Vladimir Azbel published article discussing prediction of tantalum capacitor reliability by anode acceptability evaluation. This evaluation aim to improve yield and cost by early stage identification of suspicious parts and improve the capacitor reliability especially for mission critical applications.
Introduction
The anode production process is a multi-factorial process, starting with its calculation, choice of powder supplier, production, and methods of control (CAP, DCL). The behavior of the DCL of the anode depends on the internal stresses formed during the production of the anode (ISPA) and are the cause of aging and, as a consequence, degradation of the DCL.
Today, to evaluate the acceptability of the anode visual control is used: for the presence of cracks, crystallization, and color and WC data, which do not reflect the risk of developing aging processes. Aging processes cause structural changes and respectively, mechanical properties. The SS curve is the easiest way to control the change in the mechanical properties of the material. To estimate the risk of the influence of ISPA, materials science is the approach used, based on the control of changes SS curve, the material before and after heat treatment (heating).
To select the temperature and atmosphere of heat treatment to evaluate the IS, anodes were used, made at the same recipe, which were subjected to heat treatment in the temperature range of 450ยฐC-550ยฐC in the atmosphere: air, nitrogen, vacuum. On anodes before and after heat treatment, mechanical and electrical characteristics were measured. Shown that simultaneous monitoring ISPA with CAP and DCL of the anode, significantly raises the precision of the anode acceptability prediction, for further process.
Abbreviations
- ะขC – tantalum capacitor
- DะกL- leakage currents
- ISPA – the internal stresses formed during the production of the anode
- CM – composite material
- SS curve – stress-strain curve
- ะะขะ – amorphous Ta2O5 dielectric
- IF – zone interface
- FV – formation voltage
Tantalum Anode Mechanical Properties Evaluation
The observed degradation of the DCL TC, in these tests, is due to an increase in the defectiveness of the dielectric coating caused by the aging process of the anode. In production, to evaluate the acceptability of the anode to the further process, visual control is used: for the presence of cracks, crystallization, and colour and WC data, which do not reflect the risk of developing aging processes.
Internal stresses are the main problem in maintaining the stability of the properties of material and construction its reliability under the influence of external factors (temperature, atmosphere, pressure, etc.) during the exploitation of construction, the aging process develops in the material, leading to irreversible changes in the structure of the material and its properties.
To predict the latter, in materials science, methods have been developed that are based on imitation of the accelerated conditions of their operation, similar to those mentioned above for TC. Particular interest is induced to predict the properties of a composite material (CM), where one of its components is protective coatings. The formation of a coating is usually associated with phase transitions, and the generation of new phases, which is one of the reasons for internal stress in CM.
To estimate the stability of the mechanical properties of the material to the external effect, of various appearances, of temperature-force fields, make use of the stress-strain curve (SS curve) The SS curve and the parameters describing it, shown in Fig. 1 are the easiest way to control the change in the mechanical properties of the material. Taking into account that for each region and parameter of the SS curve, mechanisms have been developed, that allows them to be associated with the structure of the material on which depend capacitance CAP, DCL leakage current, and ESR of the anode and, accordingly reliability of the TC.
Mechanisms developed for the SS curve, porous materials, allow monitoring of their structure, from the technological process of production and exploitation conditions Yield strength (Ae) on the SS curve allows you to control changes in the neck size /1,2/, Young’s modulus (E) – porosity /3/, n-strain-hardening exponent -characterize defectiveness of the plastic component of the material /4/, on which the CAP and DCL of the anode depend.
Consequently, a change in any of the parameters used in the production of the anode is reflected in the shape of the CC curve and, accordingly, in its parameters: Ae, E, and n / 5,6,7 / Consider the most general causes of ISPA in the production of the anode. The dielectric coating is an amorphous Ta2O5 (ATO) formed on the surface of the valve material Ta by the anodization-formation.
The anode of the TC imagines how CM consists of a porous product of powder metallurgy with a coating having dielectric properties. The stability of its DCL depends on the keeping of the properties of the coating during the operation of the TC. The use of the stripping procedure TC / 8/ makes it possible to compare not only the behaviour of the DCL in the anodes during testing but also to use the parameters determined from the SS curve of these anodes, see Fig.1, to monitor the structure, responsible for them.
The creation of ATO occurs as a result of the phase transformation of Ta, during the anodization of a sintered pellet, it is accompanied by volumetric changes, which leads to an increase in internal compressive stresses, due to the difference in their volume expansion coefficient, and limitation of ATO growth by the underlying Ta layer Hardness measurements in the amorphous material/metal system (in the anode it is ATO-Ta) formed by anodization showed that the boundary between them is a zone, with increased hardness compared to the polycrystalline and amorphous state, see Fig. 2, let’s call it the interface zone (IF) see fig. 3.1d.
The interface zone makes it possible to โsmooth outโ the difference between the mechanical properties of the amorphous and polycrystalline states, which reduces the risk of local concentration of ISPA and the creation of microcracks. According to /9,10 / for the behavior of ISPA, several main mechanisms are responsible in the interface zone: on the part of the polycrystalline phase, this is due to the generation and movement of dislocations, and on the amorphous phase, compressive elastic stresses and small displacements of nanocrystals.
According to suppose the mechanisms /10/, the source of ISPA can be elastic stresses, nanostructure, dislocation, and defects- such as vacancies, oxides, oxygen atoms, etc. The places of their concentrations, and the influence of the anodization voltage (FV), consider using the example of a model (see Fig. 3), built on the basis of the scheme (see Fig. 2)
According to the diagram, the maximum stresses in the anode are concentrated mainly in the zone of conjugation of Ta and ATO (see Fig. 3.1d). The growth of FV in the neck of the sintered Ta pellet (see Fig. 3.2) leads to a decrease in the cross-sectional area, due to the growth of ATO, up to 40% inside and 60% outside the neck/11/ (see Fig. 3.2b, c).
An analog of the growth of residual stresses in the IF zone (see Fig. 3.1b.c), in the region of the neck cross-section, marked in blue (see Fig. 3.2b, c). An increase in the IF zone is reflected in the shape of the SS curve (see Fig. 3.2d), an increase in its inflection point, and a decrease in the plasticity region, see Fig. 1. The scheme in fig. 3.3d illustrates the situation when the residual stresses indicated, marked brown color, in fig. 3.3 b, c, with an increase in FV, slightly affects the neck cross-sectional area and the changing structure.
This is confirmed by the keep of the shape of the SS curves of the anodes, similar shape of a sintered pellet, and the bend point increases in proportion to FV. Such changes indicate a low risk of aging. The smaller the percentage of the cross-sectional area of the neck Ta before and after anodization, the lower the risk of the influence of ISPA, which can be seen from the comparison of the behavior of the SS curves, with an increase in FV presented in Fig. 3.2 and Fig. 3.3 As can be seen from the diagram (see Fig. 3), the ISPA of the anode depends on the combination of the parameters of the sintered pellet – the diameter of the neck and formation – FV, which is determined – the recipe of the anode.
Recommended Recipe of the Anode
The anode recipe includes: the recipe of the sintered pellet, which depends on the powder, pressing density, sintering temperature/time, and the anodization recipe – on the anodization voltage, current density, temperature, and type of electrolyte The influence of the anode recipe will be illustrated by the following example:
As it can be seen from the diagram (see Fig. 3), the ISPA of the anode depends on the combination of the parameters of the sintered pellet – the diameter of the neck and anodization – FV, which is determined – by the recipe of the anode The anode recipe includes: the recipe of the sintered pellet, which depends on the powder, pressing density, sintering temperature/time, and the anodization recipe – on the anodization voltage, current density, temperature, and type of electrolyte.
The influence of the anode recipe will be illustrated by the following examples: 1. Influence of anodization recipe see fig.4.
Sinter pellets, were prepared at the same recipe and were undergo anodization in 0.01%H3PO4 and 50%Glycol+0.05%H3PO4 at the same condition current and anodization voltage. Pellet after anodization 50%Glycol+0.05%H3PO4 not destructive and pellet after anodization 0.01%H3PO4 destructive.
Using electrolyte with more low conductivity 50%Glycol+0.05%H3PO4 lead decreases the growth rate of film, i.e., decreases create heat during anodization What changed – used an electrolyte with a lower conductivity.
Influence of the recipe of a sintered pellet, see Fig. 5 From fig. 5 can see the influence of the sintering temperature, at the same pressed pellet on the pattern of the destruction of the anodes obtained from them, in the same formation recipes. What changed – was the increase in the sintering temperature.
The reduction in the ISPA of the anode primarily depends on the compatibility of the recipe of the sintered pellet and its formation. According to the proposed model, the change in the shape of the SS curve (see Fig.3.1cr. 2 and 3) depends on the level of ISPA.
The last higher they are, the stronger the reduction of the region plasticity (see fig.1) and the increase in the point of bending (Ae), which is typical for the anode. However, changing the shape and parameters of the SS curve does not allow predicting the effect of ISPA on aging during operation and, accordingly, estimating the acceptability of the anode properties for its further use.
To estimate the risk of the influence of ISPA, materials science is the approach used, based on the control of changes in Ae, the material before and after heat treatment (heating). Heat treatment conditions (temperatures and atmospheres) can correspond to exploitative conditions or simulate their accelerated process, similar Life-test for TC. On the material before and after heat treatment, SS curves are recorded and the yield strength is determined.
The greater the difference between the yield strengths, the higher the risk of aging processes when using the initial material. To estimate the effect of the ISPA anode, will use the mentioned above approach in relation to CM, where the yield strength (Aex) is presented as the sum of each of the materials that make up the composite, taking into account their volume fraction. The presence of a yield point in a material assumes the presence of mobile dislocations, while in ATO and nanostructure they are absent.
Considering the above, the yield stress of the anode is represented by the equation
Aex = Vf*Aff + Vt*Aym + Aint (1)
Aex – yield stress of composite(anode) Aff – fracture strength of amorphous ะขะฐ2ะ5/Thin Solid Films,12(1972) p.319-323 / Aym (Ae) – yield stress of matrix (sintered pellet) Aint – strength interface Vf- volume fractions amorphous Ta2O5 Vt- volume fractions of matrix Consider the effect of heat treatment at 450ยฐC in the air on the change in the parameters included in equation 1. Mainly mechanism responsible for structural changes in the anode at temperatures up to 450ยฐC, under air conditions, is the diffusion of oxygen and oxygen vacancies /12/.
This allows us to assume that the physical thickness and volume fraction of ATO, and the morphology of the porous structure do not change, which involves the permanence of the Aint, Aff, and their volumes fraction in the equation (1) Their changes at the same sintered pellet, depending on the recipe anodization. Therefore, for the change in the shape of the SS curve and Aex, after heat treatment of the anode, is responsible Aym, reflecting the level of stress in the Ta matrix.
Experimental
Consider the effect of heat treatment anode at 450ยฐC/air, on Aym and on the shape of the CC curve and Aex using the scheme, see Fig. 6 in compare cr.1
Since changes in Aex depend on Aym, that changes in the shape of cr. 2,3,4 and 5. relative to cr.1, this reflects the residual stresses in the Ta matrix, after heat treatment.
The greater the difference between their Aex, the higher the risk of aging during operation and the number of TC failures in the Life Test performed from these anodes /13 /. Consider, what temperatures and atmospheres can be used to analyze the ISPA.
To accelerate the diffusion process, use the maximum allowable temperatures for heat treatment of the anode in the air at 450ยฐC, above which ATO crystallization begins; and in a vacuum of 750ยฐC – the beginning of ATO degradation. To select the temperature and atmosphere of heat treatment to evaluate the IS, anodes were used, made at the same recipe, which were subjected to heat treatment in the temperature range of 450ยฐC-550ยฐC in the atmosphere: air, nitrogen, vacuum. On anodes before and after heat treatment, mechanical and electrical characteristics were measured.
It follows from the obtained experimental results that vacuum heat treatment leads to a stronger effect on CAP and DCL compared to air atmosphere and does not cause an increase in the oxygen content (O2). Influence of the heat treatment atmosphere on Aex and AUTS and Cap, DCL, and O2 for anodes made of powder 150kCV, with a pressing density of 5.75 g/cc, sintered and anodization at the same recipe and subjected to heat treatment at 450ยฐC, in an atmosphere of air and vacuum presented in Fig.8.
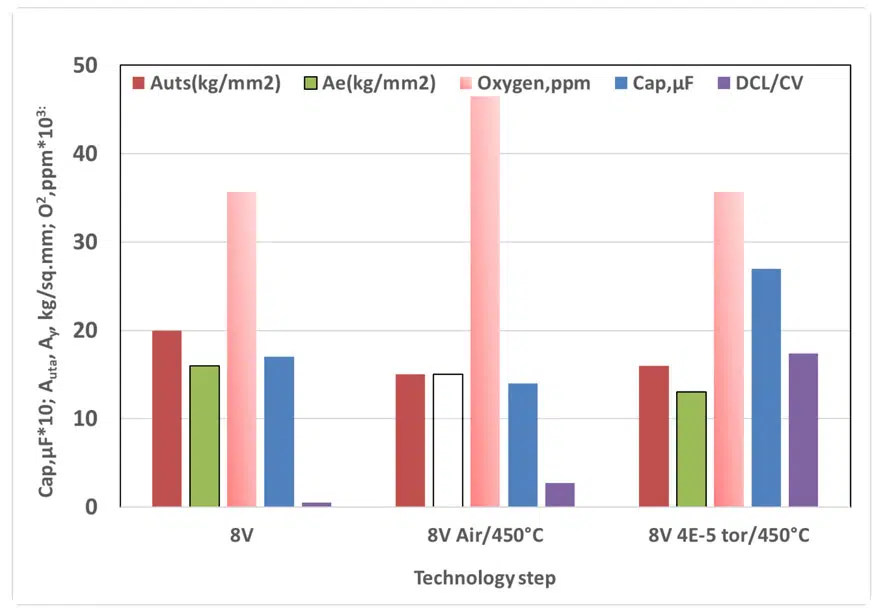
From the data presented in Fig. 8, one can see the different influence of the atmosphere on the mechanical (Aex, AUTS) and electrical (CAP, DCL) characteristics compared to their initial values.
- heat treatment in the air has a dominant effect on the property of the Ta matrix in the anode, which indicates the collapse of Aex (loss of plasticity), an increase in oxygen content, and decrease in CAP, and an increase in DCL.
- in a vacuum, dominant effect, these are processes in the ATO, as evidenced by a sharp increase in CAP and DCL, with minor changes in Aex and AUTS
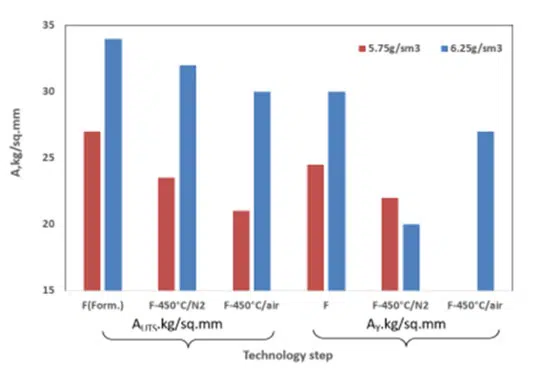
The effect of nitrogen atmosphere and air at 450ยฐะก on the mechanical characteristics of Aex and AUTS for anodes made of 80 kCV/g powder with different pressing densities of 5.75g/cc and 6.25g/cc are shown in Fig.9.
It follows from the obtained experimental results that the heat treatment of anodes, in air conditions, produced with different press densities, leads to the collapse of Aexfor a density of 5.75 g/cc, while not in the case of nitrogen conditions. This behavior of mechanical characteristics can be explained using the diagram in Fig.3. An increase in press density leads to an increase in the size of the neck, which, at the same anodization recipe, should lead to a decrease in ISPA and the risk of oxide creation due to diffusion of oxygen in the stress region.
Let us analyze the obtained experimental results, below the model, assuming that the main mechanism responsible for the structural changes in the anode at temperatures of 450-550ยฐC is the diffusion of oxygen and oxygen vacancies/12/.
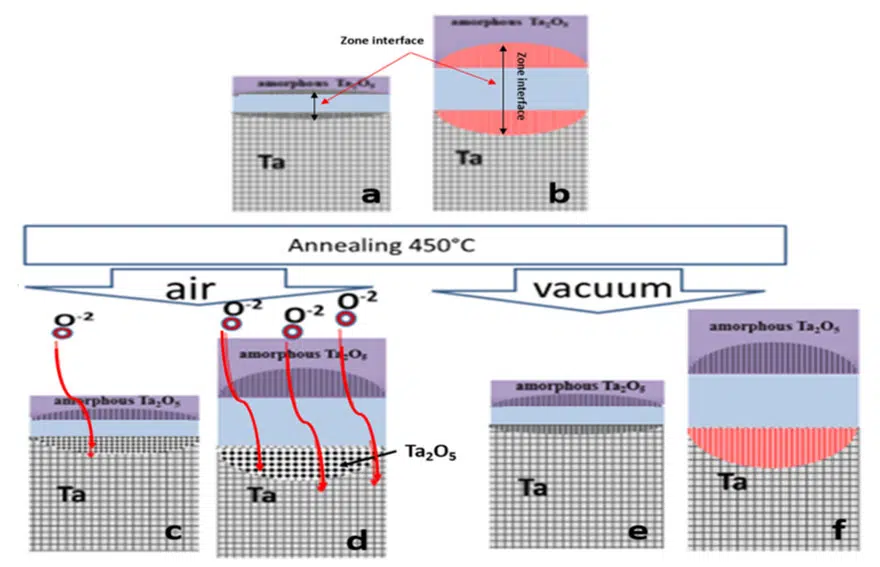
The model illustrates the effect of heat treatment in air and in a vacuum at 450ยฐC, for anodes with different levels of ISPA. The level of ISPA for the most part depends on the concentration of oxygen, its vacancies, and oxygen-containing oxides in the tantalum matrix formed during anode production.
A possible changing the level of internal stress (IS), after treatment at 450ยฐC, is reflected in the behavior of Aex see fig.6. In anodes with a high level of ISPA (see Fig. 10b), heat treatment in air leads to diffusion of oxygen into the interface zone (see Fig. 10b) and the creation of crystalline Ta2O5 oxides (see Fig. 10d) mainly in region b, (see fig. 3.1d.)ย The crystallization increases the residual stress, not only in the Ta matrix but in the film (from 250 to 400 MPa) and Young’s modulus /14 / Thus, the formation of oxides leads to irreversible changes in the structure, which leads to an additional increase in residual stresses and an increase in the average level of internal stresses, and not to their relaxation and toward shape SS curve cr.3 figs.6
As seen in Fig. 8, heat treatment in air at 450ยฐC leads to the collapse of Ae and a decrease in AUTS, which is caused by the creation of crystalline Ta2O5 (see Fig. 10d), and leads to embrittlement of the anode. The very fact of oxygen diffusion from the outside, already means that ATO is defective and, raises the risk of DCL failure. Because defect-free ATO is an anti-diffusion barrier /15/. The decrease in CAP, observed in this case, is due to the presence, of a crystalline Ta2O5 layer between the ATO and the Ta see fig. 10b, which can explain by different dielectric constant: crystalline Ta2O5~ 55-59, and an amorphous ~25-27 Ta2O5 /16 /, which can cause rising dielectric constant anode and decrease in CAP in it.ย ย
The decrease in CAP observed in the article /17/ is associated with the effect of the Ta2O5 crystalline layer. At a low level of ISPA (see Fig. 10a), heat treatment in air at 450ยฐC leads to slight changes in Aex and AUTS, which indicates the absence of irreversible changes in the structure (see Fig. 10c). In this case, heat treatment leads to the relaxation of the ISPA and the recovery of the initial structure. which leads toward the shape SS curves, cr.2,5. Heat treatment of anodes in a protective atmosphere has a dominant effect on the processes in ATO (see Figs. 7 and 8) and has little effect on Aex and AUTS (see Figs. 8 and 9), which retains a high risk of developing aging in the TC.
The growth of CAP and DCL during heat treatment at 450ยฐC in a vacuum is associated with the action of compressive stresses on ATO, from want of oxygen diffusion, for their relaxation. This enhances the processes caused by the concentration gradient of oxygen and its vacancies between IF and ATO and is the reason for the displacement of electrons and field crystallization when exposed to an electric field /18 / The action of a voltage applied to the anode and ISPA, affects the state of electrons, on the ATO-Ta interface, leads amorphous Ta2O5 to Ta2O5_, and reduces the dielectric properties of ATO. As an indicator of the acceptability of the anode to the further process, we use the difference ฮะ = Iะex-ะextI, where ะex is before and ะext is after heat treatment An increase in ฮA leads to an increase in the risk of aging processes.
According to /13/, the deviation of the ratio ฮะ/ะex is not more than 15%, which allows us to consider the anode recipe and the process of its production acceptable, for further production TC.
Summary and Conclusion
The proposed method of mechanical testing allows to separate and quantify the influence of capacitor anode design, and each of the manufacturing processes anode to finish capacitor performance at the earliest manufacturing/design steps.ย The possibility of simultaneous monitoring of the parameters of the SS curve, with CAP and DCL of the anode, rise the precision of the anode acceptability prediction, for further process.
1. A method is proposed for determining the internal stress in the anode, at the stage of its manufacture, using a sufficiently, simple and accessible method based on the registration of the SS curve.
2. Shown, that only the temperature treatment of the anode in the air at 450ยฐะก makes it possible to determine the presence and value change ISPA vs technological process of production
3. The presence of a relationship between the parameters of the SS curve with the morphology of the porous structure of the anode, makes it possible to use the calculation proposed in the work/6 / to find the optimal combination, of the parameters of the recipe anode with internal stresses.
4. The possibility of their control and correction at the anode stage production will save the financial and time costs for the production of TC.
Reference
- The Relationship of B.E.T Surface Area to the Sintering Behavior of Spherical Copper Particles, W.M. Shaffer, International Journal of Powder Metallurgy, vol. 8 no.4, 1972, pp 171-180.
- Characterization of loose powder sintered porous titanium and Ti6Al4V alloy Ziya ESEN, Turkish J. Eng. Env. Sci. 33 (2009) , 207 โ 219
- Correlation between Youngโs modulus and porosity in porous materials J. KOVACIK Journal of materials science letter s 18 (1999) 1007-1010
- Strain hardening behavior in sintered Feโ0.8%Cโ1.0%Siโ0.8%Cu powder metallurgy performs during cold upsetting A Rajeshkannan and S Narayan Proc. IMechE Vol. 223 Part B: J. Engineering Manufacture
- Tantalum Capacitors Reliability, Leakage Current Stability Prediction andย Cost Reduction by Anode Characterization During Manufacturing Process; Vladimir Azbel 3rd PCNS Passive Components Networking Symposium 7 – 10TH SEPTEMBER 2021, MILANO, ITALY
- New Approach to Tantalum Capacitor Anode Design V. Azbel https://passive-components.eu/new-approach-to-tantalum-capacitor-anode-design/. EEE COMPONENTS, PASSIVES
- Quality control sinter pellet an anode, Ta- capacitor, by Mechanical testing V. Azbel on LinkedIn
- Effect of hydrogen on the mechanical characteristics and leakage currents of tantalum anodes, with a reverse voltage applied V. Azbel on LinkedIn Published on July 25, 2020
- Nanocomposite Thin Films for both Mechanical and Functional Applications SAM ZHANG, co-au.
- Physical and mechanical properties of hard nanocomposite films prepared by reactive magnetron sputtering, Invited J. Musil, Chapter 10 in the book “Nanostructured Hard Coatings”,
- Magnesium Vapour Reduced Tantalum Powders with Very High Capacitances, Helmut Haas, CARTS Europe 2004: 18th Annual Passive Components Conference, October 18-21, 2004
- In-Situ Stress Measurement during Heat Treatment of Amorphous Tantalum Oxideย Xin Su,ย ECS Journal of Solid-State Science and Technology,4(7) N64-N69 (2015)
- Tantalum Capacitor Reliability Estimation Based on Anode Screening V. Azbelย https://passive-components.eu/tantalum-capacitor-reliability-estimation-based-on-anode-screening/
- Change of Mechanical Properties of Ta2O5 Thin Film During Crystallization Annealing Ota Hiroyki, Transactions of the Japan Society of Mechanical Engineers v.66, No 650 p.1949-1954,2000
- Diffusion barrier properties of amorphous and nanocrystalline Ta films for Cu interconnects Z. H. Cao, K. Hu, and X. K. Menga JOURNAL OF APPLIED PHYSICS 2009
- Properties of amorphous and crystalline Ta2O5Ta2O5 thin films deposited on Si from a Ta(OC2H5)5Ta(OC2H5)5 precursor C. Chaneliere Journal of Applied Physics 83, 4823 (1998)
- Effect of Dissolved Oxygen on Thermal Oxidation in Ta2O5/Ta Sandwiches YU. POZDEEV-FREEMAN, co-au.ย Journal of Electronic Materials, Vol. 27, No. 9, 1998
- Understanding internal stress evolution mechanisms associated with field crystallization of anodic tantalum oxide Lei Yang, Mark Viste, Joachim Hossick-Schott,ย J Electroceram (2014) 108โ116