Resistor types can be divided into categories by various criteria.
The most common splits are by construction types, termination leads, used material or circuit function for applications.
Thick film resistor technologies are the most often used, however what are the advantages, disadvantage compared to other thin film construction and MELF designs ?
Construction
- fixed resistors
- variable resistors (potentiometers, trimmers, rheostats)
- non-linear resistors (thermistors, photoresistors. varistors, magnetoresistors, memristors)
Lead Types
- Chassis Mount
- SMD
- MELF
- Through Hole
- Network
Materials
- carbon film
- carbon composite
- ceramic
- metal element
- metal film and thin film
- metal oxide film
- metal foil
- thick film
- wire-wound
Applications – Circuit Function
- current limiters
- shunt measure
- heaters
- strain gauges
Major Fixed Resistor Technologies
Thin vs Thick vs Foil and MELF Resistors Comparison
Comparing Thin Film vs. Thick Film Chip Resistors
Two of the most common chip resistor types in the market today are thick film and thin film technologies. Some characteristics of these two technologies are the same and some are quite different. Many of the performance differences of these two technologies are apparent from their specifications, but others are more subtle. This document will discuss the manufacturing processes and materials differences to explain how and why the two technologies perform as they do.
Thick Film
Thick Film Manufacturing Process
Thick film chip resistors are manufactured using a screen printing process like the process for screen printing t-shirts which many people are familiar with. The 96% alumina substrate is placed in the printing machine just below the screen and squeegee. The squeegee pushes the screen down to the substrate and pushes the material through the openings in the screen at the precise desired locations for the part design. As the squeegee moves across the substrate, the screen pulls itself away from the substrate leaving the material on the substrate. After each of these processes the material is dried and then fired at high temperature to sinter the thick film material to the substate and create a very robust and reliable electronic component.
The inner conductors, resistive element, dielectric, passivation and marking layers are all applied to a thick film resistor in this way. Prior to passivation, each part is tested and calibrated to its desired resistance value by means of a laser trimming process. Trimming raises the resistance value by removing some of the resistor element in a controlled way that lengthens the current path. Typically, all thick film resistors are manufactured to a resistance value slightly lower than the desired value, such that when they reach the calibration stage, it is easy to trim the parts up to their desired resistance value. This improves yield and helps to control manufacturing costs for this relatively inexpensive technology.
After trimming, a protective passivation layer is screen printed over the resistor element and parts that are 0603 size and larger are marked with their appropriate resistance value. The remaining processes provide the circuit connection through nickel barrier sputtering (vacuum deposition) to connect the top and bottom conductors and plating to provide the 100% matte tin termination for soldering.
MELF Manufacturing Process
Thin Film
Thin Film Manufacturing Process
Thin film chip resistor manufacturing (Figure 5. and 6.) typically starts with screen printing the inner conductors onto the ceramic substrate, drying and firing, like thick film chip resistors. From there the resistive elements are sputtered on in a chamber with very tightly controlled conditions and material targets. These targets contain the thin film metallic elements, in precisely controlled ratios, to produce the intended nominal resistance value. The sputtering process provides a very dense and uniform resistive element that is approximately a thousand times thinner than a comparable thick film element.
For certain resistance values with high precision requirements, photo etching may be used to precisely control the element dimensions and shape. The thin film elements are also calibrated using a laser to trim the element up in value to its desired resistance. The remaining processes are nearly identical to thick film in that the epoxy passivation and marking is applied to protect the resistive element, then the terminations are completed via nickel barrier sputtering to connect top and bottom and plating of 100% matte tin to provide the solderable connection for the PCB.
Thin Film vs Thick Film
Thin film resistive elements have a high density homogeneous metallic alloy that is highly consistent and uniform. This makes the current path through the element very consistent, reliable, and repeatable. Thick film element materials are pastes containing metallic grains combined with glass frit binders, resins, and solvents. When fired, the element has a random nature to its conductive particles throughout the resistor element.
This randomness may lead to inconsistent current paths within the part and contributes to the electrical and environmental stability limitations that thick film technology has. However, the fired thick film element sinters itself to the ceramic substrate and becomes like glass, therefore the element has exceptional moisture stability. The most common thin film resistive elements are alloys containing nickel and chromium (Nichrome) which are susceptible to corrosion from high moisture environments. Only nichrome elements with special processing or tantalum nitride thin film elements resist moisture. See Figure 7.
The trimming calibration process also creates substantial differences in thick film and thin film elements. Thin film resistors, being a metallic alloy with good heat conduction, will accept the laser trimming process with little effect on the material adjacent to the trim. Thick film elements, being glass-like, have poor heat conduction. Therefore, the material adjacent to the trim area will show microcracks where the material was heated as the laser passed through and subsequently cracked as it cooled. These microcracks lead to higher noise, poorer TCR, and higher resistance shift under typical environmental and electrical testing – Figure 8.
Main design differences of thin film vs thick films are shown on the chart below in Figure 9. comparing layer thickness vs achievable square resistance.
MELF capacitors that are also available in (micro)-chip case sizes have its advantage with possible path around the whole chip that makes it more efficient compare to Thick/Thin film SMDs. See the current path example on 0805 chip equivalent in Figure 10. below and pulse load capability comparison in Figure 11.:
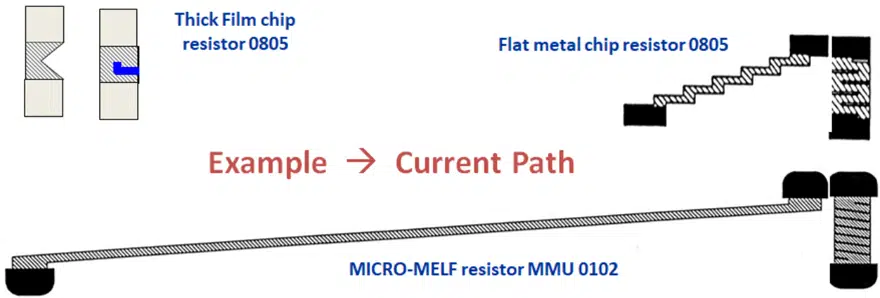
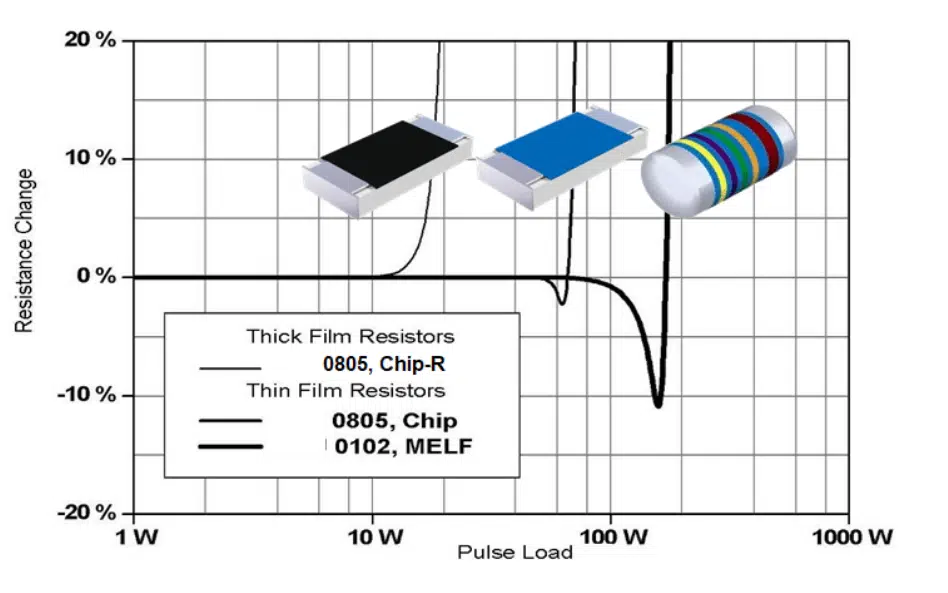
The differences in effective current length path are also reflected in the possible surface loads [W/mm2]. See the Figure 12. below.
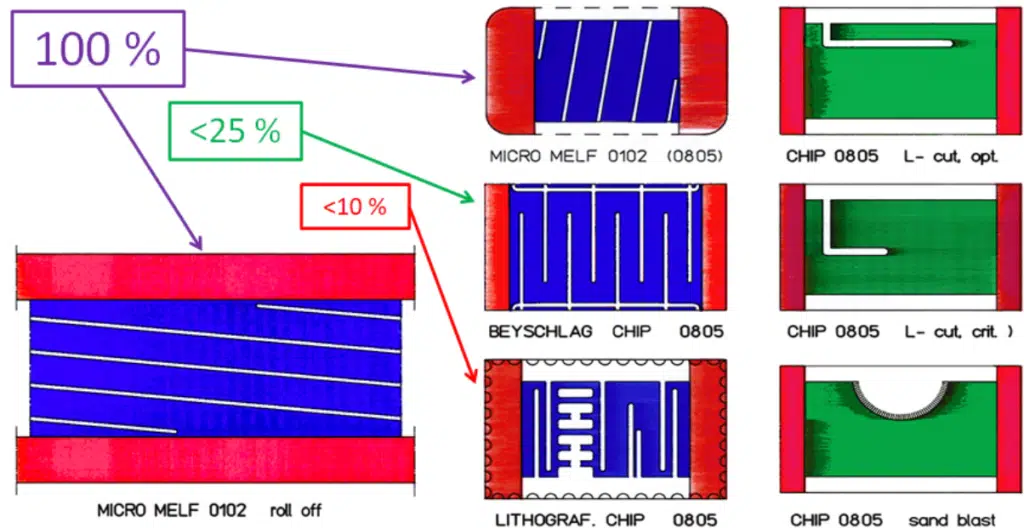
Thin Film vs Thick Film Resistors Stability
In general, thin film designs are providing better longer term stability, lower noise and robustness against soldering heat as shown in the following Figures 13.-15.:

Thick vs Thin Film Summary Comparison
Thin film chip resistors offer the ability to achieve much better TCR and absolute resistance tolerances because of their material uniformity and consistency as well as their calibration process. The significantly higher element material density, the uniformity, and the improved heat conduction of the thin film element all provide better precision, stability, and lower electrical noise with improved high frequency characteristics.
The strength of thick film resistors is low cost, wider resistance range, and inherent moisture withstanding capability. Pulse handling for thin film is better for longer term pulses, but thick film resistors are better for short pulses of 0.0001 second and shorter.