Researchers in study published by the journal Materials, evaluated the effects of different external factors such as strain, temperature, abrasion, washing, and solder pad size on the electrical resistance of surface-mounted resistor with integrated silver-coated Vectran (SCV) yarn.
Smart textiles have attracted huge attention due to their potential applications for ease of life. Recently, smart textiles have been produced by means of incorporation of electronic components onto/into conductive metallic yarns.
What is an SCV E-Yarn?
Vectran yarn is a fiber spun from aromatic polyester-based liquid-crystal polymer through the polycondensation of 4-hydroxybenzoic acid and 6-hydroxynapthalene-2-carboxylic acid. A silver coating on this fiber enables it for varieties of electronics applications as a smart textile.
Smart textiles are textiles with advanced modifications that enable them to sense and respond to external stimuli. These external stimuli are mostly electronic or photonic in nature. Electronic yarn or E-yarn are used in the healthcare sector, entertainment, fashion, on-body communication, security monitoring, sports activity tracking, and space suits.
Furthermore, microelectronics devices can be easily integrated into these smart textiles through weaving, embroidering, sewing, hybrid soldering, 2D screen printing, 3D printing, and in the form of electrically conductive inks. Also, the mechanical connectors between these smart textiles and microelectronics devices are mostly bolted buttons, socket buttons, hooks, and loops, ribbon cable connectors, crimp connectors, crimp flat-pack connectors, and snap buttons. However, the size of these electronics devices should not be large, otherwise they will damage the fabrics.
The solution to that is the incorporation of SMDs, which are very small, to smoothly embed them into any fabrics without any noticeable bulging or loading on the fabrics.
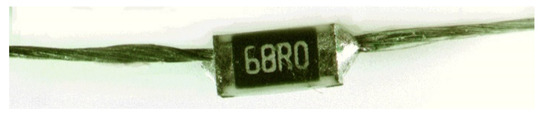
The development, characterizations, and electro-mechanical testing of surface mounted electronic device (SMD) integrated E-yarns is still limited. There is a vulnerability to short circuits as non-filament conductive yarns have protruding fibers. It is important to determine the best construction method and study the factors that influence the textile properties of the base yarn.
Objectives
In this study, researchers fabricated an SCV E-yarn using
- (i) an SCV yarn with two thin layers of silver coatings to make it conductive,
- (ii) a 68 Ω Cermet resistor with 1% tolerance, 0.27 mm length, and 0.04 mm solderable metallic terminal pads
- (iii) a carbon conducive-based solder paste.
They used a temperature-controlled vapor phase reflow soldering method to connect the metallic terminal pads of the SMD to the conductive SCV yarn with the help of a wooden cupboard, which tightly held them together during the process of soldering.
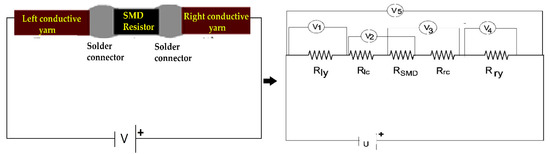
Subsequently, the effect of the gauge length, strain, abrasion, temperature, washing, and solder pad overlap thickness on electrical resistance was measured and algebraically added, followed by measurement of total power loss using the total heat dissipation calculation method.
Observations
The electrical resistance increased linearly with an increase in clamping gauge length at a constant rate per unit length of 2.802 Ω/m. Also, the correlation coefficient of 0.994 and the positive probe factor indicated a significant influence of gauge length on the electrical resistance. Moreover, the relative electrical resistance showed a similar linear relationship with the cyclic strain with a correlation coefficient of 0.99, and the effect was more significant when the strain reached 0.05%.
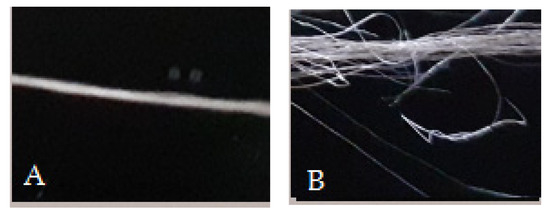
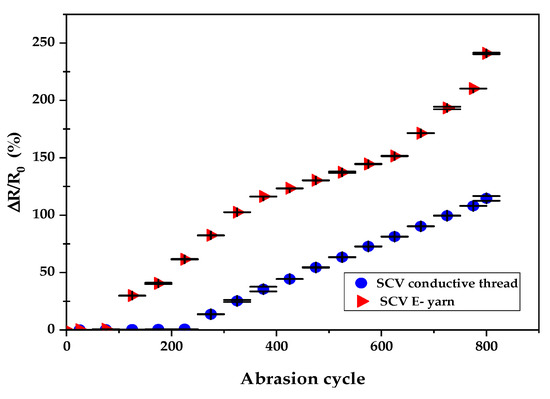
Furthermore, the effect of abrasion was highly significant owing to the formation of cracks, scratches, protruding fibers, and breakage in the outer metallic layer of the SCV conductive yarn, which was evident from optical microscope observations. The noticeable change in electrical resistance started at the 150-abrasion cycle for E-yarn and at the 225-abrasion cycle for SCV. Subsequently, the effects of mechanical abrasion were increased by 240.9% and 114.6% of the SCV E-yarn and SCV conductive yarn, respectively, after the 800-abrasion cycles. A protective coating of thermoplastic polyurethane (TPU) or silicone encapsulation alleviated this issue.
The effect of temperature on electrical resistance had two phases i.e., temperatures below 50 ℃ and temperatures between 50 ℃ to 100 ℃. Up to 50 ℃, the electrical resistance increased very slowly, but after crossing this critical temperature, resistance increased rapidly. The electrical resistance of the SCV conductive yarn and E-yarn between the temperature range of 50 °C to 100 °C increased by 47.49% and 57.99%, respectively.
The electrical resistance of SCV conductive yarn and E-yarn after each washing cycle increased by a magnitude of 6% and 10%, respectively, between 0 to 10 wash cycles. Moreover, due to the formation of an amorphous region in the micro pad connector, the resistance of E-yarn slightly increased from 1.588 to 2.125 Ω when the solder joint pad overlap length increased from 0.5 to 5 mm.
Conclusions
The researchers fabricated an SCV E-yarn setup using a vapor phase reflow soldering method to integrate an SCV conductive yarn and an SMD Cermet resistor.
From all measurements, it was evident that the gauge length and strain linearly increased the electrical resistance. Moreover, after certain critical values, abrasion, temperature, and number of washing cycles had abruptly significant influence on the electrical resistance of both SCV E-yarn and SCV conductive yarn. However, the effect of solder joint pad overlap length was minor. The study suggested coating the SCV E-yarn setup with a protective coating of TPU thermoplastic polyurethane.
Reference
Simegnaw, A., Malengier, B., Tadesse, M., Rotich, G., Van Langenhove, L., Study the Electrical Properties of Surface Mount Device Integrated Silver Coated Vectran Yarn. Materials 2022, 15, 272. https://www.mdpi.com/1996-1944/15/1/272