This blog article from Knowles Precision Devices explains cavity filter basics and its advantages in high performance under high power.
As discussed in previous ceramic coaxial resonator filter blog post, resonators are the building blocks used to create filters.
We published a blog post Resonators as Microwave Devices that discussed two different types of resonators – coaxial ceramic and dielectric.
In this post, we will cover the details of a third type of resonator – the cavity resonator.
At a high level, a cavity resonator is designed so that a space, or cavity, is enclosed by a metallic conducting surface, like a metal box. Inside the metal box, the electromagnetic waves reflect between the cavity walls.
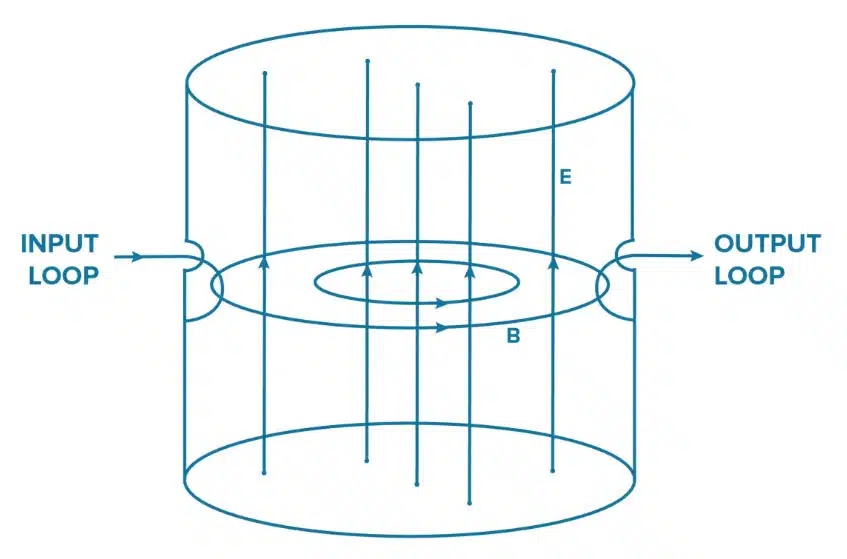
Standing waves are formed at particular frequencies and the cavity resonates at frequencies determined by the size and construction of the cavity. Conductors inserted into the cavity, as shown in Figure 1, allow for energy to be coupled into or out of the cavity.
To use cavity resonators as the building blocks of your filter, you can combine cavities of different characteristics to create the desired filter behavior.
A common type of cavity filter used today is the coaxial cavity filter, which consists of coupled TEM‐mode transmission lines, often metal posts, inside the cavity.
The transmission lines are typically shorted at one end and open on the other, with resonator lengths of less than λ/4. If the resonators are all aligned in the same direction, the filter is called a combline filter. If the resonators are alternating, the filer is called an interdigital filter.
When a Cavity Filter May Be Right for Your Application Needs
In general, cavity filters can be used in devices that operate up to 30GHz while offering high selectivity under high power. While cavity filters are often characterized as large in size, using innovative approaches to cavity construction, we can reduce the size of a cavity filter, making it quite similar to the size of a microstrip or ceramic resonator filter across various frequencies as shown in the graph in Figure 2.
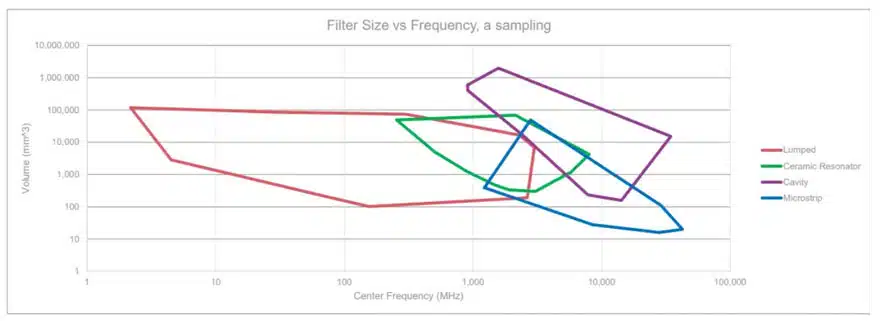
More specifically, for applications operating in the “X” band and above, until about 30 GHz, cavity combline filters can be made quite small, are easy to tune, easy to manufacture, and outperform lumped element options at these frequencies (lumped element designs are still an excellent option for lower frequencies). For operating frequencies above 30 GHz, the required dimensions become too small for a combline construction so we need to use either an interdigital cavity filter option for wide bands, which will cost more to develop, or waveguides for narrowbands.
Cavity Filter Options from Knowles Precision Devices
At Knowles Precision Devices, we use our stable, High Q ceramics to develop ceramic cavity low-loss bandpass filters that are small and have high selectivity. Our typical ceramic cavity filter is 30x smaller than filters designed using waveguide technology. With a multi-port implementation, we can create a very small, robust filter with wide reject band performance without spurious modes. The small shielded nature of our ceramic filter implementation makes it an ideal choice for integration in low noise receiver front ends with the antenna and pre-amplifier. Specs for our off-the-shelf ceramic cavity filters include the following:
- 8 x 0.2 x 0.03 inch for 10 GHz filter
- LO/Multiplier chains/RF pre-select/image filtering
- Low loss in passband: 2-4 dB typical
- Devices scalable from C to Ku band
- Bandwidth 1 to 5 percent
- Narrow footprints are great for switch filter banks
We also make more traditional cavity filters in metal enclosures with the following specs:
- Cavity bandpass for narrow to moderate bandwidths F0 = 200 to 30 GHz for bandpass filters 0.1 to 55 percent wide
- Cavity band reject for narrow bandwidths F0 = 1000 MHz to 30 GHz 0.5 to 15 percent
Our design engineers are also available to work with customers to develop build-to-print or custom cavity filter options that meet your specific application needs.
In general, our cavity filters are well suited for surface mount assembly and are ideal for high-power and high-reliability applications, such as those that may be required for devices used in space.