Turning 5G wireless communication into a widespread reality will require the use of mmWave frequencies. However, there are many of us RF engineers out there that have spent much of our careers working in the sub-6 GHz range, which actually has quite different needs than mmWave. Therefore, it is critical to get a handle on the key differences between working in this range and mmWave frequencies. Sub-6G and mmWave filter considerations are discussed in article by Peter Matthews, senior technical marketing manager at Knowles Precision Devices published by 5G Technology World.
Three Key Differences Between Sub-6 GHz and mmWave Operations
First and foremost, the rules and specifications, such as those defined by the 3GPP Specification 3GPP TS 38.104 V17.2.0 (2021-06), are different for mmWave. At a high level, this specification defines the frequency ranges where 5G can operate – FR1 (4.1 GHz to 7.125 GHz) and FR2 (24.25 GHz to 52.6 GHz). It also highlights a variety of additional performance requirements that are important to understand when building mmWave base stations and small cells including base station classes, differences in channel bandwidths, and how to test for and handle unwanted emissions.
There are also a variety of different RF design challenges at mmWave largely because as frequency increases, wavelength decreases as shown in Figure 1.
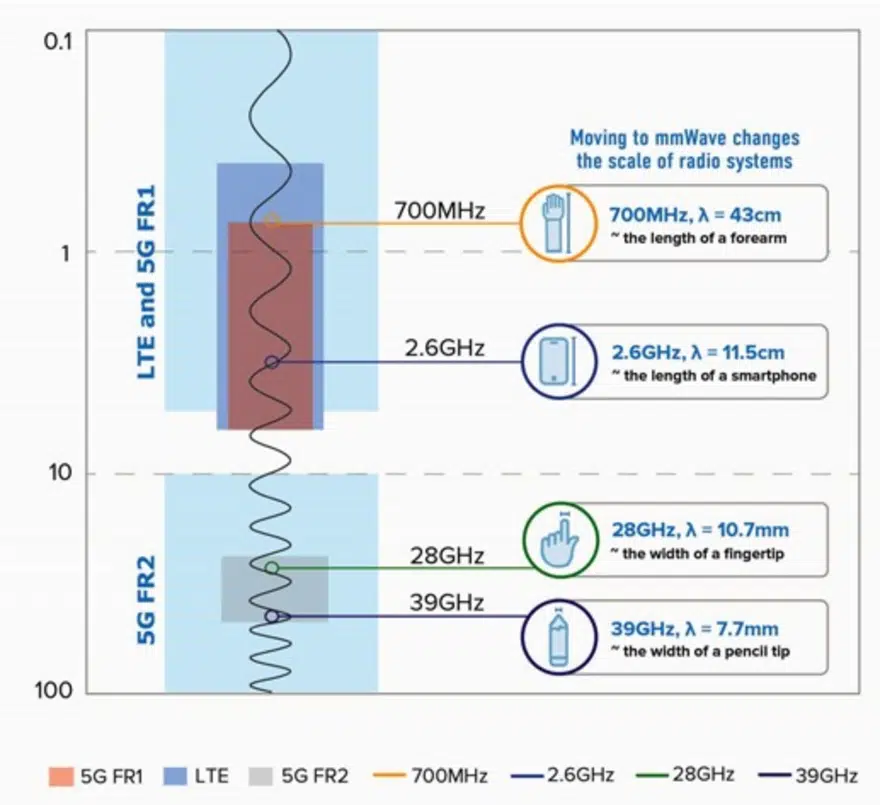
These challenges include the requirement for small form-factor components that do not sacrifice performance, maintaining dimensional tolerances of antenna and filter technologies, and ensuring temperature stability.
The third big difference between devices operating at sub-6GHz frequencies versus those operating in the mmWave range is the different filtering technologies needed at those frequencies. In general, the lumped-element model does not work well at higher frequencies because manufacturing the necessary discrete values will lead to other issues. Instead, at FR2 frequencies, RF engineers are shifting to a distributed element approach. As a result, transmission line and waveguide-based approaches are the best option.
By developing an understanding of these key differences between FR1 and FR2, making the transition to designing mmWave devices will not seem nearly as daunting.
One RF design challenge at these higher frequencies occurs because these designs require small-form-factor components. One of the ways you can achieve this without sacrificing performance is to use high K materials. Table 1 compares the difference in size of a sixth order, half-wave resonator filter built using four different materials.
Because size is at a premium in mmWave applications, dimensional tolerances of antenna and filter technologies also become critical. Poor tolerance encroaches on system performance. You can avoid this issue by using a fully integrated design featuring thin-film technology and a high-permittivity dielectric. This approach lets you shrink the overall size and reduce variation from board tolerances. Additionally, even though integration of passive functions is not overly difficult at lower frequencies, it can be quite complex at higher frequencies.
Another design issue you’ll encounter in densely packed systems arises because there’s no way to control temperature, which means frequent variations may occur and systems will run hot. Therefore, components such as filters must perform within specification over a wide range of temperatures with a temperature stability of approximately 3 ppm/°C.
Different filter technologies
As you move to FR2, you’ll find different radio architectures that include the number and type of filter technologies. Figure 2 shows the typical frequencies and bandwidths of some standard filter technologies and highlights which overlap with the 5G FR1 and FR2 bands.
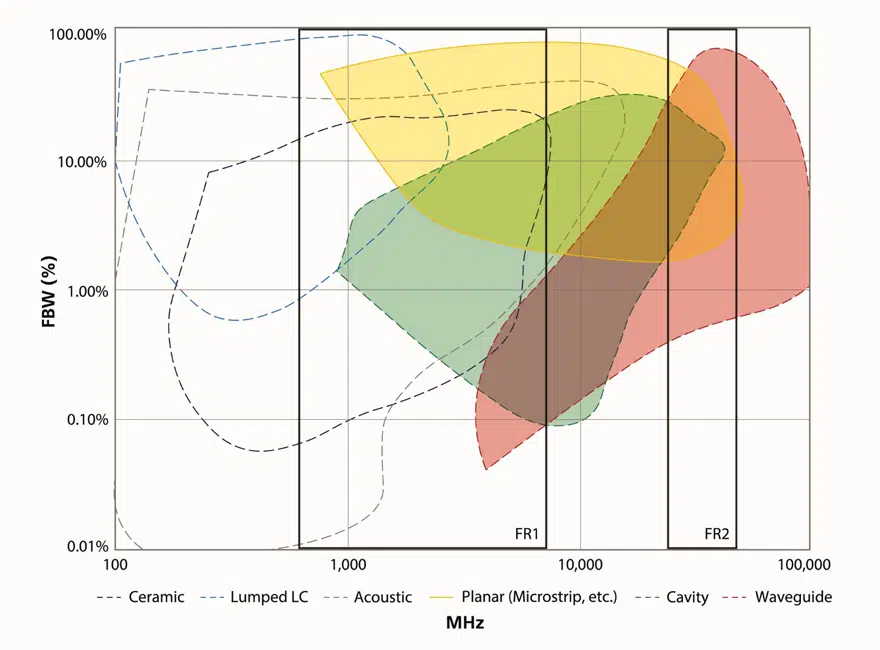
FR2 brings a change from traditional lumped-element filter designs. In general, the lumped-element model does not work well at higher frequencies because manufacturing the necessary discrete values causes other issues. For example, there are board-level parasitic effects that result from mounting components and the transmission lines used in a lumped element model also result in losses. At high frequencies, these effects would essentially detune a filter.
At FR2 frequencies, RF engineers are shifting to using a distributed element model. As a result, transmission lines and waveguides and their corresponding filtering technologies are the best methods for transferring electromagnetic waves around a circuit. More specifically, a microstrip topology is a great option. If you are unfamiliar with microstrip technology, microstrip refers to a type of planar transmission line consisting of a conducting strip separated from a ground plane by a dielectric substrate (Figure 3).
The planar filters used in a microstrip implementation are manufactured using a thin-film process, which offers high Q and a reasonable approach to achieving performance in a small footprint. Planar distributed element filters rely on carefully distributed transmission lines to create resonant structures and can be designed to tighter tolerances than a lumped element filter. This type of planar thin-film implementation is most desirable for mmWave applications from the standpoint of size, cost, and performance.
Making a smooth transition
Even if you’ve been working on RF designs for decades, you should to keep pace with the standards, requirements, and technologies that differ between designing 5G applications that operate sub-6GHz and those at mmWave frequencies.
Instead, to ease this transition, first get to know the 3GPP TS 38.104 V17.2.0 (2021-06) standard. By developing an understanding of these key differences between FR1 and FR2, making the transition to designing mmWave devices will not seem nearly as daunting.