This article written by Dennis Zogbi, Paumanok Inc. published by TTI Market Eye provides overview and mapping of dielectric raw material supply chain.
Paumanok Inc. employes a vertical research model that has data input resources at each level of the supply chain: mining, materials production and component production as well as component distribution, component consumption and materials recycling.
This creates a legacy of data whereby each segment of the supply chain is a set of checks and balances for data coming from the components markets.
This methodology also provides the best short-term and long-term forecasting model for our predictive analytics.
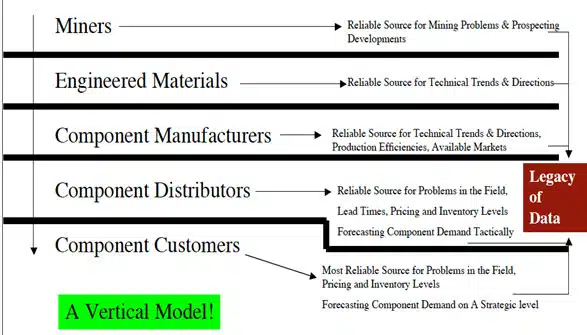
Variable Cost Structure: Costs to Produce Electronic Components
We identified that the costs to produce electronic components are dominated by raw materials which represent a large percentage of overall variable costs to produce. Within these raw material costs there are dielectric raw materials, which account for the largest percentage of overall variable costs to produce for capacitors, which is the largest electrical and electronic component technology and market segment studied.
Dielectric Materials Taxonomy
Paumanok Inc. developed Figure 2.0 below which employs six research spokes that include ceramic, aluminum, tantalum plastic, carbon and exotics.
CERAMICS
The primary dielectric material in the ceramic category is barium titanate, which is manufactured from high purity barium carbonate and high purity titanium oxide. The barium titanate is further mixed with additives to create ceramic dielectric formulations for consumption ceramic capacitors, such as multilayered ceramic chips (MLCC).
Barium Titanate Markets
Barium titanate is the workhorse of the ceramic capacitor industry and is composed of barium carbonate and titanium dioxide. Most barium titanate is produced captively by the ceramic capacitor manufacturers. Most barium titanate has an average dielectric constant of 5,000 (extremely high) and has a low average price per pound compared to other dielectric materials and produce captively by the captive MLCC manufacturers and by merchant vendors of ceramic dielectric formulations. We include all ceramic capacitor chemistries under the barium titanate umbrella and understand that each one is further modified into a capacitor formulation such as X5R, X7R, Y5V and COG/NPO.
ALUMINUM
The aluminum electrolytic capacitor market is large and subsequently has an industry-wide cost of goods sold that is substantial and which depends upon etched and formed anode and cathode foils to create the aluminum oxide dielectric, a solution for high capacitance at high voltage.
Aluminum Oxide: Aluminum oxide is the dielectric layer in aluminum electrolytic capacitors and is achieved with an etched anode foil combined with an etched cathode foil. The foil markets are large and are comprised of thin foil vendors, etching and forming of foil. The foils must be used in conjunction with an electrolyte that is liquid with newer technology based upon the use of dry type polymer cathode coatings known as conductive polymers. The anode + cathode + dielectric paper construction is complex and requires multiple chemical and machining technologies under one roof.
TANTALUM
Tantalum powder and tantalum wire are consumed in the production of tantalum capacitors. Tantalum capacitors are known for their small case sizes with high capacitance and high voltage versions. Tantalum’s ability to hold significant charge is directly proportional to the CV/g value of the tantalum metal powder (capacitance value per gram).
Amorphous Tantalum Oxide: Capacitor grade tantalum metal powder produced using sodium reduction for tantalum electrolytic capacitors. These capacitor product lines require the manufacturer to have achieved large scale chemistry of metal reduction to create the unique structure of tantalum particles.
Hexagonal Tantalum Oxide: Capacitor grade tantalum metal powder for higher capacitance value per gram of material produced using exotic nanotechnology flame synthesis. These powders are associated with conductive polymer type capacitor molded chips.
PLASTIC FILM
The plastic dielectrics are many because of the ease of manufacturing metallized film into film capacitors through machine-winding. Polypropylene and polyester terephthalate are the two primary plastic dielectrics. However, there are eight additional metallized film variations:
- PP-Polypropylene: This dielectric is associated with all electrical systems. The metallized PP film versions are for applications in motor run, X&Y circuits, snubber capacitors and for pulse discharge applications. However, also there are the hazy PP film markets in power transmission and distribution capacitors as well.
- PET-Polyethylene Terephthalate: This dielectric is used in capacitors metallized and is designed for high voltage applications in line voltage equipment such as monitors, power supplies and lighting ballasts.
- PEN-Polyethylene Napthalate: This is a dielectric for capacitors available in standard and high voltage configurations. It is niche for chip film capacitors and is consumed primarily for backlighting in monitors and screens.
- PPS-Polyphenylene Sulfide: This is a high temperature dielectric film used for automotive and industrial applications and also in a chip format.
- PI-Polyamide: An alternative to PTFE for space applications.
- PS-Polystyrene: An alternative to polycarbonate for defense, mil-spec alternatives and industrial variants.
- PTFE-Polytetrafluoroethylene: A specialty plastic dielectric film consumed in space capacitor applications.
- PC-Polycarbonate: A rare dielectric film with a Mil-Spec, hard to manufacture.
- PVDF-Polyvinylidene Fluoride: A rare dielectric film used for pulse discharge applications.
- Siloxane: A rare or emerging high voltage dielectric plastic film.
CARBON
Carbon is associated with supercapacitors, or those capacitors that operate in the Farad range.
Activated Carbon: Activated carbon comes in powder and cloth configurations and have high activation levels and complex surface areas allowing for high storage of charge.
EXOTICS
- Niobium Oxide: Niobium oxide capacitor dielectric was developed as an alternative to tantalum pentoxide dielectric for specific applications.
- Paper (Kraft/Manilla): Paper impregnated with oil is a high voltage dielectric capacitor with a small market in Europe.
- Mica: A high voltage dielectric for harsh environment applications.
- Glass: A military specification capacitor dielectric.
- Silicon Dioxide: The use of ion implantation devices to create dielectrics in silicon.
- Diamond: Diamond and diamond like carbon (see carbon above) are excellent for high voltage applications but are extremely expensive and rare.
Passive Component Maxims:
Raw Materials, Dielectric Materials and Available Surface Area
In every presentation, Paumanok Publications, Inc. emphasizes technical maxims, or scientific truths, associated with capacitors and their economic impact on research and development and mass production. The first maxim: capacitance is required in every electronic circuit and is important, because it supports demand for trillions of pieces produced. Raw materials, especially dielectric materials are an important criteria for market consideration because they contribute a significant amount to the cost of goods sold.
And the second maxim: capacitance is equivalent to the physical size of the finished product (or available surface area) and is important because it places great emphasis for technical change on the raw dielectric materials. For example, the application of nanotechnology and manipulation of raw materials has enabled component miniaturization over time in all capacitor dielectrics.
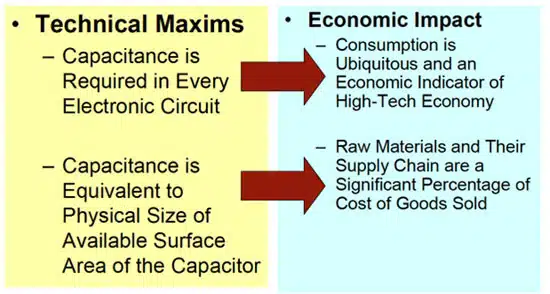
Dielectric Materials Processing by Technology Platform
This chart shows the four main technology platforms associated with capacitor dielectric development:
Multilayered Dielectric Stacking Technology: Multilayer stacking techniques require nanotechnology, which is the precise precipitation of ceramics and metals into small spherical shapes. This is accomplished by oxalate, hydrothermal, plasma arc and sol-gel processes. The ceramic sheets are cast like wet paper with printed electrodes and stacked, diced and fired.
Dielectric Winding Technology: Dielectric winding is largely reserved for aluminum electrolytic capacitors, plastic film capacitors and some types of carbon supercapacitors. It represents a significant portion of the global market with a bent toward the “electrical” supply chain with higher voltage per cell available per anode.
Porous Anode Technology: Tantalum and niobium type capacitors employ the porous anode technique whereby the metal is dissolved creating nooks and crannies inside the structure so that the capacitance layer is increased substantially. This allows for extremely high capacitance in a small footprint/case size.
Exotic Dielectric Technologies: Pressed pill technology is considered here as the method by which SLC— single layered ceramic capacitors—are produced from ready-made ceramic dielectric formulations. Pressed pill technology is also used in non-linear resistors for PTC, NTC and MOV products. Capacitors can also be manufactured from silicon through an ion implantation procedure. These dielectrics are made from silicon and have been employed in the production of integrated passive devices.
Summary and Conclusions
We have identified 20 types of individual dielectric materials contained in six sub-categories. The largest and most popular of these is ceramics, followed by aluminum, tantalum, plastic film, carbon and exotic dielectric materials. The most types of dielectric can be found under plastics, as many types of plastic materials become metallized dielectrics because of their self-healing properties. Exotic dielectrics include the legacy components in niobium, paper, and mica as well as the more exotic materials in silicon and diamond.
The methods by which dielectric materials store charge is based upon their available surface area, which is enhanced through stacking of materials (MLCCs), winding of materials (aluminum, carbon and plastic) or the unique porous anode structure of tantalum.