is adherent to an intended application (i.e. battery thermal overload protection). The polymer axial strap thermistor represents a significant and growing market worldwide.