Global Advanced Metals (GAM) introduces high purity tantalum and niobium powders suitable for additive process including Cold Spray technology. The article written by GAM R&D Dr. Matthew Osborne and A. Calvin discusses the powder requirements and features suitable for cold spray technology applications.
The unique bonding interface and lower temperature interaction is opening the door to new material systems and opportunities.
In many applications, heating from weld repair or traditional thermal spray can be detrimental to the substrate, giving cold spray an advantage as an in situ build or repair method. Many excellent references such as Practical Cold Spray can provide overviews and detailed studies of cold spray.
Cold Spray Technology
Cold spray is a variation of thermal spray technology where fine metal powders are carried by a supersonic gas stream to strike a substrate and form a conformal coating. Unlike thermal spray, cold spray particles impact the substrate as solids rather than liquids, and bond due to solid flow
and interlocking of the particles with each other, and with the substrate. Layers can be built to almost any thickness and the varieties of materials and applications are numerous.
Figure 1 shows a general schematic of the cold spray equipment and process.
Cold spray is demonstrating the unique ability to combine materials with different properties (e.g., yield strength, melting point, corrosion resistance) to form graded layers or a blended mixture such as a hard-phase / soft-phase composite for the replacement of electroplated hard coatings.
Applications for Tantalum and Niobium
Tantalum (Ta) and Niobium (Nb) are well known for their corrosion resistance and refractory properties. They are commonly used unalloyed in electronics, electronic components, tantalum capacitors, semiconductor manufacturing, medical, and specialty chemical processing applications where superior properties are required.
A review of literature shows continued testing of cold sprayed Ta and Nb in critical military and energy applications. Due to the nature of these metals, they are easy to forge and roll at low temperature using traditional metal forming methods. This workability has translated to ideal cold spray deposition performance, achieving near fully dense materials with strong, cohesive layers with superior mechanical and corrosion resistant properties.
Forming surface coatings via the cold spray process captures the benefit from tantalum’s and niobium’s corrosion and thermal resistant properties while maintaining the strength, lower weight, and lesser costs of the underlying substrates. For example, a metal-based plate or can be coated with Ta to allow more economical use in acid processing. Many applications for Ta and Nb are known and the general expansion of cold spray will assist in growing the use of these metals and their alloys.
Powder Requirements for Cold Spray
Cold spray is a straightforward process; particles impact a surface at velocities high enough to deform and flatten the particles, expose nascent surfaces for bonding, and fill the surface topography to prevent porosity. A number of operational and material parameters influence this process, and need to be carefully controlled to repeatedly create strong, dense, and continuous coatings with high deposition efficiency (DE = the amount of sprayed powder that is incorporated to the deposit; ~yield).
The key powder characteristics for unalloyed metals include:
- powder flowability
- particle diameter and shape
- particle microstructure and porosity
- gas impurities
- the powder surface
Global Advanced Metals Ta and Nb Powders
Global Advanced Metals (GAM) has a well-known history of producing high-quality Ta and Nb products including flake and agglomerated powders for capacitors, and angular met-grade powder as feed for mill products. GAM has applied the knowledge and capabilities used to develop powders for the semiconductor and capacitor industries now to produce powders with optimized and controlled particle size distributions and chemistry for cold spray applications.
The micrographs in Figure 2 show examples of angular tantalum, tantalum-alloy, and niobium powders developed for cold spray applications.
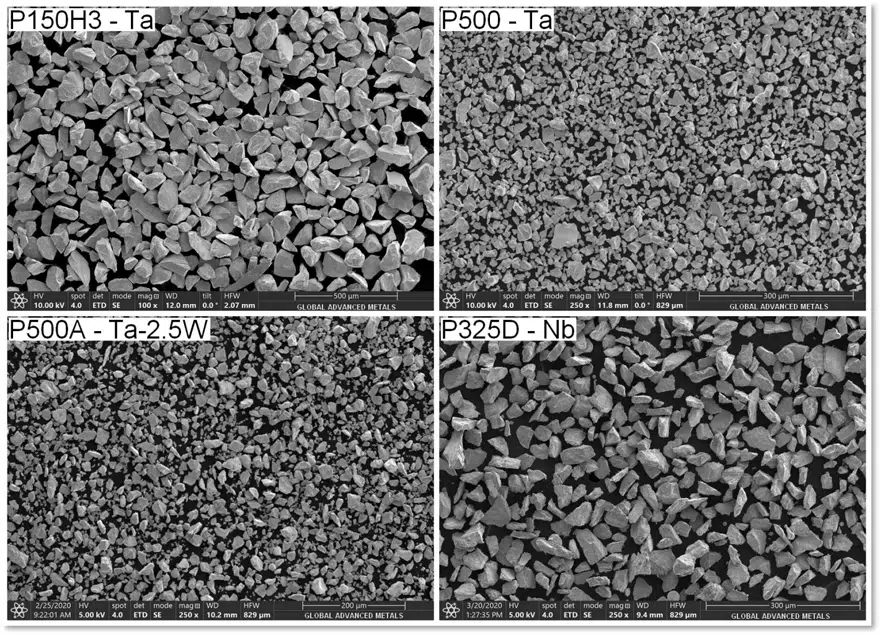
Early cold spray development testing of GAM tantalum powders have demonstrated consistent dense coatings with good bonding and low porosity. The powders used for these tests were larger, spherical particles (A), larger angular particles (B), and smaller angular particles (C). Table 1 shows the powder attributes and Figure 3 shows the feed powders. Cold spray deposition was performed by a collaborator to produce flat coupons, tensile bars, as well as coatings on interior and exterior curved surfaces.
Summary
As previous and emerging research have shown, careful control of powder properties is critical for success in cold spray applications. Early testing has demonstrated that the positive results seen in tantalum and niobium cold spray literature holds true for the high-quality powders produced by GAM.
GAM has extended well-established processing techniques commonly used in the manufacturing of capacitor-grade and metallurgical-grade powders to the tantalum, tantalum alloy, and niobium cold spray powders thus providing superior performance in the form of consistent and controlled particle size distributions, excellent flow, and industry leading chemistry.
Further material development and cold spray testing have been performed and additional results will be shared in future presentations and publications. GAM continues to invest in the development and production of powders designed for cold spray and additive manufacturing and thus will be well positioned to support the anticipated growth in this industry.
Full article in pdf – follow the link: